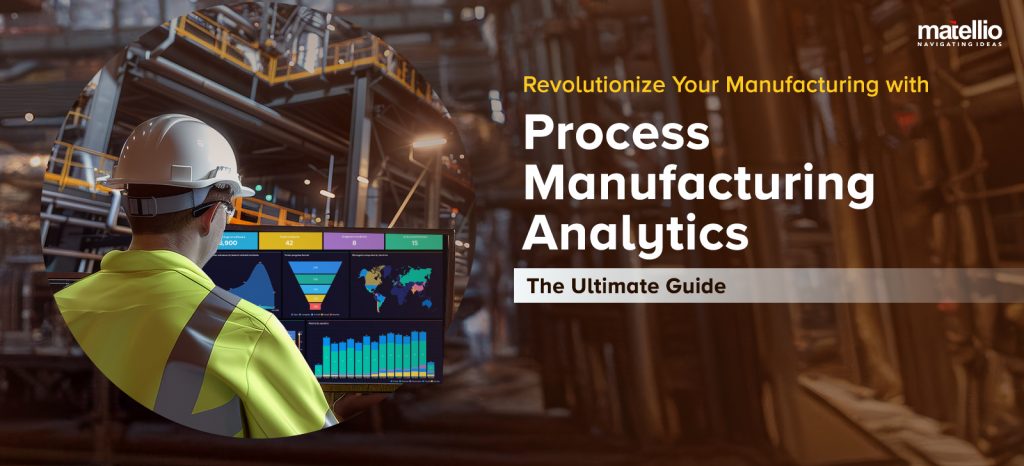
Are you ready to take your manufacturing business to the next level? In today’s rapidly evolving industrial landscape, staying ahead of the competition requires more than just efficient production lines and quality products. It demands a deep understanding of your processes, real-time insights, and data-driven decision-making. This is where process manufacturing analytics comes into play.
As a manufacturing business owner, you’re constantly seeking ways to optimize operations, reduce costs, and improve product quality. Process manufacturing analytics is the game-changer you’ve been waiting for. In this comprehensive guide, we’ll explore what process manufacturing analytics is, why it’s crucial for your business, and how you can implement it to drive transformative results.
What is Process Manufacturing Analytics?
Process manufacturing analytics is the application of advanced data analysis techniques to the continuous flow production processes typical in industries like pharmaceuticals, chemicals, food and beverage, and oil and gas. It involves collecting, analyzing, and interpreting data from various stages of the manufacturing process to improve efficiency, quality, and decision-making.
Unlike discrete manufacturing, where products are assembled from individual parts, process manufacturing involves transforming raw materials through chemical reactions, heating, cooling, and other processes. This continuous nature of production makes process manufacturing analytics particularly powerful and essential.
Process manufacturing analytics goes beyond traditional data analysis by incorporating real-time data streams, predictive modeling, and custom machine learning solutions. It enables you to:
- Monitor production processes in real-time
- Predict and prevent equipment failures
- Optimize resource utilization
- Ensure consistent product quality
- Streamline supply chain operations
- Enhance regulatory compliance
By leveraging process manufacturing analytics, you can gain a competitive edge in your industry, reduce operational costs, and drive innovation in your manufacturing processes.
Why Process Manufacturing Analytics Matters Now More Than Ever
In today’s hyper-competitive manufacturing landscape, leveraging process manufacturing analytics isn’t just an option – it’s a necessity.
As per trusted sources, the global manufacturing analytics market is expected to grow to $13.2 billion by 2026 at a Compound Annual Growth Rate (CAGR) of 14.3% during the forecast period. This growth is driven by the increasing need for process optimization and the adoption of advanced technologies like AI/ML and IoT development services in manufacturing.
And that’s not all!
Well, these stats clearly state the necessity of adopting process manufacturing analytics for your business. But what exact benefits can you obtain with analytics in manufacturing? Let’s explore!
Increasing Complexity
Manufacturing processes are becoming more intricate, with numerous variables affecting product quality and efficiency. Process manufacturing analytics helps you make sense of this complexity, enabling you to identify patterns and relationships that would be impossible to detect manually.
Rising Costs
With raw material and energy costs on the rise, optimizing resource usage through analytics can significantly impact your bottom line. Process manufacturing analytics allows you to pinpoint areas of waste and inefficiency, helping you reduce costs without compromising quality.
