
Have you ever wondered how your smartphone, car, or even your morning cup of coffee comes into being? Behind the scenes, a fascinating journey unfolds within the realm of manufacturing, where raw materials are transformed into the products we rely on daily. But have you ever stopped to ponder how this process is evolving in the digital age?
Questions naturally arise: What exactly is digital transformation in manufacturing? How does it reshape the way goods are produced, and what impact does it have on our lives?
Digital transformation in manufacturing is becoming more than just a buzzword—it’s a game-changer. It’s about infusing digital technologies like automation, AI, and IoT into every aspect of production, from design to delivery.
Why the surge in demand?
Businesses are under pressure to stay competitive by enhancing efficiency, reducing costs, and delivering products faster than ever before. Consumers, too, expect personalized products, seamless experiences, and sustainable practices from the brands they support.
As a result, manufacturers are embracing digital transformation as a strategic imperative rather than a mere trend. Those who adapt swiftly stand to gain a competitive edge in the global marketplace, while those who lag risk obsolescence.
But it’s not just about efficiency; it’s a gateway to innovation, sustainability, and fresh revenue streams. From predictive maintenance to mass customization, the possibilities are boundless.
Let’s explore the exciting frontier of digital transformation in industrial manufacturing —where tradition meets technology, and innovation knows no bounds.
What is Digital Transformation in Manufacturing Industry?
In simple terms, Digital transformation in the manufacturing industry is the use of digital tools to make everything in the manufacturing process better. It involves integrating advanced technologies like automation, data analytics, artificial intelligence (AI), and the Internet of Things (IoT) into traditional manufacturing practices.
The digital transformation in manufacturing aims to make factories smarter, more efficient, and responsive to customer needs. It revolutionizes how products are designed, produced, and delivered to the market. For example, automation streamlines repetitive tasks, AI analyzes vast amounts of data to make better decisions, and IoT devices enable real-time monitoring and control of machinery and processes.
Moreover, digital transformation extends beyond the factory floor. It affects how you manage your supply chain, serve your customers, and even how you structure your business. It helps you optimize operations, cut costs, and bring products to the market faster. Plus, it lets you offer more customized and personalized products, meeting the growing demand from customers for tailored solutions.
So, opt for digital transformation for your business today if you haven’t yet. With the right manufacturing software development company, you can unlock the full potential of digital transformation and stay ahead in today’s competitive landscape.
Benefits of Digital Transformation in Manufacturing
When you embrace digital transformation in manufacturing, you unlock a world of benefits tailored to your needs. Let’s go through some of them:
Enhanced Efficiency
With digital transformation, you streamline your manufacturing processes, making them faster and more efficient. Tasks that once took hours can now be completed in minutes, thanks to automation and smart technologies.
Cost Savings
By optimizing operations through digital tools, you cut unnecessary costs. Whether it’s reducing waste, minimizing downtime, or improving resource utilization, digital transformation helps your bottom line.
Improved Decision-Making
Embracing data analytics and AI empowers you to make better-informed decisions. Analyzing vast amounts of data provides valuable insights, guiding you towards smarter choices in production, logistics, and beyond.
Real-time Monitoring
Through the Internet of Things (IoT), you gain real-time visibility into your manufacturing processes. This means you can monitor machinery, track inventory, and respond to issues instantly, preventing potential disruptions.
Customization Opportunities
Digital transformation enables you to offer personalized products to meet the unique demands of your customers. This level of customization enhances customer satisfaction and sets you apart in the market.
Supply Chain Optimization
With digital tools, you can optimize your supply chain for maximum efficiency. This involves better forecasting, inventory management, and collaboration with suppliers, ensuring a seamless flow of materials.
Read More: Discover how Smart Manufacturing Inventory Systems optimize operations, reduce waste, and enhance efficiency in modern industrial environments.
Adaptability to Market Changes
In a rapidly changing market, digital transformation allows you to adapt quickly. Whether it’s changing consumer preferences or shifts in the industry, you can stay nimble and responsive.
Innovation and Competitiveness
Embracing digital technologies positions you as an innovator in the manufacturing landscape. Staying competitive in the market often requires not just keeping up but leading in technological advancements.
