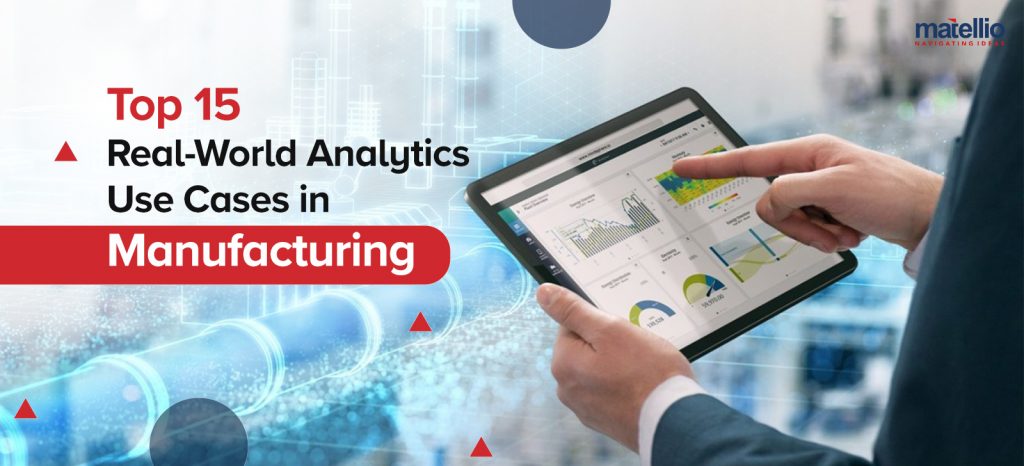
Are you tired of guessing and hoping your manufacturing operations run smoothly? Is guesswork dictating your manufacturing decisions? It’s time to harness the power of data. Analytics use cases in manufacturing are no longer a luxury; they’re a necessity for survival and growth.
In today’s time, leveraging analytics in manufacturing has become a necessity rather than a luxury. From optimizing production lines to predicting equipment failures, analytics use cases in manufacturing can revolutionize your business. But, how to find the most perfect one for your business? Moreover, how to implement analytics in manufacturing without much chaos? Well, that’s where a digital transformation services company like us comes into play!
In this blog, we have mentioned 15 real-world manufacturing analytics use cases that can transform your operations. Whether you’re looking to implement advanced manufacturing analytics or seeking to enhance your existing manufacturing operations analytics, this blog will provide you with valuable insights and practical applications. Let’s get started!
What is Manufacturing Analytics, and How Does It Work?
Picture this: You’re standing on your factory floor, surrounded by machines humming with activity. Now, imagine if you could peek inside each of these machines, understand their every whisper, and predict their needs before they even knew them. That’s the magic of manufacturing analytics use cases in a nutshell!
Manufacturing analytics software is your secret weapon in the world of production. It’s like having a super-smart assistant who never sleeps, constantly crunching numbers and spotting patterns in your data. This powerful tool takes the vast sea of information generated by your operations – from machine performance and quality control to supply chain logistics and customer feedback – and transforms it into actionable insights that can revolutionize your business.
But how does it work? Think of it as a three-step dance:
- Data Collection: Your machines, sensors, and systems are constantly generating data. Manufacturing analytics gathers this information from every nook and cranny of your operation.
- Data Processing: Advanced algorithms and artificial intelligence sift through this data, identifying patterns and correlations that the human eye might miss.
- Insight Generation: The processed data is transformed into easy-to-understand visualizations and reports, giving you the insights you need to make informed decisions.
Benefits of Adopting Analytics Use Cases in Manufacturing – What Will You Gain?
Now, you might be thinking, “This all sounds great, but what’s in it for me?” Well, buckle up, because the benefits of manufacturing analytics are about to blow your mind:
Crystal Ball for Your Machines
Predictive maintenance isn’t just a fancy term – it’s your ticket to saying goodbye to unexpected breakdowns and hello to optimized maintenance schedules. Imagine the money you’ll save!
Quality Control on Steroids
Spot defects faster than a speeding bullet and improve product quality. Your customers will think you’ve got superpowers!
Supply Chain Sorcery
Transform your supply chain from a guessing game into a well-oiled machine. No more stockouts or excess inventory gathering dust.
Efficiency Explosion
Optimize your processes to squeeze every ounce of productivity from your operations. It’s like finding extra hours in the day!
