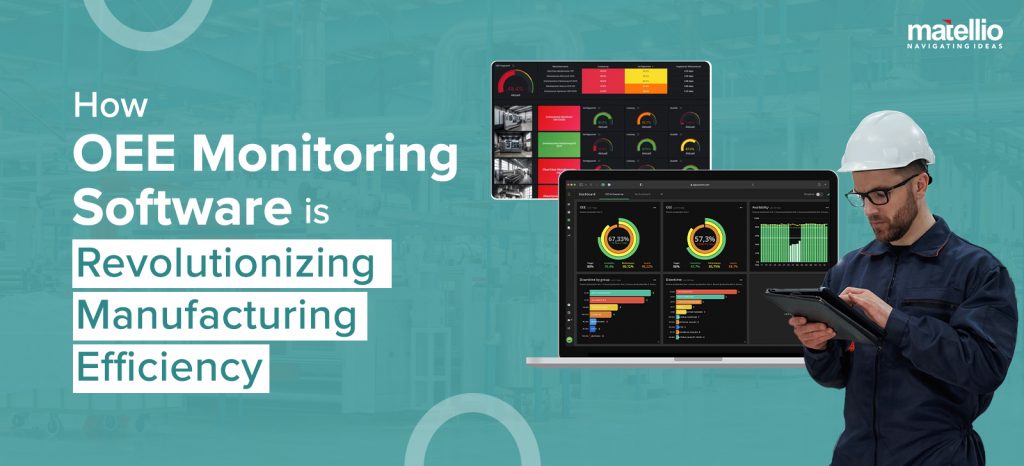
In today’s competitive manufacturing landscape, maximizing productivity, minimizing downtime, and maintaining high-quality standards are essential for growth and profitability. One of the most effective tools that manufacturers are leveraging to achieve these goals is Overall Equipment Effectiveness (OEE) monitoring software. OEE software solutions provide real-time visibility into production processes, streamline operations, and offer actionable insights, helping companies boost operational efficiency, reduce waste, and improve asset utilization. In this blog, we’ll explore how OEE monitoring software is transforming manufacturing, the core features it offers, and how building custom OEE solutions tailored to specific operational needs.
What is OEE Monitoring Software?
OEE monitoring software is a powerful digital solution designed to measure the effectiveness of manufacturing equipment and processes. It calculates OEE by monitoring key metrics: availability, performance, and quality. By providing real-time insights into these areas, OEE software enables manufacturers to identify bottlenecks, reduce downtime, and optimize their production lines. In an industry where precision and efficiency are paramount, OEE monitoring software is vital for manufacturers striving to maintain a competitive edge.
Source: Markets and Markets
Key Benefits of Developing OEE Monitoring Software
Implementing OEE monitoring software offers transformative advantages, empowering manufacturers to optimize production, reduce downtime, and improve profitability. Here’s a breakdown of the primary benefits:
Increased Operational Efficiency
With overall equipment effectiveness software, manufacturers can monitor machine performance, availability, and quality in real-time. By identifying inefficiencies, this software enhances productivity, reducing downtime and streamlining operations.
Improved Decision-Making
Real-time data provided by OEE solutions supports managers in making accurate decisions regarding maintenance, production scheduling, and resource allocation. This data-driven approach results in faster, more strategic responses to operational challenges.
Enhanced Asset Utilization
OEE software tracks equipment effectiveness, allowing manufacturers to maximize asset use. This OEE monitoring system helps minimize wear and tear, extending the lifespan of machinery and improving overall productivity.
Reduced Downtime
With proactive maintenance alerts, OEE software solutions enable teams to address issues before they result in costly breakdowns. Automated notifications help streamline maintenance tasks and avoid unexpected stoppages, keeping production schedules on track.
Cost Savings
By reducing downtime and improving production quality, OEE monitoring software significantly reduces operational costs. The software minimizes waste, enhances asset utilization, and supports better inventory management, contributing to long-term cost savings.
Quality Control
OEE software solutions provide valuable insights into quality metrics, allowing manufacturers to maintain consistent standards. Real-time tracking ensures that products meet quality benchmarks, reducing the risk of defects and improving customer satisfaction.
Real-Time Transparency
Custom-built OEE software offers visibility across departments by providing a centralized view of production metrics. This transparency fosters better collaboration, ensuring all teams work with up-to-date information for effective order handling and customer support.
Continuous Improvement
Leveraging data insights, digital transformation services aligned with OEE systems promote continuous improvement in manufacturing processes. By addressing recurring issues and streamlining workflows, companies can achieve incremental changes that enhance long-term operational efficiency.
