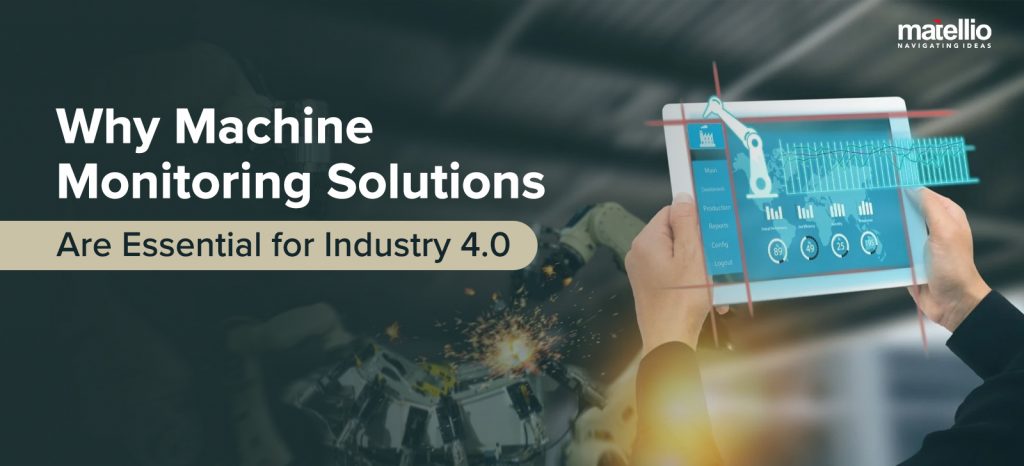
Industry 4.0 is transforming the way businesses operate by integrating advanced digital technology into production and operational processes. Machine monitoring solutions have become a cornerstone of this evolution, providing real-time insights that boost productivity, optimize efficiency, and significantly reduce costs. From manufacturing and logistics to energy production, industries are leveraging these solutions to streamline processes and enhance decision-making. Let’s explore how machine monitoring can provide an edge in the modern industrial landscape.
What Are Machine Monitoring Solutions?
Machine monitoring solutions refer to the use of digital technology to track, collect, and analyze data from machinery in real-time. Typically composed of sensors, IoT technology, and data visualization platforms, these solutions offer a centralized view of equipment performance, allowing operators to make informed decisions that prevent downtime and improve productivity. By enabling predictive maintenance, alerting operators to issues, and capturing valuable performance data, machine monitoring is essential to the success of Industry 4.0 initiatives.
Key Benefits of Custom-Building Machine Monitoring Solutions
Implementing a custom-built machine monitoring solution offers numerous advantages, empowering industries to streamline operations, reduce costs, and improve productivity. Below is a detailed look at some of the most impactful benefits:
Enhanced Productivity
With real-time data, custom-built machine monitoring software enables operators to identify inefficiencies and bottlenecks specific to their setup. This targeted data allows quick adjustments to optimize processes, reduce idle time, and maximize output, ensuring a highly efficient and tailored production system.
Predictive Maintenance
A custom machine condition monitoring system allows for predictive maintenance by tracking specific performance indicators like vibration, temperature, or pressure. Early identification of potential issues prevents costly breakdowns, enabling tailored maintenance schedules that extend equipment lifespan and reduce unexpected downtime.
Improved Safety Standards
Safety is paramount in industrial settings, and a customized industrial machine monitoring system offers enhanced safety controls. By tracking critical operational conditions, this system can detect hazardous conditions unique to the equipment and environment, allowing for proactive safety measures and a more secure environment for equipment and personnel.
Cost Savings
Customized solutions offer focused data analysis, helping companies save on unexpected repairs and energy costs. A custom equipment monitoring system identifies early maintenance needs, leading to cost-effective repairs and fewer replacements. By analyzing real-time data specific to your equipment, companies can reduce operational costs and achieve a quicker return on investment.
Data-Driven Decision Making
Customized software provides valuable insights for strategic decision-making, offering tailored reports and performance data. Management can make data-backed decisions about equipment upgrades, process optimizations, and operational improvements. This custom approach aligns with digital transformation services to build a culture of data-driven improvements across departments.
