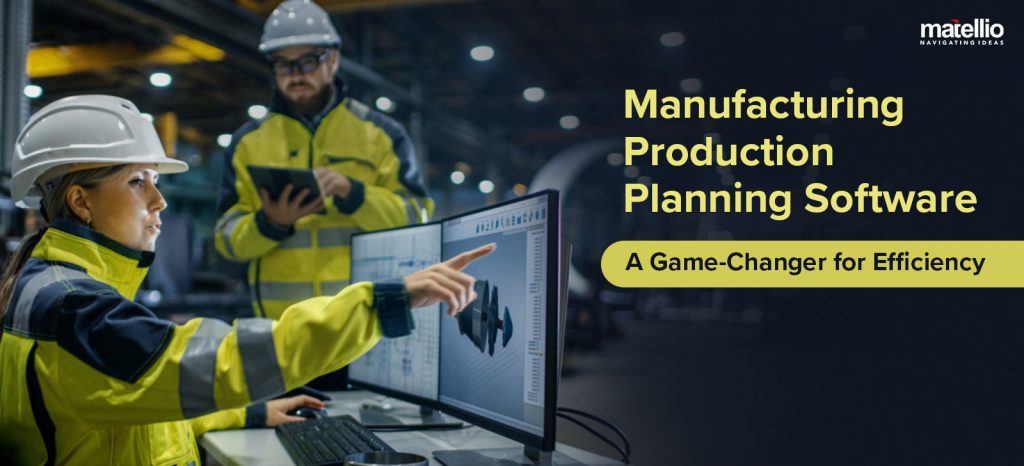
In today’s competitive manufacturing environment, efficient production planning is essential to ensure operational effectiveness, reduce costs, and meet customer demands. As production volumes grow, and supply chains become increasingly complex, traditional planning methods fall short. Digital solutions, such as manufacturing production planning software, offer a modern approach that enables manufacturers to optimize resources, cut waste, and enhance production flow.
By embracing advanced technologies, manufacturers can streamline operations, improve visibility, and make more informed decisions. This software has become an indispensable tool for manufacturers of all sizes, allowing them to manage everything from scheduling to inventory control and resource allocation with accuracy.
What is Manufacturing Production Planning Software?
Manufacturing production planning software is designed to help manufacturers plan, manage, and optimize their production processes. Unlike traditional methods that rely heavily on manual scheduling and spreadsheets, these platforms offer real-time insights, advanced analytics, and automated scheduling tools that cater to the unique needs of manufacturing environments
This software addresses the growing challenges manufacturers face, such as fluctuating demand, supply chain disruptions, and capacity constraints. It enables manufacturers to adapt quickly to changing conditions, ensuring that production remains efficient and cost-effective. The flexibility of these platforms makes them suitable for a variety of industries, allowing businesses to track and manage production workflows, resources, and materials seamlessly.
Difference Between Traditional Planning Methods and Digital Manufacturing Platforms
Traditional Planning Methods: These often involve manual processes such as creating schedules on spreadsheets, coordinating resources through emails, and reacting to changes after they occur. They lack real-time data integration and automated scheduling, which can lead to inefficiencies and delays in production.
Digital Manufacturing Planning Software: This platform offers real-time data access, automated scheduling, predictive analytics, and resource allocation tools. It optimizes the entire production workflow by ensuring real-time visibility into operations, automating manual tasks, and helping manufacturers proactively manage production changes.
How Production Planning Tools are Evolving with the Rise of Digital Manufacturing
With the rise of Industry 4.0 and smart manufacturing technologies, production planning tools have evolved significantly. Traditional methods have been replaced by highly sophisticated software that incorporates IoT (Internet of Things), AI, and predictive analytics to improve efficiency. As global competition intensifies and customer expectations grow, manufacturers are increasingly relying on digital tools to provide visibility across the production process, from raw material procurement to finished goods.
By leveraging advanced manufacturing production planning software, manufacturers can better predict demand, manage resources more efficiently, and respond to disruptions in real-time. These tools allow businesses to balance production loads, optimize capacity, and ensure on-time delivery, ultimately driving profitability.
