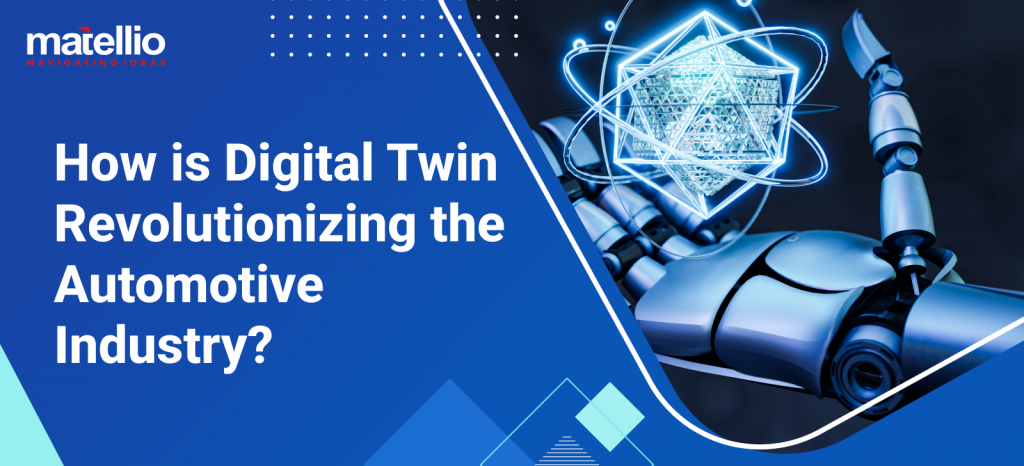
The automotive industry is on the cusp of a digital revolution, and at the heart of this transformation lies the concept of digital twins. This cutting-edge technology is poised to redefine how vehicles are designed, manufactured, and maintained, ushering in a new era of innovation and efficiency.
Digital twins, virtual replicas of physical objects or systems, are revolutionizing the way vehicles are designed, manufactured, and maintained. In the automotive industry, digital twin enhance product development, optimize manufacturing processes, and improve vehicle performance and safety.
In this blog post, we’ll delve into the fascinating world of digital twin in automotive. We’ll explore how this technology works, its benefits to manufacturers and drivers alike, and it’s exciting possibilities for the automotive industry. So, let’s get started!
What is Digital Twin in the Automotive Industry?
A digital twin is a virtual representation of a physical object or system. This virtual model mirrors the physical entity in real time, providing a means to monitor, analyze, and optimize its performance.
The concept of digital twin originated in aerospace, where it was used to replicate and simulate the behavior of aircraft components. However, its application has since expanded to a wide range of industries, including manufacturing, automotive, and urban planning. The key idea behind digital twin technology in automotive industry is to create a dynamic, real-time model that enables users to gain insights, predict outcomes, and make informed decisions.
One of the primary benefits of digital twin technology in automotive industry is their ability to facilitate predictive maintenance by continuously monitoring the performance of a physical asset, such as a vehicle; a digital twin can predict when maintenance is required, thus minimizing downtime and reducing maintenance costs. This predictive capability can significantly impact industries where downtime can result in substantial losses, such as automotive or transportation.
Another crucial aspect of digital twin technology in automotive industry is their role in enabling remote monitoring and control. In scenarios where physical access to assets is limited or hazardous, digital twin provide a means to monitor and manage these assets from a safe distance.
Furthermore, digital twin technology in the automotive industry is revolutionizing the way products are designed and developed. By creating a digital twin early in the design process, engineers can simulate and test various scenarios, optimizing the product’s performance and reducing the time to market. This approach, known as “digital prototyping,” has the potential to drive innovation and improve product quality.
Looking to Leverage Next-Gen Technologies Services from a Trusted Provider?
Digital Twin in Automotive Market Size
Benefits of Digital Twin in the Automotive Industry
A digital twin is a virtual representation of a physical product or process, which enables real-time monitoring, predictive maintenance, performance optimization, and much more. Let’s explore the various benefits and digital twin automotive use cases:
Virtual Representation
Digital twin visually represent physical vehicles, components, and manufacturing processes. This virtual model enables automotive companies to visualize and analyze their products and processes in a digital environment, facilitating better decision-making and problem-solving.
Real-Time Monitoring
With digital twins, automotive companies can monitor the performance of their vehicles and production processes in real time. This real-time monitoring enables companies to identify and address issues proactively, minimizing downtime and improving overall efficiency.
Predictive Maintenance
Digital twin enable predictive maintenance by analyzing data from sensors and other sources to predict when maintenance is required. This predictive maintenance approach helps automotive companies avoid unexpected breakdowns and reduce maintenance costs.