Reduced Environmental Impact
With a focus on sustainability, custom machine monitoring solutions promote energy efficiency and waste reduction specific to a company’s goals and regulatory needs. Tracking energy usage and emissions in real time allows companies to find ways to minimize their carbon footprint while adhering to environmental standards, enhancing both compliance and operational efficiency.
Optimized Resource Allocation
A custom industrial machine monitoring system provides tailored insights into resource usage, allowing organizations to allocate assets and resources precisely where needed. Customization ensures that resources are neither underutilized nor overused, maximizing asset utilization, improving production planning, and increasing return on investment.
Top Features to Look for in Machine Monitoring Solutions
When considering investing in machine monitoring software development, it’s essential to look for features that align with your business needs. Here’s a table showcasing some core features alongside next-generation capabilities for a robust monitoring setup.
Core Features | Next-Gen Driven Features |
Real-Time Monitoring | Predictive Analytics |
Alarm and Alert System | AI-Based Anomaly Detection |
Data Visualization and Reporting | Advanced Data Integration |
Maintenance Scheduling and History | Edge Computing for On-Site Data Processing |
Cloud Connectivity | Remote Diagnostics and Troubleshooting |
Energy and Resource Usage Monitoring | Digital Twin Technology for Simulation |
Multi-Device Accessibility | Automated Workflow Integration |
Each of these features plays a vital role in creating a comprehensive, future-proof solution for industrial applications.
Add These Exclusive Next-Gen Driven Features Within Your Machine Monitoring Software!
Contact Us!
Challenges Solved by Developing Custom Machine Monitoring Solutions
Custom-built machine monitoring solutions address numerous industrial challenges, using real-time data, predictive analytics, and IoT integration to streamline operations and boost efficiency. Here’s how these solutions tackle common issues in modern industries:
Downtime and Unplanned Failures
Challenge: Unplanned machine downtime can halt production and increase costs, as repairs and emergency responses are often needed unexpectedly.
Solution: Custom monitoring software provides real-time alerts and predictive analytics, enabling operators to address issues proactively. This minimizes downtime and keeps production running smoothly. By using advanced algorithms from custom machine learning solutions, the system can identify trends and predict potential issues, allowing for preemptive action to avoid costly disruptions.
Lack of Real-Time Insights
Challenge: Without continuous data flow, businesses struggle with limited visibility into machine performance and cannot make timely decisions to optimize operations.
Solution: Industrial machine monitoring systems equipped with IoT integration offer live insights into equipment status, performance, and operational health. This real-time visibility allows teams to make swift, informed adjustments, improving efficiency across production lines. For companies aiming to maintain agility in fast-paced environments, real-time monitoring software is a critical asset.
High Maintenance Costs
Challenge: Reactive maintenance approaches often lead to higher costs due to frequent repairs and unplanned downtime, which strain both resources and budgets.
Solution: By incorporating predictive maintenance through machine condition monitoring systems, companies can detect wear-and-tear signs early. This allows for repairs to be conducted as needed rather than on a fixed schedule, reducing overall maintenance costs. Custom machine monitoring setups offer the flexibility to tailor maintenance schedules, aligning with actual equipment conditions rather than general estimations.
Inconsistent Quality Control
Challenge: Variability in machine performance can lead to inconsistent product quality, creating waste and inefficiencies.
Solution: Equipment monitoring systems track key parameters like temperature, speed, and pressure to ensure machines operate within optimal ranges. This continuous monitoring helps maintain quality standards by catching deviations early. For industries that rely on stringent quality control, such as automotive or food processing, a custom-built monitoring system is essential to ensure consistent product output.
Poor Resource Utilization
Challenge: Inefficient resource allocation, including under- or over-utilization of machines, can lead to unnecessary costs and wasted capacity.
Solution: Machine monitoring systems provide insights into machine usage, helping businesses allocate resources more effectively. By understanding usage patterns, companies can prevent overloading certain machines while ensuring underutilized equipment is put to better use, enhancing overall productivity. For custom-built solutions, these insights can be further refined with machine learning solutions tailored to resource optimization, ensuring assets are maximized without overexertion.
Compliance with Safety and Environmental Regulations
Challenge: Compliance with safety and environmental regulations is crucial, as violations can result in costly penalties and reputational damage.
