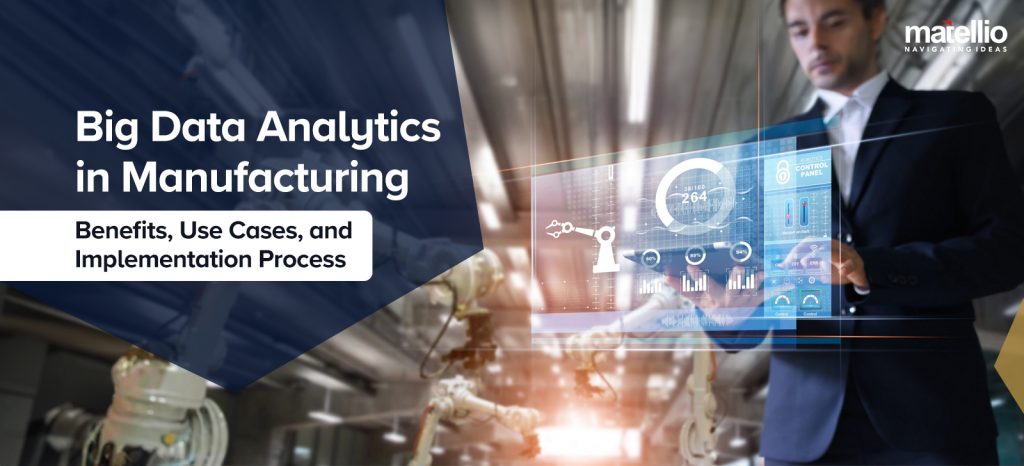
Are you juggling with countless moving parts, from supply chains to quality control, all while trying to stay ahead of the competition? Are tight deadlines, soaring costs, and unpredictable markets concerning you? Well, if you answered yes to any of these questions, big data analytics in manufacturing is for you!
In today’s fast-paced manufacturing landscape, staying competitive means embracing cutting-edge technologies like AI/ML, data analytics, and more. At the forefront of this revolution is big data analytics in manufacturing – a game-changing approach that’s transforming how you produce, innovate, and grow your business.
Imagine having a crystal ball that could predict equipment failures, optimize your supply chain, and reveal hidden opportunities. That’s the power of big data analytics. From inventory control and machine failure prediction to optimized supply chain and data-driven decisions, there are countless big data use cases in manufacturing! Intrigued?
So, as a trusted digital transformation services company, we are here to guide you on everything related to the use of big data analytics in the manufacturing industry. In this blog, we will explore top benefits, use cases, and a step-by-step implementation process. We will also uncover major challenges that might come during your transformation journey, and how Matellio can be your helping hand! But first.
Understanding Big Data Analytics in Manufacturing
Digital transformation in manufacturing is not just a trend; it’s a necessity. The rise of smart factories and interconnected devices has generated a wealth of data that, when analyzed effectively, can provide deep insights into every aspect of the manufacturing process. This is where big data analytics in manufacturing comes into play. It enables manufacturers to harness data to make informed decisions, predict outcomes, and optimize operations.
Unlike traditional data analysis, which often relies on small, structured datasets, big data analytics in manufacturing tackles massive volumes of diverse data from multiple sources across your entire production ecosystem.
Imagine having the power to analyze every aspect of your manufacturing process in real-time – from machine performance and quality control to supply chain logistics and customer demand patterns. That’s the promise of big data analytics in manufacturing. It’s not just about collecting data; it’s about turning that data into actionable insights that drive smarter decisions, boost efficiency, and help you move towards Industry 4.0.
The Revolutionary Benefits of Big Data Analytics in Manufacturing
Well, after the basic definition comes the question, “Why invest in big data analytics services? Are other companies doing it? If yes, what benefits can our company obtain or how can big data analytics in manufacturing resolve our business-specific issues?”
Well, here are the answers to all your questions!
According to a trusted source, the market for big data analytics is expected to reach $348.21 billion by the end of 2024! And that’s not all!