Compliance and Reporting
With integrated reporting capabilities, overall equipment effectiveness software simplifies tracking for regulatory compliance and audits. Automated reporting enables businesses to maintain comprehensive records, ensuring compliance with industry standards and regulatory requirements.
Essential Features of OEE Monitoring Software
While developing the software for OEE, it’s essential to prioritize features that align with your operational objectives. The table below compares core and next-gen features designed to enhance the effectiveness of software. Partnering with a provider that offers technology consulting services can further ensure that the solution integrates seamlessly with your unique processes and long-term goals.
Core Features | Next-Gen Features |
Real-Time Data Collection | Predictive Maintenance Using AI |
Automated OEE Calculations | Machine Learning for Anomaly Detection |
Downtime Tracking | Advanced Data Visualization |
Reporting and Analytics | IoT Integration |
Integration with ERP/MES Systems | Cloud Connectivity |
Quality Monitoring | Edge Computing for Real-Time Processing |
Root Cause Analysis | Digital Twin for Real-Time Equipment Modeling |
Customizable Alerts and Notifications | AI-Powered Predictive Quality Control |
Production Scheduling | Multi-Device Access |
Scrap and Waste Analysis | Remote Monitoring and Management |
Operator Performance Tracking | Self-Learning Algorithms |
These features empower your business with the tools needed to improve efficiency, prevent equipment issues, and maintain consistent quality.
Add The Power of Next-Gen Features to Upgrade Your Software!
Connect With Us
How OEE Monitoring Software Works
OEE (Overall Equipment Effectiveness) monitoring software is designed to provide real-time insights into production performance, helping manufacturers optimize efficiency, reduce downtime, and improve quality. Here’s an in-depth look at how this software works to enhance manufacturing operations:
Data Collection
- Real-Time Tracking: OEE monitoring software continuously collects data from machines, sensors, and production lines, capturing key metrics on availability, performance, and quality. This provides immediate visibility into production status and equipment conditions, enabling quick responses to any operational issues.
- Multi-Source Data Integration: The software gathers data from multiple sources, creating a comprehensive overview of production activities. For enhanced analytics, Custom Machine Learning Solutions can be integrated to analyze and predict equipment performance trends, leading to better resource allocation.
Automated OEE Calculation
- Real-Time OEE Score Calculation: Using collected data, OEE software solutions calculate OEE scores in real time, giving an immediate view of overall efficiency. Calculations are based on:
- Availability: Measures uptime and captures downtime data.
- Performance: Evaluate speed losses by comparing actual cycle time to optimal cycle time.
- Quality: Tracks defect rates and the quality of finished products.
- KPI Dashboards: Real-time scores are displayed in dashboards, allowing managers to quickly access actionable metrics and identify areas for improvement.
Root Cause Analysis
- Downtime Analysis: For each downtime instance, OEE solutions provide root cause analysis to identify underlying reasons, allowing teams to address issues efficiently.
- Quality Deviation Tracking: When quality issues occur, the software flags incidents and performs analyses to reduce recurring quality issues and scrap rates.
- Historical Trends: Identifying downtime and quality trends over time helps teams address recurring issues and refine preventative maintenance strategies.
Predictive Alerts
- Trend Analysis: By analyzing historical data and equipment performance patterns, overall equipment effectiveness software identifies trends that signal potential equipment issues.
- Automated Alerts: Predictive analytics capabilities trigger alerts to notify maintenance teams of potential issues, reducing unscheduled downtime and extending equipment lifespan.
- Preventative Maintenance Scheduling: Predictive insights also inform proactive maintenance schedules, optimizing equipment health.
Reporting and Analytics
- Detailed Reports: The software provides comprehensive reports on OEE, including shift-by-shift analysis, operational trends, and specific equipment metrics. These insights are crucial for continuous improvement.
- Comparative Analytics: The OEE monitoring system includes tools for comparing performance across production lines or shifts, helping managers implement best practices organization-wide.
- Customizable Dashboards: Real-time dashboards provide visibility into production metrics, enabling data-driven decisions that enhance productivity.
Integration with ERP and MES Systems
- Unified Data Flow: OEE software solutions integrate with ERP (Enterprise Resource Planning) and MES (Manufacturing Execution Systems) to unify production, inventory, and quality metrics across the organization.
- Improved Decision-Making: Integration allows for synchronized production data, enabling improved forecasting and resource planning.
- Cross-Functional Insights: By integrating OEE software with business systems, managers gain a holistic view of operations, facilitating more cohesive decision-making and streamlined workflows.