Innovation Acceleration
Use data to fuel your R&D and sprint ahead of the competition. Who knows? The next big thing in your industry might come from your analytics-driven insights.
Profitability Boost
When you combine all these benefits, what do you get? A healthier bottom line that’ll make your shareholders do a happy dance.
Exciting, isn’t it? Manufacturing analytics isn’t just about crunching numbers – it’s about unlocking the full potential of your operations and steering your business towards a future of unprecedented efficiency and innovation.
So, are you ready to dive into the world of manufacturing analytics and discover how it can transform your business? Let’s explore some real-world use cases that’ll make you wonder how you ever managed without it!
Where Can You Use Manufacturing Analytics – Top Analytics Use Cases in Manufacturing
Now that you understand the power of manufacturing analytics, you might be wondering, “Where exactly can I apply this in my operations?” The beauty of analytics use cases in manufacturing is that they touch every aspect of your business, from the shop floor to the boardroom.
In the following sections, we’ll explore 15 game-changing analytics use cases in manufacturing. These real-world applications will show you how data-driven insights can revolutionize your processes, boost efficiency, and drive innovation. Whether you’re looking to optimize maintenance, enhance quality control, or streamline your supply chain, there’s an analytics solution waiting to transform your manufacturing operations.
Predictive Maintenance
One of the most impactful analytics use cases in manufacturing is predictive maintenance. By leveraging advanced sensors, Internet of Things (IoT) devices, and machine learning algorithms, you can predict when equipment is likely to fail before it actually does. This proactive approach allows you to:
- Reduce unplanned downtime
- Extend the lifespan of your machinery
- Optimize maintenance schedules
- Cut repair costs
Imagine being able to address a potential issue in your production line before it causes a costly shutdown. That’s the power of predictive maintenance analytics in action.
Quality Control and Defect Detection
Analytics in manufacturing plays a crucial role in maintaining and improving product quality. By implementing real-time quality control systems powered by computer vision and machine learning, you can:
- Detect defects with higher accuracy than human inspectors
- Identify patterns in defects to address root causes
- Reduce waste and rework
- Ensure consistent product quality
This use of manufacturing analytics software not only improves your product quality but also boosts customer satisfaction and reduces costs associated with returns and warranties.
Supply Chain Optimization
In today’s global market, an efficient supply chain is critical for success. Analytics use cases in manufacturing extend to supply chain management, allowing you to:
- Optimize inventory levels
- Predict and mitigate supply chain disruptions
- Improve supplier performance
- Reduce lead times and transportation costs
By leveraging data from your entire supply network, you can make informed decisions that streamline operations and improve resilience against unforeseen challenges.
Demand Forecasting
Accurate demand forecasting is essential for efficient production planning and inventory management. Advanced manufacturing analytics, equipped with AI integration services, can help you:
- Predict future demand with greater accuracy
- Optimize production schedules
- Reduce excess inventory
- Improve cash flow
By analyzing historical sales data, market trends, and external factors like economic indicators or weather patterns, you can align your production with actual market demand, reducing waste and maximizing profitability.
Energy Management
As energy costs continue to rise and sustainability becomes increasingly important, analytics in the manufacturing sector can help you optimize your energy consumption. With real-time monitoring and analysis, you can:
- Identify energy-intensive processes and equipment
- Detect anomalies in energy usage
- Implement energy-saving measures
- Track and report on sustainability metrics
By leveraging analytics for energy management, you not only reduce costs but also improve your environmental footprint, meeting the growing demand for sustainable manufacturing practices.
Process Optimization
One of the most powerful analytics use cases in manufacturing is process optimization. By analyzing data from your production lines, you can:
- Identify bottlenecks and inefficiencies
- Optimize production parameters in real-time
- Reduce cycle times and increase throughput
- Minimize waste and resource consumption
Advanced manufacturing analytics tools can simulate different scenarios, allowing you to fine-tune your processes without disrupting actual production. This data-driven approach ensures you’re always operating at peak efficiency.
Inventory Optimization
Effective inventory management is crucial for maintaining smooth operations while minimizing costs. Analytics in manufacturing can help you:
- Predict optimal inventory levels based on demand forecasts
- Implement just-in-time inventory strategies
- Reduce carrying costs and stockouts
- Optimize warehouse space utilization
By leveraging analytics for inventory optimization, you can strike the perfect balance between having enough stock to meet demand and avoiding excess inventory that ties up capital.