When you implement big data analytics in your manufacturing operations, you’re not just upgrading your technology – you’re unlocking a treasure trove of benefits that can transform your entire business. Let’s break down the game-changing advantages:
Supercharged Operational Efficiency
With big data analytics, you can identify bottlenecks, optimize production schedules, and streamline workflows like never before. Imagine reducing waste, minimizing downtime, and maximizing your resource utilization – all based on data-driven insights.
Unparalleled Product Quality
By analyzing vast amounts of production data, you can spot quality issues before they become problems. This proactive approach means fewer defects, higher customer satisfaction, and a stellar reputation for excellence.
Predictive Maintenance That Saves Millions
One of the most powerful applications of big data analytics in manufacturing is predictive maintenance. By analyzing equipment performance data, you can predict when machines are likely to fail and perform maintenance before costly breakdowns occur. This approach can slash downtime and maintenance costs dramatically.
Supply Chain Optimization at Your Fingertips
Big data analytics gives you unprecedented visibility into your supply chain. You can forecast demand more accurately, optimize inventory levels, and identify potential disruptions before they impact your production.
Optimal Quality Control and Defect Detection
Maintaining high-quality standards is crucial in manufacturing. Big data analytics applications enable real-time monitoring of production processes, identifying defects, and ensuring consistent quality. By analyzing data from various stages of production, manufacturers can detect deviations from quality standards early and take corrective actions promptly.
Cost Reduction and Profitability Boost
By optimizing every aspect of your operations, from energy consumption to raw material usage, big data analytics helps you cut costs and increase your bottom line. It’s like having a financial optimizer working 24/7 for your business.
Data-Driven Decision Making
With big data analytics, gut feelings are replaced by solid, data-backed insights. You’ll make smarter decisions faster, whether it’s about product development, market expansion, or strategic investments.
A Boost in Energy Efficiency
Energy consumption is a significant cost factor in manufacturing. Big data analytics helps manufacturers monitor and optimize energy usage, leading to significant cost savings. By analyzing energy consumption patterns, manufacturers can implement energy-saving measures and reduce their environmental footprint.
Beyond Basics: Benefits of Advanced Manufacturing Analytics with Big Data, AI, and Cloud Computing
Apart from the basic benefits of big data analytics in the manufacturing industry, you can also leverage advanced manufacturing analytics to boost your business growth. Integration of AI, ML, data visualization, and cloud computing is crucial and adds value to your big data analytics project. These technologies enable you to optimize processes, predict outcomes, and make data-driven decisions with high precision.
Let’s see how you can benefit from advanced manufacturing analytics:
Harnessing AI and Machine Learning
- Predictive Maintenance: AI and ML can analyze data from machinery sensors to predict equipment failures before they happen, allowing for proactive maintenance and reducing costly downtime. This predictive capability extends the lifespan of machinery and enhances overall reliability.
- Quality Control: AI algorithms can identify patterns in production data to detect quality issues early. This real-time monitoring helps maintain high product standards and reduces waste by addressing defects promptly.
- Production Optimization: Machine learning models optimize production schedules by analyzing data on machine performance, material availability, and demand forecasts. This ensures efficient resource utilization and meets market demand effectively.
Leveraging Cloud Computing
- Scalable Data Storage: Cloud integration services offer scalable storage solutions, capable of handling large volumes of manufacturing data. This flexibility ensures that manufacturers can store and manage data without the limitations of physical infrastructure.
- Real-Time Processing: Cloud platforms enable real-time data processing, crucial for applications like predictive maintenance and quality control. Immediate data analysis allows for swift responses to changing conditions on the factory floor.
- Enhanced Collaboration: Centralized data repositories in the cloud facilitate better collaboration across departments and locations, ensuring that all stakeholders have access to up-to-date information for informed decision-making.
Comprehensive Analytics and Visualization
- Descriptive and Diagnostic Analytics: These analytics provide insights into past performance and identify the root causes of issues, forming the foundation for more advanced analyses.
- Predictive and Prescriptive Analytics: Predictive analytics forecast future events such as equipment failures or demand changes, while prescriptive analytics recommend actions to optimize outcomes, such as adjusting production schedules or supply chain logistics.