How Does Manufacturing Production Planning Software Work?
Data Collection
Production planning software captures data from multiple sources, such as machines, inventory systems, and customer orders. This data is used to create real-time insights into production status, material availability, and resource utilization.
Production Scheduling
One of the core features of production planning software is its ability to create dynamic schedules based on real-time data. The software automatically allocates resources, schedules production runs and adjusts timelines to meet changing demands.
Resource Optimization
With digital solutions, manufacturers can optimize the use of resources, such as labor, machinery, and materials. By analyzing historical data and forecasting future needs, the software ensures that resources are allocated efficiently, reducing downtime and improving productivity
Collaboration Tools
Production planning software provides collaboration tools that allow teams across departments to work together seamlessly. Whether it’s procurement, operations, or sales, all stakeholders have access to real-time data and can collaborate to make informed decisions.
Automation
Automation plays a key role in modern production planning. It reduces manual data entry, automates the scheduling process, and provides real-time updates on production status, which minimizes the potential for human error.
Reporting and Analytics
The software generates comprehensive reports and analytics, offering insights into production performance, bottlenecks, and areas for improvement. These insights help manufacturers make data-driven decisions to optimize operations and improve overall efficiency.
Key Features of Manufacturing Production Planning Software
Manufacturing production planning software provides a comprehensive set of core features to streamline workflows, optimize resource allocation, and ensure timely delivery. Additionally, next-gen functionalities are emerging, pushing the boundaries of efficiency and innovation in production planning. By leveraging digital transformation services, manufacturers can seamlessly integrate both core and advanced features, future-proofing their operations for greater agility and performance. Below is a table highlighting these essential and next-gen capabilities.
Core Features | Next-Gen Features |
Work Order Management | Robotic Process Automation (RPA) |
Bill of Materials (BOM) Management | IoT Integration for Smart Manufacturing |
Capacity Planning | Cloud Integration and Scalability |
Production Scheduling and Planning | Automated Workflow Optimization |
Inventory and Resource Management | Predictive Maintenance |
Real-Time Production Monitoring | AI-Powered Demand Forecasting |
Benefits of Using Manufacturing Production Planning Software
The implementation of manufacturing production planning software offers numerous transformative benefits that can streamline operations, enhance decision-making, and improve overall production efficiency. These advantages are vital for manufacturers aiming to stay competitive in a rapidly evolving market while optimizing their resources and processes.
Increased Efficiency
One of the primary benefits of using production planning software is the automation of time-consuming tasks such as production scheduling, resource allocation, and inventory management. By automating these routine processes, manufacturers can significantly reduce manual effort and minimize human error. This frees up resources and personnel to focus on critical aspects such as quality control, product innovation, and customer fulfillment. As a result, manufacturers can increase production speed while maintaining high standards.
Improved Accuracy
Production planning software for manufacturing provides real-time data to track the status of production, material availability, and machine usage. With access to accurate data, manufacturers can ensure that the right resources—whether raw materials or manpower—are available at the right time. This not only reduces the chances of production delays caused by shortages but also ensures that production schedules are met without unnecessary downtime or errors, improving overall accuracy and consistency in manufacturing workflows.
Real-Time Collaboration
In today’s global manufacturing environment, production often involves multiple teams across different locations. Manufacturing production planning software facilitates real-time collaboration by providing shared access to production schedules, inventory levels, and other key data. This allows departments—whether in-house or remote—to stay aligned on project goals, make faster decisions, and coordinate efforts more effectively. This improved communication helps eliminate bottlenecks, accelerates decision-making, and increases overall operational transparency.
Enhanced Security
Security is a critical concern in manufacturing, especially when it comes to protecting sensitive production data, intellectual property, and proprietary information. Production planning software includes advanced security features such as data encryption, multi-factor authentication, and secure access controls, which safeguard against unauthorized access and data breaches. By securing valuable information, manufacturers can mitigate risks related to cyberattacks and data theft, ensuring that their operations remain secure and compliant with data protection regulations.
