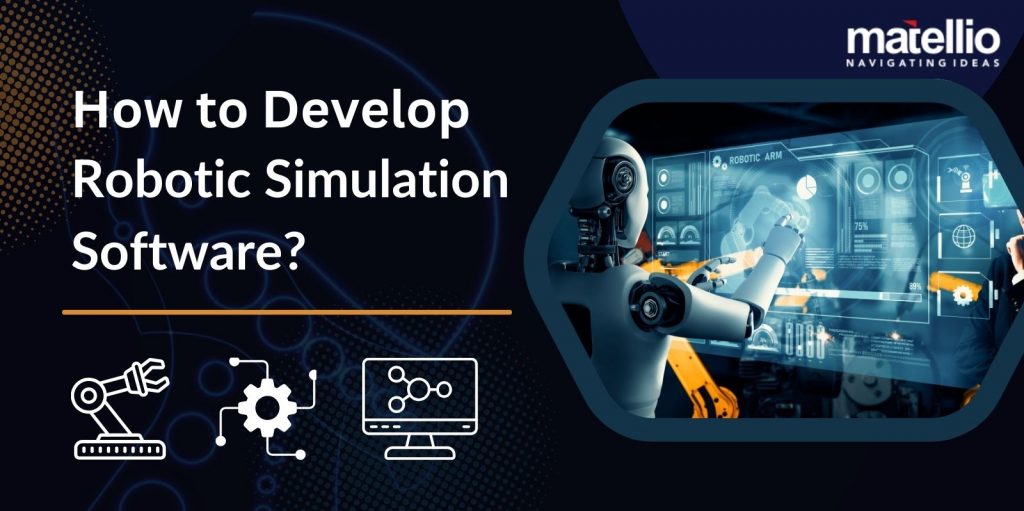
Robotic simulation software is a powerful tool used in various industries, including manufacturing, healthcare, and entertainment, to simulate and visualize robot behavior in different scenarios. By creating virtual environments that mimic real-world conditions, robotic simulation software allows engineers and designers to test and validate robot designs, optimize robot performance, and predict how robots will behave in complex environments.
In this blog post, we will explore robotic simulation software’s capabilities and benefits and its applications in different industries. We will also discuss how robotic simulation software is revolutionizing the way robots are designed, tested, and deployed, leading to more efficient and effective robotic systems.
What is Robot Simulation Software?
Robotic simulation software is software used to control and program robots to execute distinctive tasks or activities. These robots can be physical machines, such as industrial robots used in manufacturing or virtual robots used in simulation environments. The primary purpose of robotic simulation software is to simulate and test robots’ behavior in various scenarios before deploying them in real-world settings.
One of the key features of robotic simulation software is its ability to simulate complex interactions between robots and their environment. This includes factors such as the robot’s movement, the objects it interacts with, and the feedback it receives from its sensors. By simulating these interactions, engineers and developers can evaluate a robot’s performance and adjust its design or programming to improve its functionality.
Market Stats – Robot Simulation Software Market size was valued at USD 15.50 Billion in 2023 and is projected to reach USD 35.06 Billion by 2030, growing at a CAGR of 17.70% during the forecasted period 2024 to 2030.
In addition to simulation and training, robotic simulation software is used for research and development purposes. Researchers use these tools to explore new concepts in robotics, such as advanced control algorithms or novel robot designs. Researchers can quickly iterate on their designs and test them in a safe and controlled setting by simulating these ideas in a virtual environment.
Types of Robot Simulation Software
Robot simulation software enables engineers, developers, and researchers to simulate the behavior of robots in a virtual environment before physical implementation, saving time and resources while ensuring optimal performance. Let’s explore the different types of robotic simulation software and their applications in various industries.
1. Industrial Robot Simulation Software:
Industrial robot simulation software is used to simulate and optimize the operation of industrial robots in manufacturing environments. Industrial robot simulation software tools help design robotic work cells, program robot movements, and optimize robot paths to improve efficiency and productivity.
2. Service Robotics Simulation Software:
Service robotics simulation software simulates the behavior of service robots, such as autonomous drones, delivery robots, and cleaning robots. These tools help test and validate the performance of service robots in real-world scenarios.