- Interactive Dashboards: Customizable dashboards present data in an easily understandable format, helping decision-makers quickly grasp complex information and track key performance indicators (KPIs).
Interested to Leverage the Benefits of Big Data in Your Business? Contact Us Today!
Fill Our Form
Where Can You Use Big Data Analytics in Manufacturing – Use Cases for Your Business
After the robust benefits comes compelling use cases for big data analytics in manufacturing. The benefits of big data analytics in manufacturing that we discussed above aren’t just theoretical – they’re being realized by forward-thinking companies right now.
Want to see where they are using big data analytics in their companies? Let’s explore some real-world use cases that showcase the transformative power of this technology and how you can use it in your business:
Predictive Maintenance and Equipment Monitoring
Predictive maintenance is one of the most impactful big data use cases in manufacturing. By continuously monitoring equipment data, you can predict failures before they occur and schedule maintenance during non-productive hours. This approach not only reduces downtime but also enhances equipment reliability.
Real-Time Quality Control
Ensuring product quality is essential for maintaining customer satisfaction and meeting regulatory standards. With big data analytics applications, manufacturers can implement real-time quality control by analyzing data from sensors and production lines. This allows for immediate detection of defects and ensures that only high-quality products reach the market.
Inventory Management and Optimization
Effective inventory management is crucial for minimizing costs and meeting customer demand. Big data analytics in manufacturing enables manufacturers to optimize inventory levels by analyzing sales data, production schedules, and supply chain information. This ensures that manufacturers have the right amount of inventory at the right time, reducing carrying costs and avoiding stockouts.
Production Process Optimization
Optimizing production processes is a key focus for manufacturers looking to increase efficiency and reduce costs. By leveraging big data analytics in manufacturing, businesses can analyze data from production lines to identify inefficiencies and implement improvements. This leads to streamlined operations, reduced waste, and higher overall productivity.
Customer Demand Forecasting
Understanding customer demand is critical for planning production and inventory. Big data analytics allows manufacturers to forecast demand accurately by analyzing historical sales data, market trends, and external factors. This ensures that manufacturers can meet customer needs without overproducing or underproducing, leading to better customer satisfaction and profitability.
These use cases for big data analytics demonstrate its versatility and impact across various aspects of manufacturing. Whether you’re looking to optimize operations, improve quality, or drive innovation, big data analytics has a use case that can transform your business. Let’s select and implement the most promising use case of big data analytics in manufacturing for your company! Schedule a free 30-minute consultation with our experts.
Client Success Story – How a Company Tackled its Business Challenges with Matellio’s Expertise in Manufacturing Analytics
Problem
HESCO, a leading provider of third-party inspections for heavy machinery, faced significant challenges with their manual, offline safety inspection process. Their existing process was riddled with inefficiencies, including:
- Error-prone data entry
- Cumbersome and time-consuming procedures
- Inefficient progress tracking and document management
- Manual invoicing, leading to missed or overdue payments
Customers had to call with inspection details, followed by manual task allocation by admins. Inspectors visited sites, completed inspection sheets, and awaited manual review for certification or deficiency reports. This archaic method hindered operational efficiency and hampered historical data analysis.
Solution
HESCO partnered with Matellio to develop a state-of-the-art web-based platform to automate and streamline their safety inspection process.
The solution, built using ReactJS, NodeJS, and Postgres DB, offered several key features:
- Online Inspection Requests: Customers can now request inspections online, making the process more accessible and user-friendly.
- Efficient Task Management: Admins can manage inquiries, schedule appointments, and track tasks with automated reminders, ensuring efficient operations.
- Google Calendar Integration: This integration reduces scheduling conflicts and ensures punctuality.
- Customizable Inspection Sheets: These sheets, along with automated invoice generation, simplify administrative tasks.
- Real-Time Access: Both HESCO and their clients have real-time access to inspection details, certificates, deficiency forms, and invoices.
- Integrated Analytics Dashboard: This dashboard provides comprehensive insights into current, future, and completed inspections, facilitating informed decision-making.