Also Read: Manufacturing Execution System Development – Features and Cost
Application of OEE Monitoring Software
OEE (Overall Equipment Effectiveness) monitoring software provides transformative benefits across various manufacturing industries, helping them optimize efficiency, improve quality, and reduce costs. Here’s how different sectors leverage OEE monitoring software:
Automotive Manufacturing
- Precision Tracking: Automotive manufacturers rely on OEE solutions to maintain high standards for safety and precision. Real-time tracking of performance and quality metrics helps meet stringent regulatory requirements.
- Downtime Minimization: With automated root cause analysis, downtime is minimized, and maintenance schedules are optimized, which is crucial in maintaining productivity.
- Integration with IoT: By leveraging IoT development services, OEE software enables real-time data collection from various equipment, enhancing production insights and optimizing workflow.
Food and Beverage Production
- Quality and Compliance Monitoring: OEE monitoring systems play a key role in quality control by tracking production speed, downtime, and quality metrics, ensuring compliance with health and safety regulations.
- Waste Reduction: By providing insights into areas of inefficiency, OEE software solutions help reduce material waste, contributing to cost savings and a smaller environmental footprint.
- Predictive Maintenance: OEE monitoring’s predictive alerts notify teams before equipment failure, reducing unexpected breakdowns and maintaining production flow.
Pharmaceutical Manufacturing
- Regulatory Compliance and Quality Control: Overall equipment effectiveness software provides real-time monitoring of production quality, ensuring compliance with strict regulatory standards.
- Early Error Detection: By identifying quality issues at early stages, the software minimizes the risk of recalls and associated costs, protecting both consumer health and brand reputation.
- Enhanced Asset Management: Continuous monitoring optimizes asset utilization, ensuring that critical pharmaceutical equipment operates at peak performance.
Also Read: Unleashing the Power of Data Analytics in Pharmaceutical Manufacturing
Electronics Manufacturing
- Precision and Quality Control: Electronics manufacturing demands high precision, and OEE software solutions ensure consistency in production by tracking machine performance and identifying potential inefficiencies.
- Environmental Condition Monitoring: Integration with IoT sensors provides real-time tracking of environmental factors, such as temperature and humidity, ensuring that equipment runs under optimal conditions.
- Yield Optimization: By monitoring defect rates, the software helps improve yield rates, reduce rework costs, and ensure that finished products meet high-quality standards.
Textile and Apparel Manufacturing
- Optimized Production Scheduling: OEE monitoring software helps textile manufacturers by providing real-time insights into machine availability and performance, allowing for better production scheduling and quick responses to demand shifts.
- Enhanced Product Quality: Real-time monitoring of quality metrics ensures consistency in large-scale production, whether producing fabrics, apparel, or accessories.
- Seamless ERP Integration: When integrated with ERP systems, OEE monitoring solutions provide a centralized platform for tracking production metrics, ensuring streamlined workflows across production cycles.
Wish to Learn About the Development Cost of OEE Monitoring Software?
Request a Quote!
Steps to Develop OEE Monitoring Software
Developing OEE (Overall Equipment Effectiveness) monitoring software is a multi-stage process that requires thorough planning and a clear understanding of the specific needs of manufacturing environments. Each phase plays a vital role in ensuring the software meets the operational and performance goals of manufacturers. Here’s an in-depth look at the essential steps:
Conduct Market Research and Analysis
- Objective: Understanding market needs, identifying gaps, and pinpointing customer pain points are crucial to creating a solution that adds real value to end-users.
- Competitor Analysis: Analyze existing OEE software solutions to understand current capabilities, strengths, and weaknesses. This can provide insight into what’s working in the market and reveal opportunities for improvement.
- Customer Insights: Gathering feedback from potential users in the manufacturing sector can clarify expectations and highlight essential features. Insights on customer challenges—such as frequent downtime, data silos, or inefficient resource allocation—guide the development of practical and user-centric features.
Define Objectives and Requirements
- Setting Objectives: Establish specific goals, such as improving productivity, enhancing real-time tracking, or integrating predictive maintenance. These objectives will form the foundation of the software.
- Feature Prioritization: Identify essential functionalities, including real-time data collection, OEE calculations, downtime tracking, and root cause analysis. Depending on the target market, additional features like advanced data visualization and machine learning for anomaly detection can also be considered.
- Requirement Documentation: Detailed requirement documentation is essential for a smooth development process. It outlines the core requirements of the software, focusing on functionality, scalability, performance, and security standards, which ultimately guides both developers and stakeholders.
