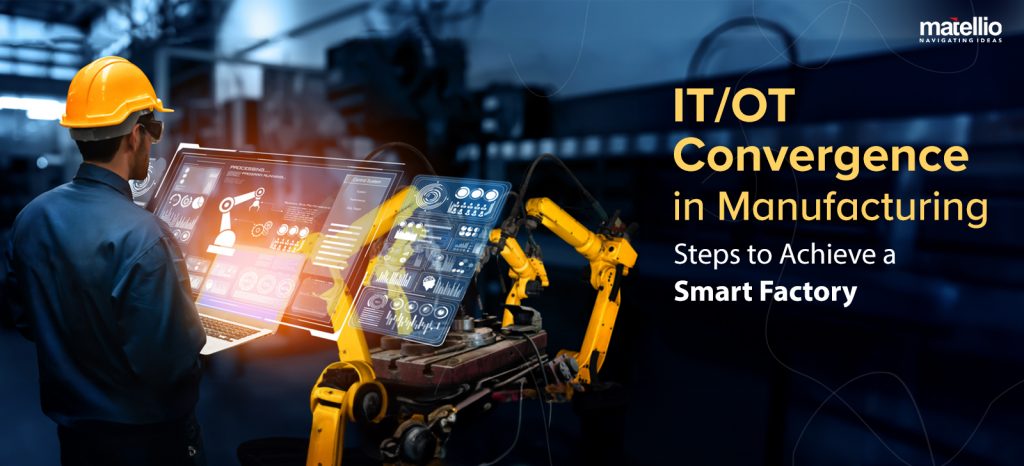
Is your manufacturing operation struggling with:
- Limited visibility into production processes?
- Rising operational costs?
- Slow decision-making due to fragmented data and disconnected legacy systems?
Well, you are not alone! Approximately 56% of manufacturers reported a lack of data integration as a significant barrier to their digital transformation efforts. But what could be the solution to such problems? Enters IT/OT convergence in manufacturing!
In today’s competitive landscape, traditional manufacturing setups are reaching their limits. The answer lies in IT/OT convergence, the strategic integration of Information Technology (IT) and Operational Technology (OT).
This convergence bridges the gap between data-centric computing (IT) and the systems that manage and monitor physical processes (OT).
By creating a unified platform for data exchange and analysis, IT/OT convergence empowers manufacturers to gain real-time insights into production processes, optimize resource utilization, boost productivity through automation, and reduce operational costs. Intrigued?
Let’s uncover more IT/OT convergence benefits and discover how you can implement it in your manufacturing operations. We will also check the IT/OT convergence challenges and how Matellio can help you resolve them effectively!
What is IT/OT Convergence?
IT/OT convergence refers to the integration of Information Technology (IT) systems with Operational Technology (OT) systems. Here’s a breakdown of each:
IT Systems
These are the data-centric systems that manage information flow within an organization. They include things like enterprise resource planning (ERP) software, databases, and communication networks.
OT Systems
These are the systems that monitor and control physical devices and processes. In manufacturing, this could include Programmable Logic Controllers (PLCs) that manage robots, sensors that track machine performance, and Human-Machine Interfaces (HMI) used for operator control.
Traditionally, IT and OT systems operated in silos, with limited communication between them. However, the rise of Industry 4.0 and the demand for more agile and responsive manufacturing processes have highlighted the need for these two domains to converge. By integrating IT and OT, manufacturers can leverage real-time data, enhance decision-making, and optimize operations across the board.
IT/OT convergence in manufacturing simply means breaking down barriers between the information systems (data) and the systems that control the machines (operations). This lets factories use data to fine-tune production, identify issues faster, and ultimately manufacture smarter.
Why Now is the Time to Implement IT/OT Convergence in Manufacturing – IT/OT Convergence Benefits
Imagine your factory transformed. No more lags in information. No more scrambling for data. IT/OT convergence in manufacturing is the key that unlocks a new level of efficiency, giving you a powerful edge.
As per a trusted source, the global IT/OT convergence market was valued at USD 51.9 billion in 2023. Over the forecast period of 2024–2030, the market is projected to grow at a CAGR of 14.5%.
But why are companies investing in this manufacturing technology trend? In other words, what are the IT/OT convergence benefits that you can enjoy for your manufacturing unit? Let’s discover!