3. Medical Robotics Simulation Software:
Medical robotics simulation software is used to simulate surgical procedures and assist in the development of robotic surgical systems. These tools help train surgeons, plan complex surgeries, and improve patient outcomes.
4. Autonomous Vehicle Simulation Software:
Autonomous vehicle simulation software simulates the behavior of autonomous automobiles, such as self-driving cars and drones. These tools help test autonomous vehicle algorithms, validate safety features, and improve vehicle performance.
5. Research Robotics Simulation Software:
Research robotics simulation software is used in academic and research institutions to simulate and study robots’ behavior in various environments. These tools help advance the field of robotics by enabling researchers to experiment with new algorithms and techniques.
6. Educational Robotics Simulation Software:
Educational robotics simulation software is used in schools and universities to teach students about robotics concepts and programming. These tools include interactive simulations and programming environments to engage students and enhance learning.
Robot simulation software plays a critical role in advancing the field of robotics by enabling engineers, developers, and researchers to design, test, and optimize robotic systems in a virtual environment. Whether it’s industrial robots, service robots, medical robots, or autonomous vehicles, simulation software has become an indispensable tool for robotics professionals across various industries. As technology continues to ripen, we can expect to see further advancements in robotic enterprise solutions, leading to more efficient and capable robots.
Build Your Robot Simulation Software with Our Expert Services.
Top Benefits of Robot Simulation Software
Robotic simulation software is revolutionizing the field of robotics by providing advanced programming capabilities and simulation tools that enable developers to create more intelligent and versatile robots. Let’s explore the numerous benefits of robotic simulation software and how it is shaping the future of robotics.
1. Enhanced Development Process
Robotic simulation software allows developers to design and simulate robotic systems in a virtual environment before physical implementation. This enables them to test different configurations, algorithms, and scenarios without the need for costly prototypes, reducing development time and costs.
2. Improved Performance and Efficiency
By using robotic simulation software, developers can optimize robot behavior and performance, leading to more efficient and effective robotic systems. Simulation tools allow for real-time analysis of robot movements, interactions, and tasks, helping to identify and rectify potential issues before deployment.
3. Increased Safety
Robotic simulation software enables developers to test the safety of robotic systems in a virtual environment, reducing the risk of mishaps and damage during the operation. This is particularly beneficial for applications in hazardous environments or those involving human-robot interactions.
4. Scalability and Flexibility
Robotic simulation software allows for easy scalability and flexibility in robot design and development. Developers can quickly modify robot configurations and behaviors to adapt to changing requirements or environments without the need for extensive reprogramming or redesign.
5. Cost-Effective Training and Education
Robotic simulation software provides a cost-effective and safe platform for training and educating robotics professionals. It allows students and researchers to experiment with robotics concepts and algorithms in a realistic simulation environment, enhancing their understanding and skills.
6. Realistic Simulation
Robotic simulation software provides a highly realistic simulation environment, allowing developers to test robot behavior in complex and dynamic scenarios. This enables them to evaluate their robots’ performance in real-world conditions, ensuring robustness and reliability.
Robotic simulation software offers numerous benefits for developers, researchers, and educators in robotics. Its potential is vast, from enhanced development processes and improved performance to increased safety and cost-effective training. As robotics continues to evolve, digital transformation services will play a vital role in shaping the future of robotics and unlocking new possibilities for intelligent and versatile robots.
Key Features of Robot Simulation Software
This state-of-the-art technology delivers a broad spectrum of features that enable engineers and researchers to develop and optimize robotic systems precisely and efficiently. Let’s delve into the key features of robotic simulation software and how they contribute to the advancement of robotics.
1. Real-time Monitoring
Robot simulation software provides real-time monitoring of robotic systems, allowing engineers to visualize and analyze data as it is generated. This feature allows quick identification and resolution of issues, ensuring optimal robot performance.
2.Task Scheduling
With task scheduling capabilities, robot simulation software allows engineers to program and schedule tasks for the robot. This feature is essential for coordinating complex operations and optimizing the robot’s efficiency.