Select the Development Team
- Partnering with Experts: Collaborate with a software development company experienced in building solutions for industrial or manufacturing sectors. Expertise in manufacturing workflows ensures a more seamless development experience.
- Assembling a Multi-Disciplinary Team: The development team should include specialists in software engineering, UX/UI design, IoT integration, machine learning, and QA testing. Each role is critical to building software that’s not only functional but also user-friendly and reliable.
- Cost Efficiency and Timeline Management: Outsourcing to an experienced team can reduce overhead costs and speed up the timeline, ensuring the project stays on track and within budget.
Choose the Technology Stack
Selecting scalable and flexible technologies is essential for building a robust OEE monitoring system that supports real-time data processing and growth in manufacturing environments. Below is an organized technology stack tailored for OEE monitoring software, presented in table format for clarity.
Component | Technology Options |
IoT Integration | MQTT, OPC-UA, ThingWorx, Azure IoT Hub |
Machine Learning & AI | TensorFlow, PyTorch, Scikit-Learn, Custom Machine Learning Solutions |
Cloud Integration | AWS IoT, Microsoft Azure, Google Cloud Platform |
Frontend Framework | React, Angular, Vue.js |
Backend Framework | Node.js, Django, Ruby on Rails |
Database | MySQL, PostgreSQL, MongoDB |
Data Visualization | Grafana, Power BI, Tableau |
Security | SSL/TLS, OAuth 2.0, JWT |
API Integration | RESTful APIs, GraphQL |
Deployment Tools | Docker, Kubernetes |
Develop the MVP Using Agile Methodology
- Minimum Viable Product (MVP) Development: Start with an MVP focused on delivering core functionalities like real-time data collection, OEE calculations, and downtime tracking. The MVP provides a working model to gather initial user feedback.
- Iterative Development with Agile: Agile methodology allows the development team to work in sprints, enabling frequent updates, testing, and feedback. This approach ensures continuous improvement based on real-time feedback from users and stakeholders.
- Cross-Functional Collaboration: Encourage collaboration between developers, product managers, and end-users to ensure the software meets user expectations and achieves the desired outcomes for production efficiency.
Testing and Quality Assurance
- Comprehensive Testing: QA should cover various testing types, including:
- Functional Testing: Verifies that each feature operates as expected.
- Performance Testing: Ensures the software can handle high volumes of real-time data without lag or failure.
- Usability Testing: Checks that the interface is intuitive and easy to navigate for operators and managers.
- Automation for Efficiency: Test automation tools streamline repetitive tests, improve coverage, and detect potential issues faster.
- Bug Tracking and Fixes: Use a bug-tracking system to log, prioritize, and resolve issues as they arise. Addressing issues early in the development cycle reduces costly delays and enhances software reliability.
Deployment and Post-Launch Support
- Deployment Planning: Use deployment tools like Docker or Kubernetes to facilitate smooth launches, especially for distributed manufacturing environments where the software needs to run across multiple machines or sites.
- Data Migration and Configuration: For companies upgrading from legacy systems, data migration and configuration are essential. This step ensures that historical data is preserved and integrated into the new OEE monitoring software.
- Ongoing Support and Maintenance: Continuous support is crucial for any successful software rollout. Provide bug fixes, security updates, and feature enhancements based on user feedback and evolving needs.
- User Training and Documentation: Offer training sessions and detailed documentation to help users maximize the software’s potential. Familiarizing teams with the software ensures smoother adoption and minimizes operational disruption.
Future Trends in OEE Monitoring Software
OEE monitoring software is evolving with innovative advancements, empowering manufacturers to achieve higher productivity, reduce downtime, and optimize operations. Here are the key trends that are driving the future of OEE solutions:
AI and Machine Learning Integration
AI integration services are revolutionizing OEE monitoring by enabling predictive maintenance capabilities. By analyzing historical performance data, AI and machine learning technologies forecast potential equipment failures, allowing maintenance teams to proactively address issues before they escalate. This predictive approach not only minimizes unplanned downtime but also reduces maintenance costs and extends the lifespan of critical machinery.
Enhanced IoT Integration
The integration of IoT sensors into manufacturing equipment enables real-time monitoring of essential metrics like temperature, vibration, and production speed. This functionality in OEE systems allows manufacturers to adjust operations based on live data, optimize resource allocation, and respond quickly to potential issues. IoT enhances the responsiveness and accuracy of overall equipment effectiveness software, enabling more efficient and reliable production.
Cloud-Based Solutions for Remote Accessibility
Cloud-based OEE software solutions provide instant, remote access to production metrics, which is especially advantageous for enterprises with multiple facilities. These cloud solutions offer scalability, allowing manufacturers to expand their monitoring capabilities with minimal infrastructure investment. By integrating cloud-based systems, teams can collaborate seamlessly, making it easier to analyze data and implement improvements from any location.