Solution: Custom machine monitoring solutions offer detailed tracking of emissions, energy use, and other critical metrics. This allows companies to meet regulatory standards by identifying and mitigating compliance risks in real time. Automated alerts notify operators of any deviations, ensuring that machines adhere to both safety and environmental guidelines.
Difficulty Scaling Operations
Challenge: Scaling operations often introduce new machines and processes, increasing complexity and challenging existing infrastructure.
Solution: With data integration and cloud connectivity, machine monitoring software enables companies to expand operations without compromising efficiency. Custom-built systems can be tailored to support scalability, allowing businesses to add new machines or expand across multiple locations seamlessly. These scalable solutions are invaluable for growing organizations, providing a unified view across all equipment and ensuring consistent performance.
Supporting Data-Driven Decision Making
Challenge: Businesses often lack sufficient data for informed decision-making, leading to reactive rather than proactive management.
Solution: Custom monitoring system software aggregates and analyzes data from various machines, offering insights that inform strategic decisions. By using data analytics, companies can make proactive adjustments to optimize production, plan for maintenance, and manage resources effectively. Leveraging machine learning within monitoring software adds another layer, transforming raw data into predictive insights that drive more accurate and timely business decisions.
Beat The Challenges with The Power of Custom Machine Monitoring Solution!
Connect With Us Now!
Applications of Machine Monitoring Software
Machine monitoring software is revolutionizing how industries operate by delivering real-time insights into equipment health, operational efficiency, and productivity. This custom-built software helps businesses reduce downtime, prevent unexpected failures, and maximize the utilization of assets across various sectors. Here’s a closer look at how machine monitoring solutions are applied in different fields:
Predictive Maintenance in Manufacturing
In manufacturing, unexpected equipment failures can cause costly downtimes and disrupt production schedules. The monitoring system collects and analyzes data from sensors installed on machinery to detect early signs of wear and potential issues. Leveraging IoT Development Services, sensors communicate in real-time, allowing maintenance teams to intervene before problems escalate, significantly reducing repair costs and downtime while extending equipment lifespan.
Quality Control in Production Lines
Consistent quality is essential in industries like automotive, food processing, and pharmaceuticals. Machine monitoring software ensures product consistency by tracking machine parameters such as speed, pressure, and temperature. Any deviation from set standards triggers alerts, allowing operators to make real-time adjustments. This capability supports stringent quality control, minimizes waste, and ensures that end products meet regulatory standards.
Energy Efficiency in Heavy Industries
Energy-intensive industries, such as chemical processing and metal production, face substantial costs if machinery operates inefficiently. An industrial machine monitoring system tracks energy consumption patterns and identifies machines that consume excessive power. Insights from this data help businesses optimize energy use, reduce costs, and contribute to sustainability goals by lowering the facility’s carbon footprint.
Asset Tracking and Utilization in Warehousing
Machine monitoring solutions enhance warehouse operations by providing data on asset usage, performance, and idle times. By tracking equipment like forklifts, conveyor belts, and automated storage systems, warehouses can ensure efficient asset utilization, reduce unnecessary wear and tear, and allocate resources more effectively. This application is particularly valuable in logistics and warehousing, where high throughput and operational efficiency are top priorities.
Downtime Reduction in Mining and Construction
In industries like mining and construction, machine uptime directly impacts project timelines and costs. Equipment monitoring system provides insights into equipment health and performance, enabling operators to address potential issues before they lead to downtime. Especially for machinery operating in remote or challenging environments, machine monitoring is essential, ensuring projects stay on schedule and reducing costly delays.
Remote Monitoring of Offshore and Remote Facilities
For oil and gas facilities, offshore wind farms, and other remote installations, machine monitoring systems provide continuous data access without requiring on-site personnel. This capability allows operators to monitor equipment status, receive alerts, and troubleshoot issues from a distance, saving time and resources. Remote monitoring reduces costly travel needs, making it invaluable in offshore and remote industries for maintaining operational continuity.
Read More: Discover how digital twin oil and gas technology is revolutionizing industry operations with advanced technology.
Fleet Management for Transportation and Logistics
Machine monitoring is an asset for transportation and logistics companies managing large vehicle fleets. By tracking vehicle health, fuel efficiency, and driver performance, companies can schedule preventive maintenance, reduce fuel costs, and improve driver safety. Custom-built machine monitoring software provides real-time insights, enabling proactive maintenance that reduces breakdowns on the road, thus supporting timely and reliable deliveries.