Compliance
Manufacturing processes are often subject to stringent industry regulations and standards. Manufacturing production planning software automates the tracking and documentation of production processes, ensuring compliance with industry-specific regulations such as ISO certifications, FDA standards, and other legal requirements. By maintaining detailed records and audit trails of every production step, businesses can demonstrate regulatory compliance and reduce the risk of penalties or legal issues.
Cost Savings
By automating production planning processes, manufacturers can achieve significant cost savings. Automation reduces the need for a large manual workforce to handle repetitive tasks like scheduling and material tracking. Additionally, by optimizing resource allocation and minimizing production delays, businesses can avoid costly bottlenecks and excess inventory. The reduced risk of human error also decreases the likelihood of costly mistakes, ultimately improving profitability.
Scalability
As businesses grow, their production demands increase. Cloud-based production planning software is designed to scale your manufacturing operations, ensuring that the system can handle increased production volumes, additional resources, and expanded manufacturing facilities without a drop in performance. This scalability allows businesses to grow without the need for costly system overhauls or hardware upgrades, enabling manufacturers to adapt seamlessly to market demand or new opportunities.
Read More: If you’re interested in learning more about how manufacturing analytics software development can benefit your production processes, feel free to read our in-depth blog on the topic.
Use Cases of Manufacturing Production Planning Software
Manufacturing production planning software plays a pivotal role in streamlining operations, optimizing resources, and enhancing decision-making across various stages of the production lifecycle. Below are some key use cases where this software proves invaluable in addressing the unique challenges faced by manufacturers.
Optimizing Resource Allocation
Manufacturers often deal with limited resources such as raw materials, workforce, and machinery. Manufacturing production planning software enables businesses to allocate these resources efficiently by analyzing demand forecasts, available stock, and production capacity. This ensures that all resources are used optimally, reducing waste and avoiding overproduction.
Just-in-Time (JIT) Manufacturing
In industries focused on minimizing inventory costs, the Just-in-Time (JIT) manufacturing approach is essential. Production planning software for manufacturing automates the scheduling and material procurement processes, ensuring that parts and materials arrive exactly when needed. This minimizes storage costs and reduces the risk of excess inventory.
Read More: Discover how Smart Manufacturing Inventory Systems optimize operations, reduce waste, and enhance efficiency in modern industrial environments.
Real-Time Production Monitoring
For manufacturers looking to maintain high levels of quality and efficiency, real-time monitoring is critical. The production planning software provides real-time visibility into the production floor, enabling managers to track production progress, identify bottlenecks, and adjust on the fly to ensure smooth operations.
Capacity Planning
Manufacturers need to plan for varying levels of demand. The Production Scheduling Software allows businesses to forecast future demand and align production schedules accordingly. This ensures that the manufacturing process can scale up or down based on customer orders, preventing underutilization or overburdening of resources.
Multi-Location Coordination
For manufacturers with multiple production sites, coordinating efforts across locations can be a challenge. The production planning system centralizes production data, offering real-time insights across all facilities. This ensures seamless coordination and helps to standardize production practices, regardless of location.
Order Fulfillment and Scheduling
Production planning in manufacturing streamlines the order fulfillment process by automating production scheduling based on customer demand and lead times. It ensures that production schedules are aligned with delivery deadlines, reducing the risk of delays and improving customer satisfaction.
Predictive Maintenance
Integrating predictive maintenance features, the software allows manufacturers to predict when equipment is likely to fail or require maintenance. This reduces unexpected downtime and helps in scheduling maintenance at optimal times, ensuring continuous production without interruptions. Incorporating AI integration services further enhances this capability.
Regulatory Compliance
Many industries, such as automotive and pharmaceuticals, require strict compliance with regulatory standards. Manufacturing process planning software ensures that all production processes are documented, providing traceability and ensuring compliance with industry regulations.
Custom Manufacturing
For manufacturers dealing with customized products, the manufacturing production planner helps tailor production schedules and material requirements based on specific customer orders. It adjusts workflows according to custom specifications, ensuring on-time delivery of personalized products without sacrificing efficiency.