Performance Optimization
Digital twin allow automotive companies to optimize the performance of their vehicles and production processes. By analyzing data from digital twins, companies can identify areas for improvement and implement changes to enhance performance.
Simulation and Testing
Digital twin enable automotive companies to simulate and test new vehicle designs and manufacturing processes in a virtual environment. This simulation and testing capability helps companies identify potential issues early in development, reducing the time and costs associated with physical testing.
Supply Chain Optimization
Digital twin enable automotive companies to optimize their supply chains by providing real-time visibility into inventory levels, production schedules, and supplier performance. This optimization helps companies reduce costs and improve efficiency.
Also Read- IoT in Supply Chain: Use Cases and Implementation Strategy
Safety and Security
Digital twin enhance safety and security by enabling companies to identify potential safety hazards and security vulnerabilities in their vehicles and production processes. This proactive approach to safety and security helps companies mitigate risks and ensure compliance with regulations.
Customization and Personalization
Digital twin enable automotive companies to customize and personalize their vehicles to meet customer needs and preferences. This customization and personalization capability help companies differentiate their products in the market and enhance customer satisfaction.
Lifecycle Management
Digital twin enable automotive companies to manage the entire lifecycle of their vehicles, from design and manufacturing to operation and maintenance. This lifecycle management capability helps companies optimize costs and improve product quality.
Remote Diagnostics and Troubleshooting
Digital twin enable automotive companies to diagnose and troubleshoot issues remotely. These remote diagnostics and troubleshooting capability help companies resolve problems quickly and efficiently, reducing downtime and improving customer satisfaction.
Digital twin in the automotive market are revolutionizing the automotive industry by providing enterprise solutions for virtual representations of physical products and processes. The benefits of digital twins, including virtual representation, real-time monitoring, predictive maintenance, performance optimization, and many others, enable automotive companies to innovate faster, reduce costs, and improve customer satisfaction.
Applications of Digital Twin in the Automotive Industry
In the automotive industry, digital twin are transforming the way vehicles are designed, manufactured, and maintained. Let’s explore the applications of digital twin in automotive market:
Manufacturing Assembly Line
Digital twin can be used to simulate and optimize the manufacturing assembly line, improving efficiency and reducing downtime. Manufacturers can use digital twin to identify potential bottlenecks, optimize production schedules, and test new production methods before implementation.
Plant/Machine Maintenance and Repairs
Digital twin can help monitor the condition of plant machinery and equipment in real time. By analyzing data from sensors embedded in the machinery, manufacturers can predict when maintenance is required, reducing the risk of unplanned downtime and costly repairs.
Quality & Safety Assurance
Digital twin can simulate and analyze the quality and safety of automotive components and systems. Manufacturers can use digital twin to identify potential defects or safety hazards early in the design process, ensuring that vehicles meet the highest quality and safety standards.
Supply Chain and Logistics
Digital twin can optimize supply chain and logistics operations by simulating and analyzing the movement of parts and components throughout the supply chain. Manufacturers can use digital twin to identify inefficiencies, optimize inventory levels, and improve delivery times.
Training and Simulation
Digital twin can train employees and simulate real-world scenarios in a safe and controlled environment. For example, automotive manufacturers can use digital twin to train assembly line workers on new production methods or simulate emergency scenarios for maintenance and repair technicians.
Digital transformation services are revolutionizing the automotive industry by providing manufacturers with powerful tools to optimize production processes, improve quality and safety, and enhance supply chain and logistics operations. As technology continues to evolve, the applications of digital twin in the automotive industry are only expected to grow, driving innovation and efficiency across the industry.
Get a Free Expert Consultation with Our Digital Twin Experts for Your Business.
Technologies Used in Digital Twin for the Automotive Industry
Digital twins, virtual replicas of physical assets, processes, or systems, have revolutionized the way automotive companies design, manufacture, and maintain vehicles. Let’s delve into the trending technologies that are shaping the future of digital twin in the automotive industry:
Internet of Things Sensors
IoT in automotive play a crucial role in digital twining by collecting real-time data from vehicles and their components. These sensors monitor various parameters such as temperature, pressure, speed, and location, providing valuable insights into the performance and condition of vehicles.
Big Data Analytics
IoT in automotive industry is revolutionizing the way data is utilized. Big data analytics is essential for processing and analyzing the vast amount of data collected by IoT sensors. By leveraging advanced analytics techniques, automotive companies can gain valuable insights into vehicle performance, customer behavior, and market trends, enabling them to make informed decisions.
Also Read- Big Data Analytics: Unlocking Industry-Specific Solutions for Transformative Business Insights
Artificial Intelligence and Machine Learning
AI and ML algorithms analyze data collected from digital twins and identify patterns, trends, and anomalies. These technologies enable automotive companies to predict maintenance issues, optimize vehicle performance, and enhance customer experience.