Steps to Develop a Custom Machine Monitoring Solution for Your Business
Developing a custom machine monitoring system involves a detailed, step-by-step approach tailored to meet specific business requirements. Here’s a breakdown of each step involved in creating a robust, scalable solution and how expert support can ensure every phase runs smoothly.
Identify Requirements and Objectives
Start by clearly defining your objectives, such as desired features, machine types to monitor, and key metrics. This stage involves understanding operational goals, potential challenges, and expected outcomes to design a targeted solution.
Our experts collaborate with your team to conduct a detailed analysis, identifying the most relevant features and functionalities for a tailored solution. This custom approach ensures the machine monitoring solutions we develop align precisely with your business needs.
Select the Right Technology Stack
Choosing suitable sensors, IoT devices, data storage options, and analytics platforms is crucial. This selection should support real-time data processing, ensure compatibility with existing systems, and offer scalability for future needs.
Our IoT consulting services provide insight into the best technology choices, ensuring that your system integrates seamlessly with current infrastructure. This strategic selection allows the system to scale as your business grows, meeting evolving demands efficiently.
Design System Architecture
Establish a blueprint detailing how components such as sensors, cloud storage, and user interfaces will communicate within the industrial machine monitoring system. A well-structured architecture ensures reliable data flow and effective system performance.
Our architects design a secure and robust framework that maximizes data accessibility and stability. We focus on developing a flexible architecture to support seamless integrations and consistent data flow, which is essential for machine monitoring software.
Integrate Data Analytics and Visualization Tools
Implement analytics tools to convert raw machine data into actionable insights. Visualization dashboards provide an accessible way to view and interpret performance metrics, helping operators make data-driven decisions.
Our team helps you choose and integrate advanced analytics and visualization tools, providing intuitive interfaces that simplify data access. With our support, your monitoring system software offers clear insights for faster, more effective decision-making.
Develop and Test Prototypes
Developing a prototype enables testing on select machines to validate the accuracy and functionality of the machine condition monitoring system. This phase helps ensure the solution meets performance expectations before full deployment.
Our developers rigorously test each feature to confirm system reliability and address any challenges. We collect feedback and make necessary adjustments, ensuring the final system functions smoothly and aligns with operational goals.
Deploy Solution and Conduct Training
After testing, deploy the full solution across relevant operations. This phase includes training users and support teams to effectively operate and maintain the monitoring system software, maximizing its functionality.
We offer comprehensive training and resources, ensuring your team understands the system fully and can leverage it effectively. Our team stays available to guide users, making the transition seamless and straightforward.
Provide Continuous Support and Optimization
Regular updates, feature enhancements, and continuous monitoring are vital for adapting the machine monitoring system to changing business needs. This step ensures ongoing optimization and maximizes long-term system value.
Our team offers consistent support, performing maintenance checks, updates, and optimizations. By staying responsive to your business’s evolving requirements, we help ensure the solution remains efficient, relevant, and reliable over time.
Need Expert Guidance to Build a Data-Driven Machine Monitoring Solution?
Fill Out the Form!
The Future of Machine Monitoring: Emerging Trends and Technologies
With the rapid evolution of technology, technology consulting services play a crucial role in guiding businesses through the integration of cutting-edge machine monitoring solutions. These services help companies harness advancements in predictive analytics, IoT, and real-time data processing to optimize operations. Here are the key trends shaping the future of machine monitoring:
AI-Driven Predictive Analytics
AI is enhancing predictive maintenance by analyzing real-time data to forecast potential equipment failures before they happen. With machine condition monitoring system capabilities, businesses can detect anomalies that might indicate breakdowns, reducing costly downtime and optimizing the lifespan of machinery. This enables a proactive approach to maintenance, allowing businesses to act before issues escalate, resulting in fewer interruptions and maximizing operational efficiency.
Edge Computing
Edge computing, by processing data closer to the source, reduces latency and bandwidth needs, allowing machine monitoring software to provide near-instantaneous updates. This trend supports faster data analysis, enabling real-time insights directly from the machine level. Ideal for time-sensitive environments, edge computing boosts response times and security, as sensitive data stays local, improving performance in industries that rely on speed and security.