Sustainability
By optimizing processes and reducing waste, digital transformation contributes to sustainability. Meeting environmental standards and reducing your carbon footprint becomes more achievable.
Strategic Growth Opportunities
Digital transformation opens avenues for strategic growth. Leveraging the expertise of an AI development company can propel you into the future, ensuring you’re at the forefront of technological advancements in manufacturing.
By embracing digital transformation in manufacturing, you unlock a world of possibilities to revolutionize your operations, drive sustainable growth, and remain competitive in today’s dynamic business landscape.
The market for digital transformation in manufacturing is projected to be worth USD 367.60 billion in 2024 and increase at a compound annual growth rate (CAGR) of 19.40% to reach USD 876.10 billion by 2029.
Projections from Statista indicate that by 2026, global spending on digital transformation will amount to $3.4 trillion.
In 2022, the manufacturing sector is expected to experience a global digital transformation valued at US$ 491.09 billion. This market is expected to grow at a strong rate of 21.2% from 2023 to 2033, reaching US$ 595.2 billion in 2023 and US$ 4.07 trillion in 2033.
74% of businesses rank digital transformation as their top concern.
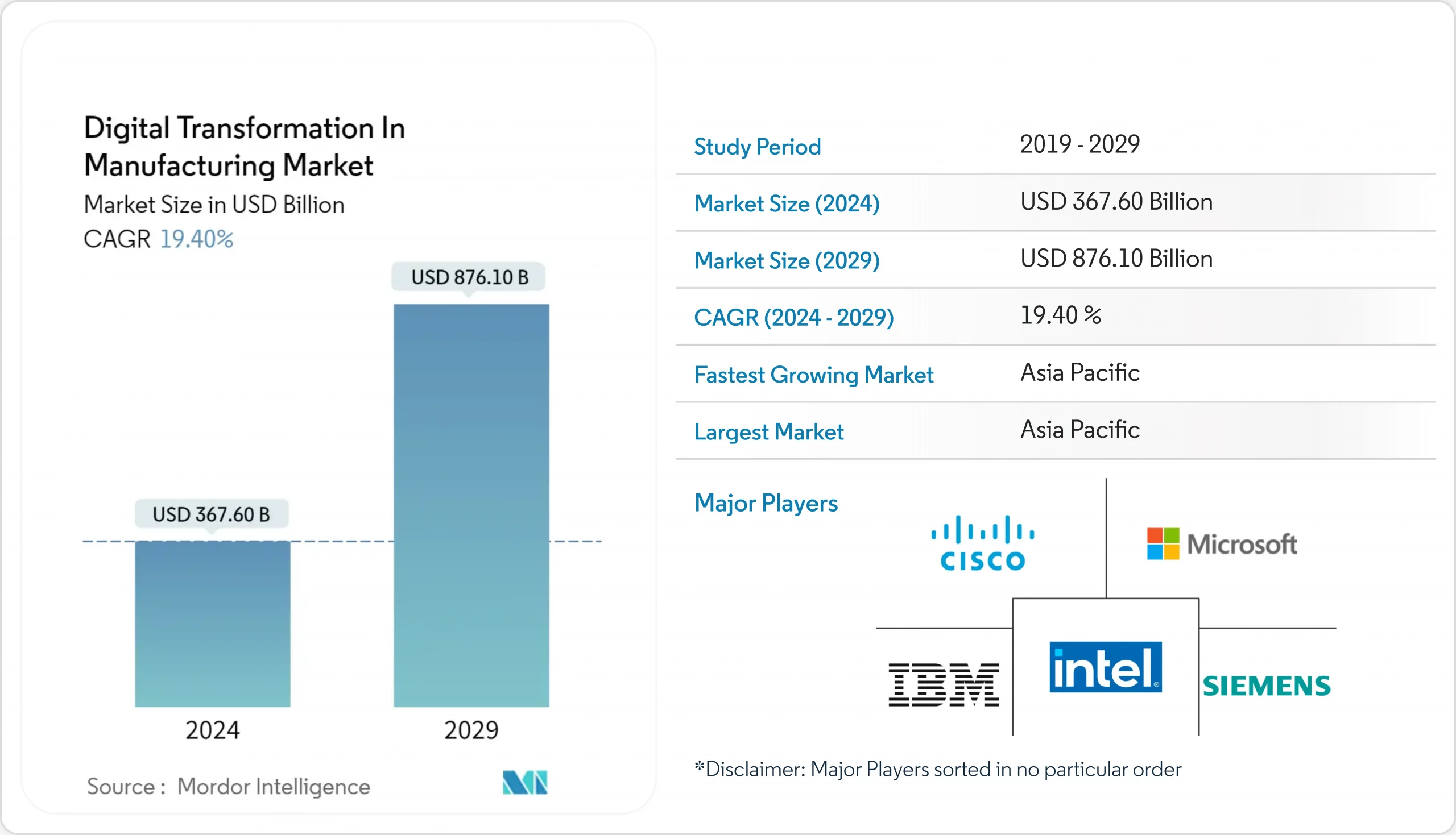
Top Digital Transformation Trends in Manufacturing
In the dynamic landscape of manufacturing, staying ahead means keeping pace with the latest digital transformation trends. Industry 4.0 has brought about a revolutionary shift, integrating cutting-edge technologies like IoT, AI, and automation into traditional manufacturing processes. Here are the top trends reshaping the manufacturing industry:
IoT Revolutionizes Operations
The Internet of Things (IoT) continues to transform manufacturing by enabling real-time monitoring, predictive maintenance, and data-driven decision-making. Collaborating with a company providing IoT development services, manufacturers can connect machines, sensors, and devices to optimize efficiency and drive innovation.
AI and Machine Learning for Predictive Insights
Artificial intelligence and machine learning algorithms empower manufacturers to unlock valuable insights from vast datasets. Predictive analytics enhance maintenance strategies, optimize production schedules, and improve quality control, leading to enhanced productivity and reduced downtime.