Robotic Process Automation (RPA)
RPA is streamlining many repetitive tasks involved in OEE monitoring, such as report generation, data entry, and compliance documentation. By automating these processes, RPA reduces the likelihood of human error, speeds up data management, and enables staff to focus on high-value activities. This efficiency improves the functionality of OEE software solutions by making data more accessible and accurate.
Real-Time Data Visualization and Interactive Dashboards
Real-time data visualization offers an intuitive way for operators and managers to monitor production metrics. Advanced dashboards within OEE monitoring software provide real-time insights into availability, performance, and quality metrics, helping teams to identify and address issues immediately. Interactive dashboards also allow users to drill down into specific areas, enabling data-driven decisions and improving overall operational efficiency.
Predictive Analytics and Prescriptive Insights
With predictive analytics, OEE solutions can go beyond traditional monitoring by forecasting potential production issues and equipment needs. By analyzing historical and real-time data, these systems provide prescriptive insights, offering recommendations for optimal resource allocation and operational adjustments. This capability helps manufacturers maintain efficiency and maximize productivity across their production lines.
Edge Computing for On-Site Data Processing
Edge computing is revolutionizing OEE monitoring systems by enabling real-time data processing at the equipment level. This reduces latency and allows instant insights even in low-connectivity environments. For large-scale manufacturing operations, edge computing is critical, providing fast response times for mission-critical decisions directly on the production floor.
Consult The Experts to Explore How These Trends Can Enhance Your Business
Book A Call Now!
How Matellio Can Help with OEE Monitoring Software Development
Investing in OEE monitoring software development goes beyond meeting industry standards; it’s about setting your business up for sustainable growth and operational excellence. With the right enterprise software development services, you can track production efficiency, reduce downtime, and make data-driven decisions to improve productivity in a dynamic manufacturing environment.
Partnering with an expert like Matellio is essential to achieve these goals. We provide advanced technology solutions tailored to your manufacturing needs, helping you optimize equipment effectiveness and maximize output.
Our experienced developers are proficient in technologies specific to OEE monitoring, ensuring that your system is not only effective today but scalable for future demands. We understand the unique challenges manufacturers face, and our customized solutions are designed to address your operational goals, improve efficiency, and enhance your production capabilities.
Our expertise covers key areas such as real-time data collection, predictive maintenance, downtime tracking, and analytics. We integrate essential features to create a seamless experience for your teams, enabling faster data analysis, enhanced machine performance, and more informed decision-making.
We also provide comprehensive IoT consulting services to help you choose the most effective tech stack, integrations, and strategies for your OEE monitoring software. From initial consultation and planning to implementation, IoT integration, testing, deployment, and ongoing support, we offer end-to-end solutions, ensuring a seamless process from start to finish—all under one roof.
If you’re ready to boost your production efficiency and reduce downtime, contact us today by filling out the form and connecting with our team of experts.
FAQ’s
Q1. How do you ensure the security and privacy of data in OEE monitoring software?
We prioritize data security and privacy by implementing advanced encryption techniques to protect data both in transit and at rest. We enforce strict access controls to prevent unauthorized access and conduct regular security audits and penetration testing to proactively identify and address any vulnerabilities.
Q2. Are you experienced with manufacturing industry standards, and will the software be compliant with these regulations?
Yes, our team has extensive experience in developing software solutions that comply with industry standards for manufacturing. Our OEE monitoring software is designed to meet relevant regulatory and operational requirements, providing a compliant and secure solution.
Q3. What is the estimated timeline for developing and deploying OEE monitoring software?
The development timeline for OEE monitoring software depends on project scope, feature complexity, and specific business requirements. After defining the project's full scope, we will work closely with you to establish a timeline that aligns with your goals. We can provide a more accurate estimate after an in-depth consultation.
Q4. What post-launch support and maintenance services do you offer?
We provide a complete range of post-launch support and maintenance services to ensure smooth software operations after deployment. Our services include bug fixes, performance enhancements, feature updates, and ongoing technical support. We offer flexible maintenance plans tailored to your needs, ensuring continuous updates and system reliability as your business evolves.
Q5. What are the projected costs associated with developing OEE monitoring software?
The cost of developing OEE monitoring software varies based on factors such as project scope, feature complexity, and specific functionalities. Matellio offers transparent cost estimates tailored to your unique business needs, ensuring a high-quality solution that fits within your budget and business goals.