Lean Manufacturing
Manufacturers adopting lean methodologies can benefit from production planning in manufacturing industry by optimizing workflows, eliminating unnecessary steps, and reducing waste. The software provides insights into process inefficiencies, allowing businesses to continuously improve their production processes.
Steps for Manufacturing Production Planning Software Development
Developing manufacturing production planning software requires a structured and strategic approach to ensure that the final product meets your business needs and delivers value. Below are the essential steps to guide your software development process effectively:
1. Research and Define Your Requirements
- Begin by conducting thorough research to define your specific needs for manufacturing production planning software.
- Understand the current landscape of production planning solutions, industry standards, and technological advancements relevant to manufacturing operations.
- Analyze existing software in the market to identify key functionalities, strengths, and areas where improvement is needed, focusing on production scheduling, resource allocation, and workflow optimization.
- Collaborate with industry experts to gather insights on pain points and required features for efficient manufacturing process planning.
- Define clear objectives and project goals based on research, ensuring that the software meets your specific business needs and addresses the challenges faced by your production teams.
2. Select the Right Development Partner
- Choose a reputable custom manufacturing software development partner with a strong background in the manufacturing industry and experience with similar projects.
- Ensure the development team has expertise in areas like manufacturing workflows, production optimization, and resource planning.
- Look for a partner who offers a comprehensive range of services, including consulting, UI/UX design, and continuous post-deployment support.
- Check the partner’s track record of delivering successful production planning software for manufacturing, with case studies or references to confirm their expertise.
3. Define the Technology Stack
- Work with your development team to select the best-suited technology stack for your production planning system, considering scalability, integration, and security needs.
- Choose technologies that support real-time production data and seamless integration with existing systems (such as ERP and MES systems) and ensure reliable performance under the demands of large-scale manufacturing.
- Ensure that the chosen stack includes tools for data analytics, reporting, and optimization, enabling better decision-making for your production processes.
Here’s a general tech stack that can be customized based on your project requirements:
Category | Technology |
Frontend | React.js, Angular, Vue.js |
Backend | Node.js, Django, Flask |
Database | MySQL, PostgreSQL, MongoDB |
Server | Express.js, Django REST Framework, Flask RESTful |
User Interface | Material UI, Bootstrap, Ant Design |
API Documentation | Swagger, Postman |
Version Control | Git, SVN |
Hosting | AWS, Azure, Google Cloud Platform |
Authentication | JWT (JSON Web Tokens), OAuth2 |
Real-time Updates | Socket.IO, GraphQL Subscriptions |
Security | HTTPS, SSL/TLS, Encryption |
Testing Frameworks | Jest, Mocha, Jasmine |
Continuous Integration/Deployment | Jenkins, GitLab CI, Travis CI |
Monitoring | Prometheus, Grafana, ELK Stack (Elasticsearch, Logstash, Kibana) |
Containerization | Docker, Kubernetes |
Messaging Queue | RabbitMQ, Kafka |
4. Develop the Minimum Viable Product (MVP)
- Start with developing a Minimum Viable Product (MVP) to prioritize core features like production scheduling, inventory tracking, resource allocation, and reporting.
- Follow an Agile development methodology to break down the process into iterative sprints, allowing for feedback and refinement throughout development.
- Focus on delivering value quickly while keeping costs and development timelines manageable, ensuring the MVP addresses your most pressing manufacturing production planning needs.
- Ensure the MVP is scalable so additional functionalities and features can be added as needed.
5. Test and Deploy
- Perform comprehensive testing on the production planning software to guarantee it functions as expected across multiple devices and platforms.
- Employ both manual and automated testing methods to identify any potential bugs or issues, ensuring the software’s reliability and user-friendliness.
- Once testing is completed, deploy the software on a secure and scalable infrastructure, ensuring that it complies with data security standards and meets the industry regulations for manufacturing operations.
- Post-deployment, monitor the system’s performance and gather feedback from users to make necessary improvements and updates for enhanced functionality.
Empower Your Manufacturing Team with Custom Advanced Production Planning Software.
Connect With Us Now!