Digital Twins Drive Innovation
Digital twins, virtual replicas of physical assets or processes, revolutionize product design, simulation, and testing. By leveraging digital twins, manufacturers gain deeper insights into performance, identify potential issues early, and accelerate time-to-market for new products.
Augmented Reality (AR) Transforms Workflows
AR technologies are reshaping manufacturing workflows by providing interactive, hands-free guidance to workers. From assembly instructions to remote assistance, AR enhances productivity, reduces errors, and improves training processes.
Blockchain Enhances Supply Chain Transparency
Blockchain technology ensures transparency and traceability across the supply chain. By securely recording transactions and verifying product authenticity, blockchain reduces counterfeiting, enhances trust, and strengthens supplier relationships.
Cloud-Based Solutions Enable Agility
Cloud computing offers scalable, flexible solutions for managing data, applications, and resources. Cloud-based platforms facilitate collaboration, enable remote access to critical information, and support agile decision-making processes.
Cybersecurity Emerges as a Priority
As digitalization expands, cybersecurity becomes paramount. Protecting sensitive data, intellectual property, and operational systems is essential to safeguarding against cyber threats and ensuring business continuity.
Sustainable Manufacturing Practices
Digital transformation fosters sustainable manufacturing practices by optimizing resource utilization, reducing waste, and minimizing environmental impact. From energy-efficient processes to circular economy initiatives, sustainability is a driving force behind innovation.
Collaborative Robots (Cobots) Enhance Flexibility
Collaborative robots, or cobots, work alongside human workers to automate repetitive tasks and enhance production flexibility. With advanced sensors and safety features, cobots improve efficiency, adaptability, and worker safety.
Embracing these digital transformation trends, including RPA in manufacturing, empowers manufacturers to adapt, innovate, and thrive in an increasingly competitive global market. By harnessing the power of IoT, AI, RPA, and Industry 4.0 technologies, manufacturers can drive operational excellence, deliver superior products, and shape the future of manufacturing.
Also Read: Most Trending AI Use Cases in Manufacturing.