1. X-ray Vision for Production
Traditionally, production data has been siloed, making it hard to identify bottlenecks. IT/OT convergence connects machines and sensors to IT systems, providing a real-time, holistic view of your entire operation. It’s like having X-ray vision, allowing you to pinpoint inefficiencies and optimize production schedules for maximum output.
2. Predict, Don’t Panic with Predictive Maintenance
Imagine knowing when a machine is about to fail before it actually does. IT/OT convergence lets you analyze sensor data to predict equipment issues. This allows proactive maintenance, preventing costly downtime and ensuring smooth production runs.
3. Quality from Start to Finish
Quality control becomes a continuous process. By integrating quality data with production information, you can identify potential issues early on in the process. This reduces waste, ensures consistent product quality, and boosts customer satisfaction.
4. Agility at Your Fingertips
The market moves fast. With IT/OT convergence in manufacturing, you can react faster to changing customer demands or new trends. Real-time data allows you to adjust production schedules quickly and efficiently, keeping you ahead of the curve.
5. Data-Driven Decisions, Every Time
Stop relying on gut instinct. IT/OT convergence in manufacturing equips you with a wealth of data to make informed decisions. From resource allocation to optimizing workflows, every choice will be backed by valuable insights, leading to smarter, more profitable operations.
6. Collaboration Powerhouse
Break down departmental barriers. IT/OT convergence fosters seamless communication between production, engineering, and quality control teams. Everyone has access to the same real-time data, enabling better collaboration and faster problem-solving across the entire organization.
IT/OT convergence in manufacturing isn’t just a buzzword; it’s the key to unlocking the true potential of your factory. By connecting information with operations, you’ll create a smarter, more efficient, and ultimately more successful manufacturing environment.
Build a Smart Factory with IT/OT Convergence in Manufacturing!
How Can IT/OT Convergence in Manufacturing Help You Establish a Smart Factory?
The benefits of IT/OT convergence are clear, but how does it translate into building a smart factory that overcomes the everyday challenges faced by manufacturers? Let’s dive into some common hurdles and see how IT/OT convergence acts as the solution:
Challenge 1: Limited Visibility into Production Processes
Imagine running a factory blindfolded. That’s what limited visibility feels like. Traditionally, data on production is scattered across different systems, making it difficult for decision-makers to get a comprehensive view of the entire operation. This lack of visibility can lead to inefficiencies, as managers cannot easily identify bottlenecks or areas for improvement. Without real-time data, predicting and preventing issues becomes nearly impossible, leading to delays and increased operational costs.
Solution: IT/OT convergence in manufacturing acts like a high-tech control center. By connecting machines and sensors to IT systems, it provides a real-time, centralized view of your entire operation. You can see machine performance data, track production progress in real-time, and identify bottlenecks that are hindering efficiency. This allows for data-driven adjustments to optimize production flow and maximize output.
Challenge 2: Unplanned Downtime and Reactive Maintenance
Unexpected equipment failures can cripple production schedules and lead to significant financial losses. Traditionally, maintenance practices have been reactive, addressing issues only after they occur. This approach not only leads to unplanned downtime but also shortens the lifespan of equipment due to inadequate care.
Solution: IT/OT convergence in manufacturing acts like a predictive maintenance tool. By analyzing sensor data, the system can identify early warning signs of potential equipment issues before they occur. This allows for preventive maintenance scheduling, minimizing downtime, saving costs on repairs, and ensuring smooth production runs. Imagine catching a small tear in your clothes before they become a gaping hole – that’s the power of predictive maintenance.
Challenge 3: Inconsistent Product Quality
Maintaining consistent product quality is a perennial challenge in manufacturing. Variations in raw materials, machine performance, and human error can lead to quality issues, resulting in customer dissatisfaction and increased costs due to rework and scrap. Traditional systems often lack the capability to provide real-time feedback on production quality, making it difficult to address issues promptly.
Solution: IT/OT convergence acts like a real-time quality inspector. By integrating quality control data with production information, you can monitor product quality throughout the manufacturing process. The system can even trigger alerts for any potential deviations from specifications, allowing for immediate corrective actions to ensure consistent quality from start to finish.
Challenge 4: Difficulty Adapting to Changing Market Demands
The market is dynamic, and manufacturers need to be agile. However, siloed data makes it difficult to react quickly to changing trends or customer demands. Traditional manufacturing systems often lack the flexibility to adjust production schedules or processes on short notice. This rigidity can result in missed opportunities and an inability to meet customer expectations.