3. Motion Control
Robotic simulation software offers motion control features that enable engineers to simulate and test different motion trajectories for the robot. This feature helps in optimizing the robot’s movements for maximum efficiency and accuracy.
4. Sensory Feedback
By simulating sensory feedback, robot simulation software enables engineers to test the robot’s ability to sense and respond to its environment. This feature is crucial for developing robots that can interact effectively with their surroundings.
5. Environment Mapping
Robotic simulation software allows engineers to create detailed maps of the robot’s environment, including obstacles and other features. This feature helps plan and optimize the robot’s navigation path.
6. Autonomous Navigation
With autonomous navigation capabilities, robotic simulation software enables engineers to develop robots that can navigate and operate independently in complex environments. This feature is essential for applications such as autonomous vehicles and drones.
7. Object Recognition
Robotics simulation software includes object recognition capabilities that help robots recognize and interact with things in their environment. This feature is crucial for applications such as robotic pick-and-place operations.
8. Human-Robot Interaction
Robotic simulation software allows engineers to simulate and test human-robot interaction scenarios. This feature is essential for developing robots that can work safely and effectively alongside humans.
9. Data Logging
Robot simulation software enables engineers to log and analyze data from robotic systems. This feature helps in identifying trends and patterns in the robot’s behavior, leading to improvements in its performance.
10. Simulation
Robotics simulation software provides a realistic simulation environment, allowing engineers to test and validate their robotic systems before deployment. This feature helps reduce costs and risks associated with real-world testing.
11. Multi-Robot Coordination
Robotic simulation software includes features for coordinating numerous robots to operate jointly towards a shared goal. This feature is essential for applications such as swarm robotics and collaborative manufacturing.
12. Error Handling
With error-handling capabilities, robotic simulation software allows engineers to simulate and test the robot’s response to errors and failures. This feature helps in developing robust and reliable robotic systems.
13. Integration Capabilities
Robot simulation software offers integration capabilities with other software and hardware systems, enabling seamless data exchange and communication. This feature is crucial for integrating robots into existing workflows and systems.
14. Customization Options
Robotics simulation software provides customization options that allow engineers to tailor the software to meet their specific requirements. This feature enables the development of highly specialized robotic systems for various applications.
Robotic simulation software offers a wide range of features that enable engineers and researchers to develop, test, and deploy robotic systems with precision and efficiency. By leveraging these features, robotics is advancing rapidly, opening new opportunities for automation and innovation across industries.
Use Cases of Robot Simulation Software
Robotic simulation software is revolutionizing various industries by enabling organizations to simulate, test, and optimize robotic systems before actual deployment. Let’s explore the industry-wise use cases of robot simulation software and how it is transforming operations across different sectors.
Manufacturing:
In the manufacturing industry, robotic simulation software designs and optimizes robotic assembly lines. Manufacturers can simulate different production scenarios, optimize robot trajectories, and improve cycle times. This software also helps in identifying and resolving potential bottlenecks in the production process.
Automotive:
In the automotive industry, robotic simulation software is used for designing and testing robotic welding, painting, and assembly processes. It enables manufacturers to optimize robot placements, minimize production expenses, and assure product quality and consistency.
Healthcare:
In the healthcare industry, robotic simulation software trains medical professionals and develops robotic surgical procedures. Surgeons can simulate complex surgeries, practice on virtual patients, and refine their techniques before operating on real patients, leading to improved surgical outcomes.
Logistics and Warehousing:
In logistics and warehousing, robot simulation software optimizes warehouse layouts, automates material handling processes, and improves inventory management. It helps reduce functioning expenditures, improve efficiency, and ensure timely delivery of goods.
Aerospace and Defense:
In the aerospace and defense industry, robotics simulation software is used for designing and testing uncrewed aerial vehicles (UAVs), also known as drones. It enables engineers to simulate flight missions, test aircraft performance, and optimize flight paths, leading to safer and more efficient UAV operations.
Construction:
In the construction industry, robot simulation software is used for designing and planning construction projects. It enables engineers to simulate construction processes, optimize resource allocation, and identify potential safety hazards before starting construction, resulting in more efficient and safer construction practices.