Digital Transformation in Industrial Manufacturing: Challenges and Solutions
While digital transformation in manufacturing brings numerous benefits, it also presents several challenges that you must take care of while implementing it to your business. Here are some of the key challenges along with potential solutions:
Challenge 1: Legacy System Integration
Many manufacturers grapple with integrating new digital technologies into existing legacy systems, leading to compatibility issues, data silos, and operational inefficiencies.
Solution: We can provide seamless integration solutions that bridge the gap between legacy systems and modern digital technologies. Our expertise ensures a smooth transition, preserving the functionality of existing systems while unlocking the benefits of digital transformation.
Challenge 2: Data Security Concerns
As digital transformation increases reliance on data, manufacturers face heightened concerns about data security, privacy breaches, and cyber threats.
Solution: Our company specializes in implementing robust cybersecurity measures tailored to the manufacturing sector. From encryption protocols to secure access controls, we prioritize the protection of sensitive data and safeguarding your digital infrastructure.
Challenge 3: Workforce Training and Adoption
Adopting new technologies requires a skilled workforce. Many manufacturers face challenges in training employees to use advanced digital tools effectively.
Solution: We offer comprehensive training programs designed to upskill your workforce and facilitate a smooth transition to digital processes. Our training modules focus on user-centric design, ensuring employees feel confident and competent in utilizing the latest technologies.
Challenge 4: Scalability
Manufacturers often encounter difficulties in scaling digital solutions to accommodate business growth or changing operational needs.
Solution: Our scalable digital transformation solutions are designed to grow with your business. Whether you’re expanding production capacities, entering new markets, or diversifying your product line, our solutions can adapt to meet your evolving requirements.
Challenge 5: Interconnected Ecosystems
Creating a fully connected manufacturing ecosystem involves coordinating various stakeholders, suppliers, and partners.
Solution: We specialize in building interconnected ecosystems that streamline communication and collaboration. Our solutions facilitate seamless information flow across the entire value chain, optimizing supply chain management and enhancing overall operational efficiency.
Challenge 6: Return on Investment (ROI) Measurement
Measuring the ROI of digital transformation initiatives can be challenging, and manufacturers often seek clear metrics to justify their investments.
Solution: Our analytics and reporting tools provide real-time insights into the performance and impact of digital transformation efforts. We help manufacturers quantify the tangible benefits, from cost savings to increased productivity, providing a transparent view of the ROI.
By addressing these challenges with tailored solutions, your company can position itself as a valuable partner for manufacturers navigating the complexities of digital transformation in the industry.
How to Implement Digital Transformation in Manufacturing
Implementing digital transformation in manufacturing requires a strategic and systematic approach that encompasses technology adoption, process optimization, organizational change, and cultural transformation. Here are the key steps to effectively implement digital transformation in manufacturing:
Define Clear Objectives and Goals
Begin by defining clear objectives and goals for digital transformation initiatives aligned with your organization’s strategic priorities. Identify specific areas of improvement, such as operational efficiency, product quality, supply chain visibility, or customer experience, and establish key performance indicators (KPIs) to measure progress and success.
Our experienced team will perform a thorough digital readiness assessment, identifying areas for improvement and developing a customized digital transformation roadmap aligned with your business objectives.
Develop a Digital Transformation Roadmap
Develop a detailed roadmap outlining the steps, milestones, and timelines for implementing digital transformation initiatives. Prioritize initiatives based on their potential impact, feasibility, and resource requirements, and sequence activities to minimize disruption to ongoing operations while maximizing value creation.
Invest in Technology and Infrastructure
Invest in the right mix of digital technologies, tools, and infrastructure to support your digital transformation goals. Leverage our expertise to recommend and implement cutting-edge technologies such as IoT, AI, and automation, tailored to enhance efficiency, productivity, and innovation.
Monitor Progress and Iterate
Monitor progress against key performance indicators (KPIs) and milestones outlined in your digital transformation roadmap. Establish mechanisms for continuous monitoring, feedback collection, and iterative refinement to drive ongoing improvement and innovation within your digital ecosystem. Leverage performance monitoring tools, analytics dashboards, and feedback loops to identify areas for optimization and address any challenges or bottlenecks that may arise.