Augmented Reality and Virtual Reality
AR and VR technologies are used to visualize and interact with digital twins in a virtual environment. Automotive companies can use these technologies for design reviews, training simulations, and remote maintenance, improving efficiency and reducing costs.
Blockchain Technology
Blockchain technology can enhance the security and transparency of data exchanged between digital twin and other systems. It can also facilitate secure transactions, such as vehicle sales and leasing while ensuring data integrity and authenticity.
Cloud Computing
Cloud computing enables automotive companies to store and access digital twin data securely and cost-effectively. It also provides scalability and flexibility, allowing companies to deploy digital twin globally and integrate them with other systems seamlessly.
3D Printing
3D printing technology is used to create physical prototypes based on digital twin models, enabling faster and more cost-effective prototyping and product development processes.
The automotive industry is undergoing a digital transformation driven by the adoption of digital twin technology. By leveraging technology consulting services, automotive companies can enhance vehicle design, manufacturing, and maintenance processes, leading to improved efficiency, cost savings, and customer satisfaction.
Challenges Overcome by Digital Twin in Automotive Industry
Let’s explore the challenges faced by the automotive industry and how digital twin are addressing them:
Complexity of Vehicle Systems
- Challenge: Modern vehicles are equipped with many complex systems, including engines, transmissions, brakes, and electronic components. Managing and optimizing these systems requires a comprehensive understanding of their interactions and performance.
- Solution: Digital twins enable virtual prototyping and testing of vehicles and components, allowing manufacturers to simulate real-world conditions and scenarios. This helps identify potential issues early in the development process, reducing costs and reducing time to market.
Cost and Time Constraints
- Challenge: Developing new vehicles or components is a costly and time-consuming process. Traditional prototyping and testing methods can be inefficient and may lead to delays in product development.
- Solution: Digital twins can simulate and optimize manufacturing processes, leading to improved efficiency and cost savings. Manufacturers can identify bottlenecks and inefficiencies in the production line and make necessary adjustments to improve overall productivity.
Quality Control
- Challenge: Ensuring the quality and reliability of vehicles is crucial for customer satisfaction and brand reputation. However, identifying and resolving quality issues can be challenging, especially in complex systems.
- Solution: By providing a complete view of vehicle systems and performance, digital twin help ensure the quality and reliability of vehicles. Manufacturers can identify and address quality issues early in the development process, minimizing the risk of recalls and warranty claims.
Maintenance and Service
- Challenge: Efficient maintenance and service are essential for vehicle longevity and customer satisfaction. However, predicting maintenance needs and optimizing service schedules can only be possible with real-time data and insights.
- Solution: Digital twins enable manufacturers to gather real-time data on vehicle performance and usage, allowing them to offer personalized services and recommendations to customers. This leads to improved customer satisfaction and loyalty.
Digital twins are revolutionizing the automotive industry by providing innovative solutions to its challenges. By enabling virtual prototyping, real-time monitoring, and predictive maintenance, a professional AI development company like Matellio helping manufacturers improve efficiency, reduce costs, and enhance product quality, ultimately transforming the way vehicles are designed, manufactured, and serviced.
Get a Budget Estimate for Your Next Big Project.
Conclusion
Digital twin represents a paradigm shift in interacting with and managing physical assets. Organizations can gain valuable insights, improve operational efficiency, and drive innovation by creating a digital replica of the physical world.
Digital twins are rapidly transforming the automotive industry, from design and manufacturing to post-sale maintenance and the overall driving experience. This technology offers a powerful glimpse into the future of mobility, one that is data-driven, efficient, and personalized.
While challenges exist, the potential benefits far outweigh them. As technology matures and integration with existing systems becomes smoother, digital twin promise to revolutionize every aspect of the automotive industry.
As technology continues to evolve, we can expect to see even greater integration of digital twins across industries, transforming the way we work, live, and interact with the world around us.
FAQs
What is a digital twin in the automotive industry?
A digital twin in the automotive industry is a virtual representation of a physical vehicle, system, or process. It uses real-time data and simulation to mimic the behavior and performance of its physical counterpart.
How is data privacy and security addressed in digital twin technology?
Data privacy and security are crucial considerations in digital twin technology. Manufacturers must implement robust security measures to protect sensitive data and ensure compliance with relevant regulations, such as GDPR.
How is digital twin technology expected to evolve in the future?
Digital twin technology is expected to become more sophisticated, with increased integration of AI and machine learning. This will enable even more advanced predictive capabilities and further enhance the overall impact on the automotive industry.
How does digital twin technology improve product design?
Digital twins enable automakers to simulate and test vehicle designs in a virtual environment before physical prototypes are built. This helps identify potential issues early in the design process, reducing development time and costs.