Solution: IT/OT convergence in manufacturing acts like a market intelligence dashboard. It gives you real-time data on production capabilities, inventory levels, and customer demands. This allows for more flexible production scheduling. Imagine being able to quickly adjust production lines to meet a sudden surge in demand for a specific product – that’s the agility IT/OT convergence provides.
Challenge 5: Data Silos and Communication Gaps
Information silos create communication barriers between departments, hindering collaboration and decision-making. When IT and OT systems operate independently, valuable data remains isolated, preventing a holistic view of operations. This fragmentation can lead to inefficiencies, as teams may duplicate efforts or miss critical insights.
Solution: IT/OT convergence acts like a universal translator, breaking down data silos and communication gaps. Everyone in the organization – production, engineering, and quality control – has access to the same real-time data. This fosters seamless collaboration, allowing teams to work together more effectively, identify problems faster, and develop solutions collaboratively.
Challenge 6: Lack of Skilled Workforce
The modern manufacturing environment requires a workforce with skills in data analysis and IT alongside traditional manufacturing expertise. Finding and retaining these skilled workers can be a challenge. As manufacturing becomes more digitalized, the demand for employees who can operate and maintain advanced technologies increases. However, there is often a gap between the skills available in the workforce and those required by modern manufacturing processes.
Solution: IT/OT convergence, while requiring some workforce upskilling, can streamline processes and reduce the need for certain manual tasks. Additionally, the data-driven insights provided by IT/OT convergence can empower even less experienced workers to make informed decisions and contribute to the optimization process.
By addressing these common manufacturing challenges, IT/OT convergence paves the way for building a truly smart factory – one that is efficient, adaptable, data-driven, and secure. You can connect with us to learn more about how this manufacturing technology trend can benefit your organization!
Seeking to Resolve Your Manufacturing Challenges Using IT/OT Convergence?
How to Implement IT/OT Convergence in Manufacturing?
Now that you understand the power of IT/OT convergence in manufacturing, you might be wondering: “How do I actually implement it in my own factory?” Here’s a roadmap to guide you through the process. This comprehensive guide breaks down each step, addressing potential concerns and providing clear actions to ensure a smooth transition towards your smart factory.
Understanding Your Business Requirements and the IT/OT Landscape
What to Identify: This is an audit of your existing technological infrastructure. On the IT side, this includes your Enterprise Resource Planning (ERP) software, data management systems, and specific applications used for production planning or inventory control. In short, you must analyze the custom manufacturing solutions that are used in your company.
For OT, you’ll want to catalog Programmable Logic Controllers (PLCs) that manage your robots, sensors that track machine performance, and Human-Machine Interfaces (HMI) used for operator control.
Feeling overwhelmed? Unsure where to find information? The best way to streamline this step is to connect with a consultancy and opt for business and technology consulting services.
Goal Setting – Defining Your IT/OT Convergence Roadmap
Once the requirements are clear, the next step to implement IT/OT convergence in manufacturing is to define a clear roadmap or IT/OT strategy.
Clearly define the specific challenges you want IT/OT convergence to address.
Ask yourself questions like:
- Are you aiming to improve production visibility by tracking machine performance data in real-time?
- Do you want to optimize resource allocation by analyzing data on raw material usage and equipment availability?
- Maybe you’re looking to achieve predictive maintenance by leveraging sensor data to anticipate equipment failures before they occur.
Having clear goals will guide your convergence strategy and help you prioritize resources.
Feeling unsure about the right goals? Look at your current production bottlenecks or areas with the highest costs. These are prime targets for IT/OT convergence in manufacturing initiatives.
Need help identifying goals? Consult with your production floor managers and data analysts. They can provide valuable insights into areas where data-driven decision making can have the most significant impact.
Building Your Bridge – Developing an IT/OT Convergence Strategy
This is where you outline the specific plan for connecting your IT and OT systems. Think about these key areas:
- Data Integration: How will you collect and transfer data from OT systems (sensors, machines) to your IT infrastructure (databases, applications)? This might involve implementing industrial gateways that act as translators between different systems or utilizing edge computing solutions for processing data closer to its source.
- Data Standardization: Data from various sources may not speak the same “language.” You’ll need a plan to ensure data from different devices and systems is standardized for seamless analysis. This could involve adopting common communication protocols or data formats like OPC UA.