Stringent Regulations
Industries like pharmaceuticals and food production face increasingly strict regulatory requirements. Analytics in manufacturing can help ensure compliance by providing real-time monitoring of critical process parameters and maintaining detailed audit trails.
Customer Expectations
Today’s customers demand consistent quality and faster delivery times. Process manufacturing analytics enables you to meet and exceed these expectations by ensuring product consistency, reducing lead times, and improving overall quality control.
Competitive Pressure
Your competitors are likely already investing in data analytics in manufacturing. Falling behind in this area could mean losing market share and profitability. By embracing process manufacturing analytics now, you can stay ahead of the curve and position your business for long-term success.
Data Explosion
The advances in Industrial IoT consulting and sensors have led to an explosion of data in manufacturing environments. Process manufacturing analytics provides the tools to harness this data and turn it into actionable insights.
Sustainability Concerns
With growing emphasis on sustainable manufacturing practices, process manufacturing analytics can help you optimize resource usage, reduce waste, and minimize your environmental footprint.
Supply Chain Disruptions
Recent global events have highlighted the need for resilient and agile supply chains. Analytics can help you better predict and respond to supply chain disruptions, ensuring business continuity.
By leveraging process manufacturing analytics, you’re not just keeping pace with industry trends – you’re positioning your business to thrive in an increasingly data-driven world. The insights gained from analytics in manufacturing can drive innovation, improve decision-making, and ultimately lead to a more profitable and sustainable business.
Let’s Get Started with Your Process Manufacturing Analytics Project with a Free 30-minute Consultation!
How Companies Are Transforming with Process Manufacturing Analytics – Client Success Story
Leading manufacturers across industries are already reaping the benefits of process manufacturing analytics. Let’s explore a real-world example to illustrate the transformative power of this technology:
In the realm of process manufacturing, where efficiency and precision are paramount, the ability to derive meaningful insights from data is crucial. Hypertherm, a global leader in industrial cutting systems, faced a significant challenge in this area. The traditional methods they used to analyze data from their cutting cartridges were not only time-consuming but also limited their capacity to make timely and informed decisions, which are essential to maintain operational efficiency and reduce downtime.
The Challenge
Hypertherm’s process manufacturing environment was hindered by labor-intensive manual data management processes. These methods made it difficult to optimize operations and gain real-time insights, crucial for predicting cartridge lifespan and enhancing operator performance. The inefficiency in data handling posed risks of unplanned downtime and increased operational costs, impacting overall productivity.
The Solution
Recognizing the need for transformation, Matellio partnered with Hypertherm to develop a custom cartridge reader app tailored to their specific needs. This innovative application automated the data capture process, effectively eliminating the need for manual data entry. The app streamlined the collection and organization of data from the cartridges, converting raw data into structured, analyzable datasets.
But the solution didn’t stop at data capture. Leveraging advanced process manufacturing analytics, Matellio transformed these datasets into actionable insights. Through strategic consulting, we provided Hypertherm with a clear roadmap on how to utilize these insights effectively, enabling them to make data-driven decisions that enhanced their operations.
The Outcome
The integration of advanced analytics into Hypertherm’s process manufacturing resulted in several transformative benefits:
Predictive Maintenance
By accurately predicting cartridge lifespan, Hypertherm could proactively schedule maintenance activities, significantly reducing unexpected downtime and ensuring continuous production.
Operational Efficiency
With insights derived from real-time data, Hypertherm optimized both operator performance and machine usage, leading to substantial improvements in productivity and operational efficiency.
Strategic Decision-Making
The actionable insights gained through analytics empowered Hypertherm to make informed decisions, improving their overall operational workflow and supporting long-term strategic goals.
Conclusion
Hypertherm’s success story underscores the critical role that advanced analytics plays in process manufacturing. By converting raw data into meaningful insights, companies can not only enhance their operational efficiency and reduce downtime but also make strategic decisions that drive sustained success.
At Matellio, we specialize in custom software development for the manufacturing industry, utilizing cutting-edge technology to help manufacturers unlock the full potential of their data. This ensures they remain competitive in a rapidly evolving market.
Interested in discovering how process manufacturing analytics can revolutionize your operations? Contact us today to explore how we can help you achieve your business goals!
Also Read: Manufacturing Analytics Software Development – From Concept to Implementation
Key Areas You Can Revolutionize with Process Manufacturing Analytics
So, you have explored the benefits and a real-world example of how analytics in manufacturing proved to be a boom for a company. But what areas can you optimize with this robust manufacturing technology trend?