Education and Research:
In the education and research fields, robotic simulation software is used to teach robotics concepts and conduct research on robotic systems. Students and researchers can simulate robotic behaviors, experiment with different algorithms, and develop new robotic applications in a virtual environment.
Robotic simulation software is a versatile tool that is transforming operations across various industries. By enabling organizations to simulate, test, and optimize robotic systems, industrial automation and robotics software is helping to improve efficiency, lower expenses, and steer innovation across industries. As technology continues to progress, the use cases of robotic simulation software are expected to expand further, leading to more sophisticated and efficient robotic systems in the future.
Technology Trends in Robot Simulation Software
As technology continues to evolve, several key trends are shaping the future of robotic simulation software. Let’s explore the latest trends in this exciting field.
Realistic Simulation Environments
Robot simulation software is becoming increasingly sophisticated, offering realistic 3D environments that accurately simulate real-world conditions. 3D robot simulation software allows engineers to test and validate robotic systems in virtual environments before deployment, reducing costs and risks associated with physical testing.
Integration with AI and Machine Learning
AI and machine learning are revolutionizing robotic simulation software, enabling robots to learn and adapt to their environments. By integrating AI algorithms, simulation software can generate more intelligent and autonomous robotic behaviors, leading to more efficient and versatile robotic systems.
Cloud-Based Simulation
Cloud computing is transforming the way robot simulation software is deployed and managed. Cloud-based simulation platforms offer scalability, accessibility, and collaboration features, allowing users to access and share simulation data anywhere.
Digital Twin Technology
Digital twin technology is being integrated into robotics simulation software, enabling engineers to create virtual replicas of physical robots. This allows for real-time monitoring, predictive maintenance, and optimization of robotic systems, improving performance and reliability.
Human-Robot Collaboration
Robotic simulation software is enabling closer collaboration between humans and robots in shared workspaces. By simulating human-robot interactions, engineers can design safer and more efficient robotic systems that can work alongside humans in various industries.
Simulation-Based Training
Simulation-based training is gaining popularity in robotics. It allows operators to train on virtual robots before operating real ones. This improves safety, reduces training costs, and accelerates the learning curve for new operators.
Optimization for Industry-Specific Applications
Robotics simulation software is being optimized for specific industries, such as manufacturing, healthcare, and logistics. These industry-specific solutions offer tailored features and functionalities to meet each industry’s unique requirements.
The field of robot simulation software is rapidly growing, propelled by refinements in technology and a growing demand for more intelligent and efficient robotic systems. By embracing technology consulting services, engineers and developers can unlock new possibilities in robotics and automation, paving the way for a more interconnected and automatic future.
Experience the Unparalleled Accuracy with Tailored Robot Simulation Software Tools.
Challenges and Solutions of Robot Simulation Software Development
Robotic simulation software development comes with its own set of challenges. Let’s investigate the pivotal challenges faced in robot simulation software development and discuss potential solutions to overcome them.
Complexity of Robot Behavior: Robots exhibit complex behaviors that are difficult to simulate accurately. Capturing the nuances of robot behavior in a simulation environment requires advanced modeling and simulation techniques.
Solution: Use advanced modeling techniques, such as physics-based modeling and machine learning, to accurately capture robots’ behavior in simulation.
Realism of Simulation: Achieving a high level of realism in simulation is challenging, as it requires modeling a wide range of physical and environmental factors that can affect robot performance, such as friction, gravity, and sensor noise.
Solution: Invest in high-fidelity simulation environments that can replicate real-world conditions with high accuracy, including realistic physics and environmental factors.
Computational Complexity: Simulating complex robotic systems can be computationally intensive, requiring powerful hardware and efficient algorithms to ensure real-time performance.
Solution: Utilize parallel computing techniques to distribute simulation tasks across multiple processors, improving computational efficiency and enabling real-time simulation.
Integration with Hardware: Connecting simulation software to physical hardware, such as robots and sensors, can be challenging due to compatibility points and the requirement for accurate data synchronization.
Solution: Use standardized interfaces, such as ROS (Robot Operating System), to facilitate the integration of simulation software with physical hardware and other software components.
Scalability: As robotic systems become more complex, the scalability of simulation software becomes increasingly important, requiring software that can handle large-scale simulations efficiently.