- Security Measures: With IT and OT systems connected, you’re creating a larger attack surface for cyber threats. Develop a robust cybersecurity strategy that includes network segmentation (separating IT and OT networks), firewalls for added protection, and regular software updates to patch vulnerabilities.
If you feel overwhelmed by technical details, partner with a digital transformation services provider experienced in manufacturing software development and familiar with IT/OT convergence best practices. Your chosen technology partner can recommend the right hardware, software, and implementation strategies for your specific needs.
Finding Your Partner – Choosing the Right Technology Partners
Partnering with an experienced custom manufacturing software development company can be a valuable asset to your IT/OT convergence journey. Lok for a trusted company with the following qualifications:
- Manufacturing Expertise: They should understand the unique challenges and opportunities within the manufacturing industry.
- IT/OT Convergence Experience: They should have a proven track record of implementing successful IT/OT convergence projects.
- Technology Knowledge: They should be familiar with the latest hardware, software, and best practices in IT/OT convergence.
- Project Management Skills: They should possess the skills to manage the project efficiently and keep it on track.
Testing the Waters – Pilot Project and Refinement
Don’t attempt to overhaul everything at once. Invest in MVP development services to start with a pilot project in a specific area, like a single production line or a particular type of equipment. This allows you to:
- Test the technology: See how well the chosen hardware and software integrate with your existing systems and how effectively they collect and analyze data.
- Identify challenges: No project is perfect, and pilot projects are a great way to identify any unforeseen hurdles you can address before a full-scale rollout.
- Refine your approach: The insights gained from the pilot can be used to refine your overall.
IT/OT Convergence Challenges and How to Tackle Them Effectively
The path to a smart factory paved with IT/OT convergence in manufacturing isn’t without its hurdles. Here are some common IT/OT convergence challenges manufacturers face and how, with the right approach, you can turn them into stepping stones for success:
Challenge 1: Cybersecurity Concerns
With IT and OT converging, your attack surface becomes larger. This can feel like opening the gates to a digital fortress, leaving your critical manufacturing operations vulnerable to cyber threats.
Tackling It: Implement a robust cybersecurity strategy with network segmentation (separating IT and OT networks) and firewalls. Regularly update software and firmware on all connected devices. Matellio prioritizes security. Our solutions are built with secure coding practices and regular penetration testing to ensure the integrity of your data and operations.
Challenge 2: Lack of Skilled Workforce
IT/OT convergence requires a workforce with expertise in data analysis and IT alongside traditional manufacturing knowledge. Finding and retaining these skilled workers can be a challenge.
Tackling It: Upskill your existing workforce by providing training programs on data analysis, IT fundamentals, and cybersecurity awareness. Matellio offers comprehensive training and support to help your team understand and utilize the new system effectively. Our intuitive user interface minimizes the need for extensive technical knowledge, allowing your team to focus on leveraging data insights for better decision-making.
Challenge 3: Project Complexity and Management
IT/OT convergence projects can be complex, requiring careful planning, execution, and ongoing maintenance.
Tackling It: Partner with an experienced IT solution provider like Matellio. We have a proven track record of successfully implementing IT/OT convergence projects in manufacturing environments. Our team of experts will manage the entire process, from initial planning and technology selection to implementation, training, and ongoing support.
Challenge 4: Return on Investment (ROI) Justification
Demonstrating the return on investment (ROI) for IT/OT convergence projects can be challenging for some manufacturers.
Tackling It: Focus on quantifiable benefits like increased production efficiency, reduced downtime, improved product quality, and lower maintenance costs. Utilize pilot projects to showcase the tangible impact of IT/OT convergence on specific areas of your operation. Matellio can help you build a business case that highlights the projected ROI of your IT/OT convergence initiative, considering both cost savings and revenue generation opportunities.
By proactively addressing these challenges and leveraging the expertise of a solution provider like Matellio, you can navigate the IT/OT convergence in the manufacturing journey with confidence. Our comprehensive solutions and proven methodologies empower you to unlock the full potential of your data and transform your manufacturing operation into a smarter, more efficient, and competitive entity.
Why Choose Matellio to Implement IT/OT Convergence in Manufacturing?