Well, process manufacturing analytics can drive improvements across virtually every aspect of your operations. Let’s dive into some key areas where you can expect to see significant benefits:
Quality Control and Assurance
Process manufacturing analytics enables real-time monitoring and control of product quality. By analyzing data from in-line sensors and quality checks, you can:
- Detect and correct quality issues before they become costly problems
- Ensure consistent product quality across batches
- Reduce waste and rework
- Implement statistical process control for continuous improvement
Predictive Maintenance
Leveraging machine learning algorithms and real-time data, predictive maintenance analytics can:
- Predict equipment failures before they occur
- Reduce unplanned downtime
- Optimize maintenance schedules
- Extend equipment lifespan
- Reduce maintenance costs
Supply Chain Optimization
Supply chain analytics in manufacturing can transform your operations by:
- Improving demand forecasting accuracy
- Optimizing inventory levels
- Enhancing supplier performance management
- Reducing lead times
- Improving overall supply chain resilience
Read More: Discover how Smart Manufacturing Inventory Systems optimize operations, reduce waste, and enhance efficiency in modern industrial environments.
Energy Efficiency
Process manufacturing analytics can significantly impact your energy consumption by:
- Analyzing energy usage patterns
- Identifying opportunities for reduction
- Optimizing process parameters for energy efficiency
- Monitoring and reducing carbon footprint
Product Development and Innovation
Analytics can accelerate your R&D processes by:
- Identifying optimal formulations and process parameters
- Predicting product performance based on process data
- Facilitating faster and more efficient scale-up from lab to production
- Enabling data-driven decision making in product development
Regulatory Compliance
In heavily regulated industries, process manufacturing analytics can:
- Ensure compliance with industry regulations
- Monitor and document critical process parameters
- Provide detailed audit trails
- Facilitate faster and more accurate reporting
Yield Optimization
By analyzing process manufacturing analytics data, you can maximize product yield by:
- Identifying and eliminating sources of waste and inefficiency
- Optimizing process parameters for maximum yield
- Reducing variability in production processes
- Implementing advanced process control strategies
Operational Efficiency
Real-time analytics for smart manufacturing systems can boost overall operational efficiency by:
- Providing visibility into production bottlenecks
- Optimizing production scheduling
- Improving resource allocation
- Reducing cycle times
Customer Satisfaction
By leveraging process manufacturing analytics, you can enhance customer satisfaction through:
- Improved product quality and consistency
- Faster order fulfillment
- Enhanced ability to meet custom specifications
- Proactive quality assurance
Sustainability
Process manufacturing analytics can support your sustainability goals by:
- Reducing waste and emissions
- Optimizing resource utilization
- Facilitating the development of more sustainable products
- Providing data for sustainability reporting
These improvements aren’t just theoretical – they’re being realized every day by manufacturers who have embraced process manufacturing analytics. By implementing analytics in these areas, you’re not just optimizing individual processes; you’re transforming your entire manufacturing operation into a more efficient, responsive, and competitive entity.
Want Expert Assistance to Identify the Best Use Case of Analytics in Manufacturing?
Fill Our Form
How to Implement Process Manufacturing Analytics in Your Business?
The successful implementation of process manufacturing analytics requires a strategic approach that transforms raw data into actionable insights, driving efficiency and innovation across your operations. Here’s a step-by-step guide to help you get started:
Evaluate Your Existing Data Ecosystem
Start by assessing your current data landscape to understand where you stand and identify areas for improvement.
- Map Out Data Sources: List all data collection points within your manufacturing processes, including machinery sensors, production logs, ERP systems, and manual records.
- Assess Data Integrity: Evaluate the quality and accuracy of your data. Identify inconsistencies, gaps, or redundancies that could affect your analytics efforts.
- Analyze IT Capabilities: Review your current IT infrastructure, ensuring you have the necessary storage, processing power, and networking capabilities to support advanced analytics.
- Identify Integration Challenges: Look for data silos that need to be integrated into a cohesive system for comprehensive analysis.
Understanding your current data environment is crucial for laying a solid foundation for analytics.
Set Clear Goals and Metrics
Establishing clear objectives is critical to guide your analytics implementation and ensure it delivers measurable business value.