Solution: Leverage cloud computing resources to scale up simulation capabilities as needed, enabling large-scale simulations without the need for expensive hardware investments.
Robotics simulation software development presents its own challenges; these challenges can be overcome with the right technique and mechanisms. By investing in advanced modeling techniques, high-fidelity simulation environments, and efficient computing resources, a professional AI development company like Matellio help to create robust and effective robotic simulation software that accelerates the development and deployment of robotic systems.
Steps of Robot Simulation Software Development
Robotic simulation software plays a crucial role in developing and testing robotic systems, enabling engineers to design, simulate, and validate robotic applications before deployment. Let’s explore robotic simulation software development and the key steps involved in creating these complex systems.
Define Requirements
The first step in robot simulation software development is to define the requirements based on the intended use case. This includes determining the type of robots to be simulated, the environment in which they will operate, and the tasks they will perform.
Design Architecture
Next, the software architecture is designed, considering the requirements and underlying technologies. This includes determining the programming languages, frameworks, tools to be used, and overall system architecture.
Develop Core Functionality
The core functionality of the robot simulation software is then developed, including features such as robot modeling, simulation environment creation, and task planning. This involves implementing algorithms for robot control, collision detection, path planning, and sensor simulation.
Implement User Interface
A user interface is developed to allow users to interact with the simulation software. This includes designing graphical interfaces for robot visualization, environment editing, and simulation control.
Integrate Sensors and Actuators
The simulation software is integrated with sensors and actuators to simulate the robot’s interaction and environment. This includes simulating sensor data such as camera images, lidar scans, proximity sensors, and actuator control signals.
Test and Validate
Once the software is developed, it is tested and validated to ensure it meets the intended requirements and functions. This includes testing the simulation software with different robotic systems and environments to verify its accuracy and reliability.
Deploy and Maintain
Finally, robot simulation software is deployed for use in various applications, such as robotics research, education, and industrial automation. Ongoing maintenance and updates are also performed to ensure the software remains compatible with new technologies and requirements.
The robotics simulation software development process is complex and requires expertise in robotics, software development, and simulation technologies. By following a structured approach and leveraging advanced tools and techniques, developers can create high-quality robotic simulation software that accelerates the development and deployment of robotic systems.
Best Simulation Software for Robotics
Robotics simulation software solutions enable users to design, simulate, and optimize robotic systems, leading to increased efficiency, reduced costs, and improved safety. Let’s explore today’s top robotic simulation software and its key features.
RoboDK
RoboDK is a powerful and versatile robotic simulation software that allows users to simulate and program industrial robots for various applications. It supports a wide range of robot brands and models, making it suitable for a variety of industries. RoboDK’s key features include offline programming, collision detection, path optimization, and robot calibration.
Visual Components
Visual Components is a coplete 3D manufacturing simulation software that allows users to design, simulate, and optimize their manufacturing processes. 3D robot simulation software offers a wide range of tools for modeling robotic systems, including robots, conveyors, and workstations. Visual Components’ key features include drag-and-drop simulation, robot path planning, and virtual commissioning.
Epson RC+ Robot Simulation Software
Epson’s RC+ software is designed for use with Epson robots and offers a complete set of tools for simulation, programming, and optimization. RC+ enables users to simulate robot movements, test different scenarios, and optimize robot paths, all within a user-friendly environment.
Siemens Process Simulate
Siemens Process Simulate is a leading simulation software used for the virtual commissioning of robotic systems. Siemens robotics simulation software allows users to create detailed 3D simulations, test robot programs, and validate system behavior, helping to reduce commissioning time and costs.
RobotStudio
RobotStudio is a leading abb robot simulation software developed by ABB. It allows users to simulate and program ABB robots for various industrial applications. RobotStudio’s key features include 3D modeling, collision detection, path optimization, and virtual commissioning.
V-REP (Virtual Robot Experimentation Platform)
V-REP is a versatile and extensible robotic simulation software that is widely used in research and education. It offers a wide range of features for simulating robotic systems, including robots, sensors, and environments. V-REP’s key features include a customizable physics engine, realistic 3D graphics, and a complete API for integration with external software.