Outcome
The implementation of Matellio’s web solution revolutionized HESCO’s inspection process. Key outcomes included:
- Increased Efficiency: Tasks that previously took two days now take just two hours, thanks to automation.
- Elimination of Manual Processes: Manual task assignment, progress tracking, and data management have been entirely automated, saving time and reducing human error.
- Enhanced Analytics: The analytics dashboard offers detailed insights into inspections, aiding in better decision-making.
- Improved Customer Experience: Clients benefit from a transparent, user-friendly online platform that simplifies communication and enhances their overall experience.
Matellio’s expertise in data analytics and custom manufacturing software development significantly boosted HESCO’s operational efficiency, elevated customer satisfaction, and supported business growth by replacing outdated manual processes with advanced, automated systems.
Do You Want a Similar Transformation for Your Company Using Big Data Analytics?
Share Your Requirements
The Implementation Process: Bringing Big Data Analytics to Your Factory Floor
Now that you’re excited about the potential of big data analytics in manufacturing, you might be wondering, “How do I actually implement this in my factory?” After all, there are many aspects related to big data analytics. For instance, analyzing the actual business concerns and IT gaps, hiring talented resources, creating strategies, identifying the right features, trends, and tools, etc.
Don’t worry – we’ve got you covered. Here’s a step-by-step guide to bringing the power of big data analytics to your manufacturing operations:
Assess Your Current Data Infrastructure
Before diving into big data analytics, it’s crucial to understand your starting point. This assessment phase involves:
- Auditing existing data sources: Identify all the places where you’re currently collecting data. This might include production line sensors, quality control systems, inventory management software, and even manual records.
- Evaluating data quality: Assess the accuracy, completeness, and timeliness of your current data. Are there gaps or inconsistencies that need addressing?
- Reviewing your IT infrastructure: Examine your current hardware and software capabilities. Do you have the necessary computing power and storage capacity to handle big data analytics?
- Identifying data silos: Look for isolated pockets of data that aren’t currently integrated with other systems. These silos often hold valuable insights when connected to the bigger picture.
This assessment will help you identify strengths to build upon and weaknesses to address in your big data strategy. You can leverage technology consulting services to streamline this step.
Define Clear Objectives and KPIs
With a clear understanding of your current state, it’s time to set your goals. This step is critical because it will guide all your future decisions. Consider:
- Specific business challenges: What problems do you want big data analytics to solve? This could range from reducing machine downtime to optimizing inventory levels.
- Measurable outcomes: Set concrete, quantifiable goals. For example, “Reduce unplanned downtime by 30%” or “Improve overall equipment effectiveness (OEE) by 15%.”
- Alignment with business strategy: Ensure your big data objectives support your overall business goals. This alignment will help secure buy-in from leadership and justify the investment.
- Time-bound targets: Set realistic timelines for achieving your objectives. This will help you track progress and make necessary adjustments along the way.
Remember, it’s often better to start with a few well-defined objectives rather than trying to solve everything at once.
Choose a Trusted Digital Transformation Services Company
Implementing big data analytics in manufacturing is a complex undertaking. Partnering with the right digital transformation services company can make all the difference. Look for a partner that:
- Has specific experience in manufacturing analytics software development
- Offers end-to-end services, from strategy consulting to system integration and support
- Demonstrates a track record of successful projects in your industry
- Can provide case studies and references from satisfied clients
- Has expertise in the latest big data technologies and methodologies
A trusted partner will guide you through the complexities of big data implementation, helping you avoid common pitfalls and accelerate your journey to data-driven manufacturing. Well, that’s what we do at Matellio!
Data Collection and Integration
This is where your big data analytics system starts to take shape. Key steps include:
- Implementing IoT devices and sensors: Deploy smart sensors throughout your manufacturing process to capture real-time data on machine performance, environmental conditions, and production metrics.
- Establishing data collection points: Identify critical points in your production process where data should be collected. This might include checkpoints for quality control, inventory tracking, or energy consumption monitoring.