- Define Key Business Objectives: Identify the specific challenges you want to address, such as improving yield, reducing downtime, or enhancing product quality.
- Set Quantifiable KPIs: Determine the key performance indicators (KPIs) that will measure the success of your analytics initiative, like “Increase OEE by 10%” or “Reduce scrap rate by 20%.”
- Align with Strategic Priorities: Ensure your analytics goals align with broader business objectives, such as entering new markets or achieving sustainability targets.
- Create a Roadmap: Develop a timeline with milestones to track progress and ensure the project stays on course.
Clear goals and KPIs will help you measure the impact of your analytics implementation.
Partner with a Technology Expert
Implementing process manufacturing analytics is complex and requires specialized expertise. Engaging a technology consulting services provider can significantly enhance your chances of success.
- Select an Experienced Partner: Choose a provider with proven experience in manufacturing analytics and deep industry knowledge.
- Look for Comprehensive Services: Ensure your partner offers end-to-end solutions, from strategy and planning to implementation and ongoing support.
- Check References: Ask for case studies and speak with past clients to understand the provider’s capabilities and success rates.
- Focus on Innovation: Partner with a company that leverages cutting-edge technologies, such as AI, machine learning, and IoT, to drive advanced analytics.
The right partner will guide you through the implementation process, helping you avoid pitfalls and achieve your goals.
Go Agile and Develop Your Custom Solution
The next step is to design and develop a custom process manufacturing analytics solution that aligns with your specific needs and goals. Embracing the Agile development methodology can be particularly beneficial here, as it allows for flexibility, rapid iterations, and continuous improvement throughout the development process.
- Collaborate with Stakeholders: Involve key stakeholders from various departments, including production, quality control, and IT, to ensure that the solution addresses all critical business needs. Their input will guide the development process and help prioritize features.
- Define User Stories and Requirements: Break down the project into manageable user stories that describe the desired functionalities from the end-user perspective. This helps keep the development process focused and aligned with user needs.
- Iterative Development: Ask your chosen custom manufacturing software development partner to develop the solution in small, iterative cycles (sprints), with each iteration building upon the previous one. This approach allows for regular feedback, enabling the team to make adjustments quickly and ensure the solution evolves in the right direction.
- Prototyping and Testing: Create prototypes and test them with end-users to gather feedback. This ensures that the final product is user-friendly and meets the intended objectives.
- Incorporate Advanced Technologies: Integrate cutting-edge technologies such as AI integration services, machine learning, and IoT. For example, machine learning algorithms can be used to predict equipment failures or optimize production schedules.
By adopting the Agile methodology, you ensure that your custom analytics solution is developed efficiently, with a focus on meeting the actual needs of your manufacturing operations.
Also Read: How Advanced Manufacturing Analytics Future-Proof Your Company
Test Your Solution and Deploy on the Cloud Platform
Once your custom process manufacturing analytics solution has been developed, it’s essential to thoroughly test it to ensure it functions as expected and delivers the desired results. After successful testing, deploying the solution on a cloud platform can offer scalability, flexibility, and real-time access to analytics.
- Comprehensive Testing: Conduct rigorous testing across multiple environments to identify and resolve any bugs or performance issues. This should include unit testing, integration testing, and user acceptance testing (UAT) to ensure the solution meets all requirements.
- Simulate Real-World Scenarios: Test the solution under conditions that closely mimic your actual manufacturing environment. This helps to validate that the solution can handle real-world data volumes, processing speeds, and potential challenges.
- Optimize for Performance: Fine-tune the solution to optimize performance, ensuring that it can process data efficiently and deliver insights in real-time. This may involve refining algorithms, optimizing data processing workflows, or adjusting hardware configurations.
- Deploy on a Cloud Platform: Choose a cloud platform that best suits your business needs, such as AWS, Microsoft Azure, or Google Cloud. Deploying on the cloud offers numerous advantages, including scalability, cost-effectiveness, and ease of access. It also supports seamless integration with other cloud-based tools and services.
- Monitor and Manage: After deployment, continuously monitor the solution’s performance to ensure it operates smoothly. Use cloud management tools to track usage, performance metrics, and system health. This allows for quick identification and resolution of any issues.
Deploying your analytics solution on the cloud ensures that your manufacturing operations can scale efficiently as your business grows, while also providing the flexibility to adapt to changing needs. Hence, always opt for cloud integration services!