The journey to a smart factory paved with IT/OT convergence is exciting, but it requires a reliable technology consulting services partner with the expertise and resources to guide you every step of the way. Here’s why Matellio stands out as the ideal choice for your manufacturing IT/OT convergence needs:
Deep Manufacturing Industry Knowledge
We understand the unique challenges and opportunities that manufacturers face. Our team has extensive experience working with companies across various manufacturing sectors, allowing us to tailor our solutions to your specific needs.
Also Read: Deep Learning in Manufacturing: Transforming Your Business
Proven Track Record of Success
Matellio has a proven track record of successfully delivering complex business solutions and digital transformation services to manufacturing companies worldwide. Our case studies showcase the tangible results we’ve delivered for our clients.
Comprehensive IT/OT Convergence Solutions
We offer a full suite of IT/OT convergence solutions, including:
- Integration Platform: Our platform seamlessly connects your IT and OT systems, ensuring smooth data flow and eliminating data silos.
- Data Management and Analytics: We provide tools to collect, analyze, and visualize your manufacturing data, empowering you to make data-driven decisions.
- Secure Data Encryption: Matellio prioritizes data security with at-rest and in-transit encryption, ensuring your sensitive manufacturing data remains protected even in the event of a breach.
Focus on User Experience
Our solutions are designed with user-friendly interfaces, minimizing the need for extensive technical knowledge. This allows your team to focus on leveraging data insights for better decision-making, not wrestling with complex technology.
Training and Support
We don’t leave you hanging after implementation. Matellio offers comprehensive training programs and ongoing support to ensure your team can effectively utilize the new system and maximize its potential.
Focus on ROI
We understand the importance of demonstrating value. We’ll work with you to build a business case that highlights the projected ROI of your IT/OT convergence initiative, considering both cost savings and revenue generation opportunities.
By partnering with Matellio, you gain more than just a technology provider – you gain a trusted advisor with the expertise and commitment to help you achieve your smart factory goals.
Also Read: How to Build IoT-based Smart Factory Management Solutions?
Ready to unlock the power of IT/OT convergence in your manufacturing operation?
Conclusion
The path to a smart factory is paved with data-driven insights and interconnected systems. While IT/OT convergence in manufacturing presents challenges, it also unlocks a treasure trove of opportunities for manufacturers. By overcoming these IT/OT convergence challenges and strategically implementing IT/OT convergence in manufacturing, you can:
- Boost Efficiency and Productivity: Real-time data from your machines allows for optimized production scheduling, preventive maintenance, and minimized downtime.
- Enhance Product Quality: Continuous monitoring of production processes helps identify and address quality issues before they impact your end product.
- Reduce Costs: Data-driven insights can help optimize resource allocation, minimize waste, and lower overall manufacturing costs.
- Gain a Competitive Edge: IT/OT convergence empowers you to make faster, more informed decisions, giving you a significant edge in today’s competitive landscape.
Matellio is your trusted partner on the journey to a smarter factory. We offer the expertise, technology, and ongoing support you need to navigate IT/OT convergence successfully. Let’s work together to unlock the full potential of your data and transform your manufacturing operation into a future-proof powerhouse. Contact us today to schedule a free consultation to discuss your IT/OT convergence goals!
FAQ’s
Q1. What is an example of IT and OT convergence?
An example of IT and OT convergence is the integration of enterprise resource planning (ERP) systems with manufacturing execution systems (MES). This integration allows real-time data from the shop floor to be seamlessly shared with the business systems, enhancing decision-making and improving operational efficiency.
Q2. How much will it cost me to implement IT/OT convergence in manufacturing?
The cost of implementing IT/OT convergence in manufacturing varies widely based on the scale of the project, existing infrastructure, and specific requirements. It's best to consult with a professional service provider like Matellio for a detailed quote tailored to your needs.
Q3. How can I connect with Matellio for IT/OT convergence implementation?
Here's a simple process you need to follow for connecting with us:
- Fill out our form
- Discuss your requirements with our experts over a free 30-minute call
- Get custom quote and project scope from our business analysts
- Choose a flexible engagement model and sign the legal agreements
- Get started with your project
Q4. What other services do you offer?
- Cloud integration services
- Custom enterprise software development
- Industry-focused engineering services
- Enterprise mobility solutions
- DevOps and Testing
- UI/UX and Proof-of-Concept
- SaaS services
- Technology consulting services
- Digital transformation consulting
- Data consultation services