- Integrating diverse data sources: Develop a strategy to bring together data from various systems – production equipment, ERP systems, supply chain management tools, and even external sources like weather data or market trends.
- Creating a centralized data platform: Implement a robust data management system that can handle the volume, velocity, and variety of big data. This might involve setting up a data lake or a cloud-based data warehouse.
- Ensuring data quality and consistency: Implement data cleansing and validation processes to ensure the accuracy and reliability of your data.
Read More: Discover how Data Quality as a Service can revolutionize your business by ensuring accurate, consistent, and reliable data for better decision-making and operational efficiency.
Build Analytical Models and Dashboards
With your data collected and integrated, it’s time to turn it into actionable insights. Your chosen development partner will help you:
- Develop predictive models: Create algorithms that can forecast maintenance needs, predict quality issues, or optimize production schedules based on historical and real-time data.
- Implement machine learning: Use advanced analytics techniques to uncover hidden patterns and continuously improve your models over time.
- Design intuitive dashboards: Create user-friendly interfaces that present key insights in an easily digestible format. Customize dashboards for different roles within your organization.
- Enable real-time analytics: Set up systems that can process and analyze data as it’s generated, allowing for immediate action when issues arise.
- Incorporate descriptive, predictive, and prescriptive analytics: Go beyond just describing what happened to predicting what will happen and recommending actions.
Train Your Team and Foster a Data-Driven Culture
The final step is ensuring your team can effectively use and benefit from your new big data analytics capabilities:
- Provide comprehensive training: Offer workshops and hands-on sessions to familiarize employees with new tools and dashboards.
- Develop data literacy: Help all employees understand the basics of data analysis and interpretation, not just your data scientists.
- Encourage data-driven decision making: Lead by example and incentivize the use of data in daily operations and strategic planning.
- Create cross-functional teams: Bring together individuals from different departments to collaborate on data-driven projects.
- Establish a continuous improvement mindset: Regularly review and refine your big data analytics processes based on feedback and results.
Remember, implementing big data analytics in manufacturing is an ongoing process. Start with a pilot project, learn from your experiences, and gradually expand your capabilities. With persistence and the right approach, you’ll transform your manufacturing operations into a data-driven powerhouse, setting new standards for efficiency, quality, and innovation in your industry.
Are you ready to embark on this transformative journey? The future of smart, data-driven manufacturing is within your reach – and it starts with taking that first step towards implementing big data analytics in manufacturing. Contact our experts today!
Overcoming Challenges in Implementing Big Data Analytics
Well, well, well, so now you have explored the benefits, the uses cases, a successful case study, and a step-by-step process for implementing big data analytics in manufacturing. But is that all?
No, there are some other challenges that you might have to consider when using analytics for manufacturing.
Data Security and Privacy
In big data analytics for manufacturing, your data is both an asset and a potential liability. As you collect information from various sources, you create attractive targets for cybercriminals. Protecting proprietary processes, customer data, and operational information is crucial. A data breach could lead to financial losses and reputational damage. Robust data security is now a fundamental business imperative.
To address these concerns:
- Implement robust encryption for all data
- Use role-based access controls
- Conduct regular security audits
- Train employees on data security best practices
- Ensure compliance with data protection regulations
Integration with Legacy Systems
Integrating modern big data systems with existing legacy infrastructure is a significant challenge for many manufacturers. Legacy systems weren’t designed for big data analytics, creating substantial hurdles. Incompatible data formats, outdated protocols, and limited processing power complicate integration. Successfully bridging old and new systems is crucial for leveraging historical data alongside new data streams.
To overcome these hurdles:
- Use middleware for data transformation
- Develop custom APIs for system communication
- Consider a phased migration approach
- Implement a data warehouse as an intermediary
- Focus on change management for employee adaptation
Skill Gap and Talent Acquisition
Big data analytics in manufacturing requires a unique blend of data science expertise and manufacturing domain knowledge. This specialized skill set is rare, creating a significant talent gap. Manufacturers face the challenge of upskilling existing employees and attracting new data science talent. Building an effective team is crucial for driving innovation and maintaining competitiveness.