Digital Twins
Digital twin technology allows businesses to create virtual replicas of machines or systems. This enables testing in a virtual environment, helping to fine-tune performance and anticipate maintenance needs, making machine monitoring system adoption easier and more efficient. Digital twins enhance operational efficiency by allowing businesses to simulate different operational scenarios without disrupting the physical asset, leading to better optimization and strategic decision-making.
Enhanced IoT Integration
With advancements in IoT, machine monitoring systems now support seamless communication across multiple devices. Enhanced equipment monitoring systems benefit from IoT’s interconnectedness, combining insights from various data points for comprehensive machine health insights. This connectivity fosters unified data flow, which empowers operators to monitor complex environments effortlessly, making informed decisions that elevate productivity and reduce costs.
Cybersecurity for Industrial IoT
As IoT expands, so do security risks, especially in industrial settings. Machine monitoring systems are now adopting stronger cybersecurity protocols to protect machine data against breaches and unauthorized access. Advanced security practices safeguard sensitive machine data, ensuring businesses comply with regulations and maintain trust in the reliability of monitoring system software.
Remote Monitoring and Control
Remote capabilities allow operators to oversee machine performance from any location, a feature essential for industries with offshore or remote operations. Industrial machine monitoring systems facilitate real-time oversight, alerting teams to potential issues before they become critical. Remote monitoring enables continuous management of assets, reducing the need for physical presence and ensuring that machines remain operational, especially in isolated or hard-to-access locations.
Real-Time Data Integration with ERP Systems
Integrating machine monitoring data with ERP systems boosts operational insights, supporting enterprise-wide visibility and decision-making. This integration helps businesses make informed, data-driven choices by aligning machine monitoring solutions with ERP data, leading to optimized resource allocation, improved maintenance scheduling, and better supply chain management.
How Can Matellio Help with Machine Monitoring Solutions?
Implementing a robust machine monitoring solution is essential for businesses that prioritize operational efficiency, predictive maintenance, and data-driven decision-making. At Matellio, we specialize in custom-built machine monitoring solutions tailored to your industry needs, enabling real-time insights, optimized resource management, and enhanced equipment performance.
Our Approach
- With extensive experience in developing machine monitoring software, we deliver fully integrated solutions that work seamlessly with your existing systems, offering centralized access to real-time data and actionable insights.
- Our solutions aggregate data from IoT sensors, controllers, and ERP systems into a unified platform, providing a complete, real-time overview of machinery health and operational metrics.
- Data security is integral to our solutions. We implement secure access controls, encryption, and regular system audits to protect operational data, ensuring compliance with industry standards.
- We are a trusted software development company; we specialize in machine monitoring solutions tailored to your unique industry needs, delivering real-time insights, optimized resource management, and enhanced equipment performance.
- Our team works closely with you to understand your specific requirements, ensuring your machine monitoring system is custom-tailored to align with your business goals.
- Each machine condition monitoring system is designed to meet your operational needs, from predictive maintenance to quality control.
- From initial design through deployment and beyond, we provide end-to-end support to ensure smooth operation and ongoing system optimization.
Ready to enhance your operations with a data-driven machine monitoring solution? Fill out the form to connect with us!
FAQs:
Q1. How do you ensure the security of our machine monitoring solution?
We incorporate advanced security features like encryption, secure user access, and compliance checks throughout the development process. Regular audits and industry-standard security practices protect your data from potential threats.
Q2. Can you integrate machine monitoring with our existing systems?
Absolutely. We excel at integrating monitoring solutions with various systems, including ERP, asset management, and inventory systems, ensuring seamless data flow and improved operational efficiency across departments.
Q3. What is the typical timeline for implementing a machine monitoring solution?
The timeline depends on factors such as data complexity, integration requirements, and specific customizations. We collaborate with you to define a clear project timeline that ensures timely and efficient implementation.
Q4. What kind of post-launch support do you offer for machine monitoring solutions?
We offer ongoing support, including system optimization, updates, and user training. Our team monitors the solution post-launch to ensure smooth operation and assists with additional insights as your data requirements evolve.
Q5. What are the projected costs for developing a machine monitoring solution?
Costs vary based on factors like data sources, integration needs, and compliance requirements. We provide transparent pricing to deliver a high-quality solution within your budget, meeting your operational goals effectively.