Challenges in Manufacturing Production Planning Software Development
Developing manufacturing production planning software presents several challenges, including managing complex production workflows and ensuring smooth integration with existing legacy systems. As manufacturers modernize, it becomes essential to incorporate advanced features while maintaining operational efficiency, security, and scalability. Addressing these challenges requires a strategic approach to implement systems that are agile, efficient, and built to support future growth.
Handling Complex Production Workflows
Challenge: Manufacturing environments often involve complex production workflows that must be managed across multiple teams, machinery, and production stages. Ensuring the software can handle these complexities in real time is critical for minimizing production delays and errors.
Solution: A robust, customizable manufacturing production planning software allows manufacturers to map and automate complex workflows while providing real-time visibility into every stage of production. The software should be flexible enough to adapt to different production models, such as just-in-time (JIT) or lean manufacturing.
Data Security and Privacy
Challenge: Protecting sensitive production data, intellectual property, and operational plans is critical. Unauthorized access or data breaches can lead to significant financial and reputational damage.
Solution: Implementing advanced security features like encryption, access controls, and secure cloud storage ensures that production data remains secure. Compliance with global data protection regulations, such as GDPR or industry-specific standards, must also be integrated into the production planning software for manufacturing systems to ensure full security.
Inventory and Resource Optimization
Challenge: Efficiently managing inventory and resources is a key challenge for production planning. Over-ordering or stockouts can lead to production delays or excess costs, making precise planning essential.
Solution: Production Scheduling Software should include real-time inventory tracking and resource optimization features. These tools can forecast demand, automate reordering, and ensure that production runs smoothly without delays caused by resource shortages.
Integrating with Legacy Systems
Challenge: Many manufacturers rely on legacy ERP, CRM, or MES systems that may not be fully compatible with new production planning software, leading to integration challenges.
Solution: Developing APIs and custom integration solutions allows the new production planning system to seamlessly connect with existing systems. This ensures data flow across the entire production cycle, from raw materials procurement to final product delivery.
Ensuring Multi-Location Coordination
Challenge: For manufacturers operating across multiple facilities or locations, coordinating production efforts and ensuring resource availability at each site can be a significant challenge.
Solution: Cloud-based manufacturing process planning software enables centralized control and visibility across all manufacturing locations. By providing real-time data on production status, inventory levels, and resource allocation, manufacturers can ensure smooth coordination and avoid bottlenecks or delays.
Demand Forecasting and Flexibility
Challenge: Unpredictable market demand or supply chain disruptions can affect production schedules, causing delays or inefficiencies.
Solution: AI-powered demand forecasting tools can predict market trends, helping manufacturers adjust production plans accordingly. Production planning software with real-time data analysis and dynamic scheduling capabilities ensures manufacturers can respond quickly to changes in demand without affecting production timelines.
Managing Production Downtime
Challenge: Unplanned equipment downtime or maintenance can severely disrupt production schedules, leading to delays and increased costs.
Solution: By integrating predictive maintenance tools into the manufacturing production planning software, manufacturers can monitor equipment health and schedule maintenance proactively, reducing unplanned downtime. Real-time production monitoring also helps detect issues before they escalate, ensuring minimal impact on production schedules.
Ready to Optimize Your Manufacturing Process and Overcome Planning Challenges?
Contact Us Today!
Future Trends in Manufacturing Production Planning Software
As technology rapidly advances, manufacturing production planning software must adapt to incorporate emerging innovations that enhance efficiency, scalability, and decision-making. Below are the key trends shaping the future of production planning:
AI-Powered Demand Forecasting
Artificial intelligence (AI) is revolutionizing demand forecasting by providing manufacturers with the tools to predict fluctuations in demand more accurately. AI-driven algorithms analyze historical data, market trends, and external factors such as economic conditions or seasonality. This predictive capability allows manufacturers to optimize their production schedules in advance, reducing overproduction or underproduction. By incorporating AI into production planning, manufacturers can make smarter decisions that align production with real-time market demands, improving overall supply chain efficiency.
IoT Integration
The Internet of Things (IoT) is transforming manufacturing by enabling real-time data collection from connected devices across the production floor. IoT sensors and devices monitor everything from machine performance to energy usage, providing invaluable insights into production operations.
