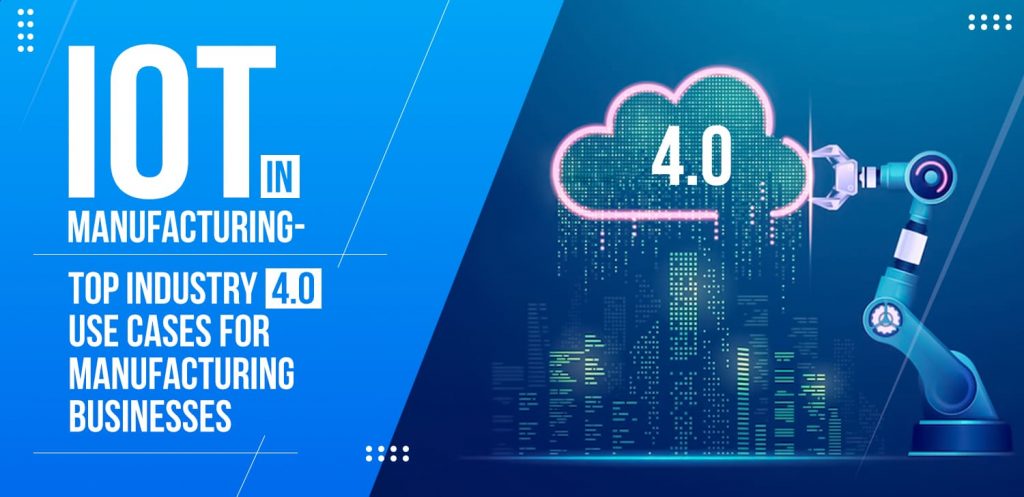
IoT implementation has been changing the face of industries. Business-centric IoT app is helping businesses drive value in core processes and reimagine how they serve the customers. As one of the early adopters of IoT, the manufacturing industry is leading the front with Industry 4.0.
The fourth industrial revolution, also known as Industry 4.0 and smart manufacturing, is completely altering the production lines for the better. From machines being able to communicate with each other to automation that boosts productivity, industry 4.0 has enabled manufacturing businesses to smarten their processes. It is no wonder that the industry 4.0 market is expected to reach 267.01 billion by 2026, growing at a CAGR of 20.71% from 2021 to 2026.
The need for manufacturing brands to become resilient in the post-pandemic era is further attributed to the adoption of industry 4.0. Let’s catch up on how industrial 4.0 is beginning an all-new generation of manufacturing.
What is Industry 4.0?
Industry 4.0 or industrial revolution 4 is a globally adopted term to smarten the manufacturing process and capitalize on automation to build smart factories. It offers a notion of the manufacturing process with a smooth paradigm shift from a central industrial control system to a process where smart products define the next step.
Manufacturers operating on the industry 4.0 model leverage an autonomous decision-making model, asset tracking, and real-time process monitoring to create value focused on the personalization of the products.
Industrial 4.0 Use Cases for Manufacturing Industry
Increased Efficiency
Every manufacturing business is exploring ways to maximize efficiency. IoT brings them the right set of tools and technologies to reach this goal. IoT-based software solutions allow companies to capitalize on data-driven insights and create actionable insights that boost productivity. Here’s how:
Predictive Maintenance
- Unplanned downtime costs $50 billion annually to industrial manufacturers.
- Aging equipment is the leading cause of unplanned downtimes.
- The average cost per hour of equipment downtime is $260,000.
These statistics are clear indicators of why 80% of the manufacturers consider predictive maintenance part of a multi-faceted maintenance strategy.
Predictive maintenance aims at proactive maintenance planning to avoid unexpected equipment downtimes. IoT devices like sensors are installed with the machines to analyze the conditions constantly. They also check the determinants to identify potential malfunctions and send an alert to the authorized personnel. Once the data is collected, it is analyzed on various KPIs to generate reports. Having the maintenance schedule beforehand allows managers to plan resources for the task and shift the load accordingly.
The comprehensive predictive maintenance system benefits the overall production in multiple ways:
Improved Worker Safety and Compliance
Manufacturing employees are susceptible to a wide range of hazards that can be life-threatening. This has forced businesses to deploy IoT solutions to ensure worker safety and compliance at the workplace. While one of the facets of this application has been discussed above, that’s not it.
Quality Control
Quality assurance is an important aspect of the manufacturing process. A small defect in the raw material or inaccurate measurement can lead to big problems. For instance, if the amount of certain raw material exceeds or precedes the required quality in the pharmaceutical industry, it can lead to loss of life. This not just creates a big legal issue for the business but also accounts for life-threatening outcomes.
When the processes are manual, such issues are bound to creep in at one point or another. The carelessness of production staff or manual problems such as tiredness, boredom, and drowsiness can impact the quality of deliverables and hence, the production outcomes.
IoT solves this issue for manufacturing businesses. IoT and AI combinations allow for high-quality inspection at every stage of development. It eliminates the manual process to minimize risk to the quality and decrease the instances of scrap or defect rejects. Defect identification with IoT is also quicker, thus ensuring a faster turnaround.
Asset Tracking
Asset tracking and management have been a critical part of the manufacturing businesses. Traditional systems leveraged satellite and cellular technology to track assets. While the technologies delivered fairly good results, they were technically incompetent, expensive, and did not optimize asset monitoring.
The problems with traditional asset tracking systems encouraged businesses to opt for IoT-powered solutions. Here is how various parts of the manufacturing industry benefit from IoT-based asset tracking:
Read More: How can IoT Improve the Retail Industry?
a. Supply Chain and Logistics
Sometimes, it is required for businesses to track high-value assets on the move. Tracking them in real-time gives managers and business owners peace of mind and makes delivery more efficient. RPA in manufacturing and IoT systems enable businesses to gain visibility of the supply chain, allowing them to know the exact location of the asset, the status of delivery, the condition of an asset, and more.
b. Facility Monitoring
Smart surveillance systems allow managers to know about asset conditions on the floor and make informed decisions. Cameras and sensors are installed within the facilities to track any illegal activity like theft. Once these problems are detected, managers are alerted by the system to take timely action. Similarly, in case of misplacement, the assets can be located to avoid any problems.
c. Inventory and Warehouse Management
Is Your Manufacturing Business Ready for the Wave of Industrial 4.0?
Industrial automation has been making it to the headlines for now. It is the preferred way for manufacturing businesses to foster evolution, development, and advancement in their factories. While enhancing the processes at their core, IoT-powered systems also allow them to perform product testing, inspection, assembling, heavy-lifting, and more. These factors are expected to continue to bolster the industry’s adoption in the upcoming years.
We at Matellio offer the right technology solutions to the manufacturing businesses on their way to digitalization. Our specialized IoT teams combined with excellent mobile, web, and custom ERP developers help you identify the gaps in your processes and address them with the right digital products. Our state-of-the-art product design and development lab is well equipped to create experiences that enable you to optimize the manufacturing processes and harness long-term value from your investment in IoT-based manufacturing solutions.
We pride ourselves on our IoT development services and capabilities, that include:
- Infrastructural competence to create cutting-edge IoT hardware and software products
- Experience in building IoT products for diverse industry verticals
- Certification in the futuristic technology stack
- Secure data management policies
- Support for management of legacy and advanced devices
- High performing analytics and data collection
Let us know your goals with IoT implementation, and we’ll build the right IoT team for you to achieve them. Share your requirements right away.