Our solutions are built with scalability in mind, ensuring they can evolve alongside your business needs. We provide ongoing support to keep your digital infrastructure future-proof, monitoring performance and optimizing processes to drive sustainable growth and innovation in your manufacturing operations.
Also Read: How To Develop a Manufacturing Tracking Software?
By partnering with us throughout your digital transformation journey, you gain access to expertise, guidance, and solutions tailored to your unique needs. Together, we can navigate the complexities of digital transformation and unlock new opportunities for innovation, efficiency, and success in your manufacturing operations.
Case Study of Digital Transformation in Manufacturing
Throughout its history, Cisco has mainly relied on contract manufacturers for most of its manufacturing needs. While outsourcing offers various advantages, it also presents the hurdle of regulating outsourced production processes, particularly concerning product quality.
To address this challenge, Cisco pioneered a “virtual” MES (manufacturing execution system) platform known as VMES. This innovative platform furnishes real-time visibility into the quality of the supply chain.
VMES effectively disseminates supply chain quality data in real-time, encompassing three pivotal facets of outsourced production operations: Traceability, Transformation, and Test.
Why Choose Matellio for Digital Transformation in Manufacturing
Choosing Matellio for Digital Transformation Services is a strategic decision that ensures your business stays ahead in the rapidly evolving landscape of industry 4.0. With our comprehensive suite of services and expertise in digital transformation, we offer tailored solutions to address the unique challenges and opportunities facing your manufacturing operations.
At Matellio, we provide cutting-edge technologies and innovative solutions that empower you to optimize efficiency, streamline processes, and drive innovation across every aspect of your manufacturing operations. Our team of experts brings extensive experience and industry knowledge to the table, enabling us to understand your specific needs and deliver customized solutions that align with your business objectives.
Furthermore, our commitment to excellence and customer satisfaction sets us apart. We prioritize transparency, collaboration, and communication throughout the digital transformation journey, ensuring that you are involved and informed every step of the way.
With Matellio as your trusted partner, you can navigate the complexities of digital transformation with confidence, knowing that you have a dedicated team working tirelessly to help you achieve your goals. Together, we can unlock new opportunities, enhance competitiveness, and pave the way for sustainable growth in the digital age.
What are some examples of digital transformation initiatives in manufacturing?
Examples of digital transformation initiatives in manufacturing include predictive maintenance programs using IoT sensors and analytics, implementation of smart manufacturing technologies such as robotics and automation, adoption of digital twin technology for virtual modeling and simulation, integration of supply chain management systems with blockchain technology, and deployment of additive manufacturing solutions such as 3D printing for rapid prototyping and production.
How can manufacturers measure the success of digital transformation initiatives?
Manufacturers can measure the success of digital transformation initiatives by tracking key performance indicators (KPIs) such as operational efficiency, product quality, supply chain responsiveness, customer satisfaction, cost savings, revenue growth, and market share. By monitoring these metrics over time and comparing them against predefined targets and benchmarks, manufacturers can assess the impact and ROI of digital transformation efforts and make informed decisions about future investments and strategies.
What are the key technologies driving digital transformation in manufacturing?
The key technologies driving digital transformation in manufacturing include IoT (Internet of Things), AI (Artificial Intelligence), automation, data analytics, cloud computing, robotics, 3D printing, and digital twins. These technologies work together to optimize processes, improve decision-making, and enable smarter and more connected manufacturing operations.
How long does it take to see tangible results from digital transformation in manufacturing?
The timeline for seeing tangible results from digital transformation in manufacturing can vary based on the complexity of the initiatives, the scale of implementation, and the specific goals set by the organization. While some improvements may be realized relatively quickly, the full benefits often become more apparent over the medium to long term.
Can small and medium-sized manufacturers benefit from digital transformation?
Yes, small and medium-sized manufacturers can benefit significantly from digital transformation. Many digital solutions are scalable and can be tailored to the specific needs and resources of smaller organizations. Digital transformation can help them improve efficiency, reduce costs, and compete effectively in the market.