With production planning software for manufacturing integrated with IoT, manufacturers can instantly adjust processes based on real-time data, optimizing production workflows, reducing waste, and preventing potential machine failures before they impact the production schedule. IoT-driven data also enables predictive analytics, improving operational efficiency by minimizing downtime and enhancing decision-making.
Cloud-Based Solutions
As manufacturers increasingly seek flexible, scalable solutions, cloud-based production planning software is becoming the go-to choice. Cloud-native solutions offer the ability to dynamically scale production planning efforts in line with business growth without the need for costly infrastructure upgrades. Moreover, cloud-based platforms facilitate real-time collaboration between teams across different locations, streamlining workflows and improving coordination.
By integrating cloud integration services, manufacturers can seamlessly connect their production planning software with existing enterprise systems such as ERP, CRM, and MES platforms, enabling a unified and efficient ecosystem that enhances operational agility and data accessibility.
Predictive Maintenance
Predictive maintenance is another emerging trend that will play a crucial role in future production planning. By using advanced sensors, IoT devices, and AI algorithms, manufacturers can monitor the health and performance of their machinery in real-time. This real-time data helps identify potential issues before they result in equipment failure, allowing for proactive maintenance scheduling.
Integrating predictive maintenance into production scheduling software minimizes unplanned downtime, extends the lifespan of machinery, and ensures that production schedules are not interrupted by unexpected breakdowns. This approach not only saves costs but also improves overall production reliability and efficiency.
Consult with Our Experts to Explore How Manufacturing Production Planning Software Can Streamline Your Operations
Schedule a Consultation Now!
How Can Matellio Help in Manufacturing Production Planning Software Development?
The development of manufacturing production planning software requires in-depth expertise, meticulous planning, and an understanding of industry-specific challenges. At Matellio, we offer enterprise software development services and end-to-end solutions tailored to optimize your production processes, ensuring efficiency and business growth.
Our Approach:
With our extensive experience in software development, we deliver customized production planning solutions designed to meet your business’s specific needs. Whether you need advanced scheduling, real-time tracking, or seamless integration with third-party systems, our team is equipped to provide the perfect solution.
Our team ensures the software integrates smoothly with your existing tools, including ERP systems, MES systems, and supply chain management software. This seamless integration allows for real-time data synchronization and automated workflows, improving operational efficiency and decision-making.
By utilizing technology consulting services, we guide your business in incorporating cutting-edge technologies, such as IoT and AI, to enhance production planning, improve predictive maintenance, and optimize resource allocation. Our tailored solutions help you gain a competitive edge and drive productivity.
So, whether you’re looking for a comprehensive development plan, insights into project timelines and costs, or expert consultation to refine your software strategy, our team is here to assist. Reach out by filling out the form, and let’s get started on optimizing your production planning.
FAQ’s
Q1. manufacturing production planning software
We prioritize the security of your business data throughout the development of manufacturing production planning software. Our approach includes implementing advanced encryption protocols, secure access controls, and conducting regular security audits to ensure your production data remains safe from unauthorized access or breaches.
Q2.Are you familiar with industry standards, and will the software comply with these regulations?
Yes, we are well-versed in industry-specific regulations and compliance standards. Our team ensures that the production planning software adheres to all relevant manufacturing standards and regulatory requirements, giving you peace of mind as your production processes scale.
Q3. What is the estimated timeline for developing and deploying the software?
The timeline for developing and deploying manufacturing production planning software varies depending on the scope and complexity of your project. Once the requirements are outlined, we work closely with you to set a timeline that meets your business goals while ensuring timely delivery of the software.
Q4.What post-launch support and maintenance services do you provide?
We offer full post-launch support and maintenance services, including bug fixes, feature updates, performance optimization, and technical support. Our maintenance plans are tailored to meet your specific production needs, ensuring the software continues to run smoothly and efficiently over time.
Q5. What are the estimated costs for developing this software?
The development costs for manufacturing production planning software depend on several factors, such as the project's scope, required features, and technical complexities. At Matellio, we provide transparent pricing and ensure that the final solution meets both your budget and operational requirements.