Train Your Team and Embed Analytics into Your Culture
For your process manufacturing analytics implementation to be successful, it’s vital that your team understands and embraces these new tools.
- Provide Tailored Training: Offer comprehensive training programs that cover the technical aspects of analytics tools and their strategic applications.
- Promote Data Literacy: Encourage employees at all levels to understand and utilize data in their daily roles, fostering a culture of data-driven decision-making.
- Encourage Cross-Department Collaboration: Facilitate collaboration between departments to ensure that data insights are shared and acted upon across the organization.
- Commit to Continuous Improvement: Regularly review and refine your analytics processes, incorporating feedback and evolving needs.
Embedding a data-driven culture will maximize the impact of your analytics investment and ensure long-term success.
By following these steps, you can effectively implement process manufacturing analytics, transforming your operations into a data-driven powerhouse. This strategic approach will help you unlock new efficiencies, improve product quality, and drive innovation, setting your business up for long-term success in the competitive manufacturing landscape.
Let’s Begin Your Project with a Free 30-minute Consultation!
Share Your Requirements
How Can Matellio Help You with Process Manufacturing Analytics Implementation?
At Matellio, we understand that the journey to successful process manufacturing analytics implementation can be complex and challenging. That’s why we offer a comprehensive suite of services designed to guide you through every step of the process, ensuring that your transition to data-driven manufacturing is smooth, efficient, and impactful. Here’s how we can help:
Expert Consultation and Strategy Development
Our process begins with an in-depth consultation to understand your unique business needs, challenges, and objectives. We work closely with your team to develop a tailored analytics strategy that aligns with your goals, ensuring that every aspect of your manufacturing operations is optimized for maximum efficiency and performance.
Custom Manufacturing Software Development
We specialize in custom manufacturing software development tailored to your business environment. Whether you need a real-time analytics dashboard, predictive maintenance tools, or advanced process control systems, our team has the expertise to deliver a solution that drives tangible results.
End-to-End Implementation Support
From initial setup to final deployment, we manage the entire implementation process. Our team ensures that your process manufacturing analytics solution is seamlessly integrated with your existing systems and fully operational on the cloud, providing you with real-time access to critical data insights.
Ongoing Training and Support
We don’t just deliver a solution and walk away. Matellio provides ongoing training to ensure that your team is fully equipped to leverage the power of analytics in their daily operations. Additionally, our support team is always available to assist with any issues or enhancements as your business needs evolve.
Driving Innovation with Advanced Technologies
Our commitment to innovation ensures that you stay ahead of the curve. By incorporating cutting-edge technologies like AI, machine learning, and Industrial IoT consulting, we help you unlock new levels of operational efficiency, product quality, and business growth.
In short, choosing Matellio as your partner for process manufacturing analytics implementation means you’re opting for expertise, innovation, and a commitment to your success. Our holistic approach ensures that every aspect of your operations is enhanced, leading to sustained improvements in efficiency, quality, and profitability.
Ready to transform your manufacturing operations? Contact us for a free 30-minute consultation, and let’s discuss how we can help you achieve your business goals.
FAQ’s
Q1. What are the key benefits of implementing process manufacturing analytics?
Process manufacturing analytics can significantly improve product quality, reduce operational costs, enhance regulatory compliance, optimize resource utilization, and increase overall operational efficiency by providing real-time insights and predictive analytics.
Q2. How long does it typically take to implement process manufacturing analytics?
The implementation timeline can vary depending on the complexity of your manufacturing processes and the specific goals of your analytics initiative. On average, a full implementation, including consultation, development, testing, and deployment, can take anywhere from a few months to over a year.
Q3. What kind of data is required for effective process manufacturing analytics?
Effective process manufacturing analytics typically requires data from various sources such as machinery sensors, production logs, ERP systems, supply chain data, and quality control systems. The data should be accurate, consistent, and real-time for the best results.
Q4. Can process manufacturing analytics help with regulatory compliance?
Yes, process manufacturing analytics can play a crucial role in ensuring regulatory compliance by providing real-time monitoring of critical process parameters, maintaining detailed audit trails, and facilitating faster, more accurate reporting.
Q5. How can Matellio support my business in implementing process manufacturing analytics?
Matellio offers end-to-end support for implementing process manufacturing analytics, including expert consultation, custom software development, cloud deployment, ongoing training, and support. We ensure that your solution is tailored to your specific needs and integrated seamlessly into your existing operations.