To address this challenge:
- Develop training programs for existing employees
- Partner with educational institutions
- Create a data-driven organizational culture
- Offer competitive compensation to attract talent
- Form cross-functional teams for knowledge sharing
- Provide continuous learning opportunities
Scalability and Future-Proofing
The big data landscape is constantly evolving, with growing data volumes and emerging technologies. Your analytics system must be able to scale and adapt to these changes. Consider future data volumes, new data sources, and emerging analytics technologies. A system that can’t evolve could quickly become obsolete, hindering strategic decision-making.
To ensure scalability and future-proofing:
- Explore cloud-based solutions for flexibility
- Design a modular system architecture
- Use open standards and APIs for future compatibility
- Conduct regular technology assessments
- Implement flexible data models
- Incorporate adaptable machine learning capabilities
Addressing these challenges builds a robust foundation for your data-driven manufacturing future. However, you must partner with a trusted data analytics services company that can offer expert assistance throughout your transformation journey. That’s exactly where Matellio comes in!
Leverage Free 30-Minute Expert Consultation to Overcome Big Data Analytics Challenges!
Book Your Slot
Why Partner with Matellio for Your Big Data Analytics Journey
Implementing big data analytics in manufacturing can be complex, but you don’t have to go it alone. At Matellio, we specialize in guiding manufacturers like you through every step of the big data analytics journey. Here’s why we’re the ideal partner for your transformation:
Expertise in Custom Manufacturing Software Development
We understand that every manufacturing operation is unique. Our team of experts can develop tailored solutions that address your specific needs and challenges.
Tailored Data Consultation
Our data consultation services help you make sense of your data landscape, identify opportunities, and develop strategies that drive real business value.
Comprehensive Digital Transformation Services
Big data analytics is just one piece of the Industry 4.0 puzzle. Our digital transformation services ensure that your entire operation is ready for the future of manufacturing.
Cutting-Edge IoT and AI Integration
Our IoT development services and AI integration capabilities allow us to create powerful, interconnected systems that maximize the potential of your big data analytics implementation.
Also Read: IoT Data Analytics: Benefits, Use Cases, and Implementation
End-to-End Technology Consulting
From initial assessment to ongoing support, our technology consulting services ensure that your big data analytics initiative aligns with your overall business strategy and delivers measurable results.
Expertise in RPA Development Services
At Matellio, we specialize in offering tailored RPA development services that are designed to enhance your manufacturing operations. Our expertise in RPA development services ensures seamless integration and automation of your repetitive tasks, leading to increased efficiency and productivity.
Are you ready to unlock the full potential of your manufacturing operations? Contact us today, and let’s start your big data analytics journey together. Your smarter, more efficient, and more profitable manufacturing future is just a conversation away.
FAQ’s
Q1. How can big data analytics improve my manufacturing operations?
Big data analytics can enhance manufacturing operations by optimizing production schedules, improving product quality, predicting equipment failures, and providing real-time insights that help in making informed decisions.
Q2. What are the key steps to implementing big data analytics in manufacturing?
The implementation process includes assessing your current data infrastructure, defining clear objectives and KPIs, collecting and integrating data, building analytical models and dashboards, and training your team to foster a data-driven culture.
Q3. Why should I choose Matellio for my big data analytics needs in manufacturing?
Our comprehensive digital transformation services, expertise in custom manufacturing software development, and a proven track record of successful projects in the manufacturing industry, ensuring that your big data analytics initiative aligns with your business strategy and delivers measurable results.
Q4. How does Matellio support the integration of AI and IoT in manufacturing analytics?
We provide cutting-edge IoT development services and AI integration capabilities, creating interconnected systems that maximize the potential of your big data analytics implementation, leading to enhanced operational efficiency and innovation.
Q5. What kind of ongoing support can I expect from Matellio for my big data analytics project?
Matellio offers end-to-end technology consulting services, from the initial assessment to ongoing support, ensuring that your big data analytics system remains aligned with your evolving business needs and continues to deliver value.