FANUC ROS Simulation
Fanuc robot simulation software is flexible and powerful robotic middleware widely used in research and industry. It offers a wide range of tools and libraries for building robotic systems, including simulation capabilities. ROS’s key features include a modular architecture, support for various robot platforms, and a large and active community.
Robotic simulation software plays a crucial role in modern robotics, enabling users to easily design, simulate, and optimize robotic systems. The software solutions mentioned above are some of the best options available today, offering a wide range of features and capabilities for various industries and applications. Whether you are a manufacturer looking to optimize your production process or a researcher exploring new robotics technologies, these tailored software solutions can help you achieve your goals efficiently and effectively.
Why Choose Matellio for Implementing Robot Simulation Software
This transition can be smooth and beneficial with the right software partner, such as Matellio. Here are several reasons why choosing Matellio for implementing robotic simulation software is a smart choice:
Expertise and Experience: Matellio has a team of experienced professionals who specialize in developing and implementing robotic simulation software. Their expertise ensures that the software is tailored to meet your organization’s specific needs and requirements.
Customized Solutions: Matellio understands that every organization is unique, with its own set of challenges and requirements. They offer customized solutions that are designed to address these specific needs, ensuring that the software integrates seamlessly into your existing processes.
Cutting-edge Technology: Matellio stays abreast of the latest trends and advancements in robotic simulation software. They incorporate cutting-edge technology into their solutions, ensuring your organization benefits from the most advanced features and functionalities.
Cost-effective Solutions: Implementing robotic simulation software can be a significant investment. Matellio offers cost-effective solutions that provide excellent value for money, helping you maximize your return on investment.
Quality Assurance: Matellio is committed to delivering high-quality software solutions. They follow stringent quality assurance processes to ensure that the software meets the highest performance and reliability standards.
Customer Support: Matellio provides complete customer support services to assist you throughout the implementation process and beyond. Their team is available to answer any questions or address any issues you encounter.
Proven Track Record: Matellio has a proven track record of successfully implementing robotic simulation software for organizations across various industries. Their portfolio of successful projects is a testament to their expertise and capabilities.
Choosing Matellio to implement robotic simulation software is a wise decision. Their expertise, customized solutions, cutting-edge technology, cost-effective solutions, quality assurance, customer support, and proven track record make them the ideal partner for organizations looking to enhance their manufacturing processes with robotic simulation software.
Conclusion
Robotic simulation software is revolutionizing the field of healthcare and rehabilitation by offering innovative solutions for patients with neurological disorders and injuries. These software applications provide customizable and interactive therapy sessions that can be tailored to individual needs, helping patients regain mobility, improve motor function, and enhance overall quality of life.
The versatility and effectiveness of robotic simulation software are evident in its ability to be integrated into various healthcare settings, including hospitals, rehabilitation centers, and even home-based care. By combining advanced robotics with interactive software, healthcare providers can deliver personalized and engaging therapy sessions that maximize patient outcomes and minimize recovery time.
As technology continues to advance, robotic simulation software has immense potential to improve patient care and outcomes. Continued research and development in this field will likely lead to even more innovative solutions that enhance the lives of patients with neurological disorders and injuries.
Robotic Simulation Software – FAQs
Q1. Why is robotic simulation important?
This addresses the significance of using simulation in robotics. Simulation allows developers to iterate more quickly, test various scenarios, and refine algorithms before deploying them on real hardware. It also reduces costs associated with hardware experimentation and facilitates safer testing.
Q2. Is robotic simulation software open-source or proprietary?
Users might be interested in the licensing models of different simulation tools. Some open-source software allows for community contributions and customization, while others are proprietary, with commercial licenses offering additional features and support.
Q3. How can I contribute to robotic simulation software development?
This addresses opportunities for individuals to participate in improving existing simulation platforms or developing new ones. Contribution avenues may include code contributions, bug reporting, documentation writing, or participating in community discussions and events.
Q4. How does robotic simulation software integrate with real-world hardware?
Users might want to know how simulation software interfaces with physical robots. Integration methods vary but may include exporting simulation results to real robots, using simulated robots to control physical hardware, or connecting simulation environments to external sensors and actuators.