Read More: Discover how retail inventory optimization solutions can streamline operations, reduce costs, and enhance your supply chain efficiency in the modern retail landscape.
Asset Performance Management
Maximizing the performance and lifespan of your assets is key to profitability. Manufacturing analytics use cases in asset management enable you to:
- Track asset utilization and performance metrics
- Identify underperforming assets
- Optimize asset maintenance and replacement schedules
- Improve overall equipment effectiveness (OEE)
With a data-driven approach to asset management, you can make informed decisions about when to repair, upgrade, or replace equipment, ensuring optimal performance and return on investment.
Product Development and Innovation
Analytics use cases in manufacturing extend beyond the production floor to the design lab. By analyzing product performance data, customer feedback, and market trends, you can:
- Identify opportunities for product improvements
- Accelerate the product development cycle
- Predict market acceptance of new features
- Optimize product designs for manufacturability
This data-driven approach to innovation helps you stay ahead of the competition by delivering products that meet evolving customer needs while maintaining efficient production processes.
Workforce Management and Safety
Your workforce is your most valuable asset, and analytics can help you optimize its performance and safety. Manufacturing operations analytics in this area allow you to:
- Optimize workforce scheduling based on production demands
- Identify skills gaps and training needs
- Monitor and improve workplace safety metrics
- Enhance employee productivity and satisfaction
By leveraging data to manage your workforce effectively, you can create a safer, more productive work environment while reducing labor costs and improving employee retention.
Logistics and Transportation Optimization
Efficient logistics and transportation are crucial for timely delivery and cost management. Analytics use cases in manufacturing extend to this area, helping you:
- Optimize route planning and vehicle loading
- Predict and mitigate transportation delays
- Reduce fuel consumption and emissions
- Improve on-time delivery performance
By applying advanced analytics to your logistics operations, you can reduce transportation costs while improving customer satisfaction through timely deliveries.
Customer Insights and Personalization
Even in manufacturing, understanding your customers is key to success. Analytics in the manufacturing sector can help you:
- Analyze customer buying patterns and preferences
- Predict future customer needs
- Personalize product offerings and services
- Improve customer retention and loyalty
By leveraging customer data, you can tailor your products and services to meet specific market needs, giving you a competitive edge in the industry.
Pricing Optimization
Pricing your products correctly is crucial for maximizing profitability. Manufacturing analytics software can assist you in:
- Analyzing market trends and competitor pricing
- Determining optimal price points for different markets
- Implementing dynamic pricing strategies
- Evaluating the impact of pricing changes on demand
Data-driven pricing strategies ensure you’re maximizing revenue while remaining competitive in the market.
Warranty Analysis
Warranty management is an often-overlooked area where analytics can provide significant benefits. By applying analytics to warranty data, you can:
- Identify recurring product issues
- Predict future warranty claims
- Optimize warranty reserves
- Improve product quality based on warranty insights
This use of analytics in manufacturing not only reduces warranty costs but also provides valuable feedback for product improvement.
Sustainability and Environmental Impact
As sustainability becomes increasingly important, analytics can help you monitor and improve your environmental performance. With advanced manufacturing analytics, you can:
- Track and reduce carbon emissions
- Optimize resource usage and waste management
- Ensure compliance with environmental regulations
- Develop and monitor sustainability initiatives
By leveraging data to drive sustainability efforts, you can reduce your environmental impact while also appealing to environmentally conscious customers and investors.
By implementing these analytics use cases in manufacturing, you’re not just solving today’s challenges – you’re positioning your business to swiftly tackle future demands. The power of data analytics in manufacturing is clear: it drives efficiency, innovation, and competitive advantage across the entire value chain.
Want to Implement Any of These Analytics Use Cases in Manufacturing?
Technology Trends Enhancing Analytics in Manufacturing
While analytics use cases in manufacturing are powerful on their own, combining them with other cutting-edge technologies can exponentially increase their value. Here are some key technology trends that, when integrated with analytics, can revolutionize your manufacturing processes:
Artificial Intelligence (AI) and Machine Learning
AI and machine learning algorithms can take your manufacturing analytics to the next level. By leveraging AI and ML, you can:
- Enhance predictive maintenance with more accurate failure predictions
- Improve quality control through advanced image recognition
- Optimize production scheduling with dynamic, self-adjusting algorithms
- Automate decision-making processes for faster response times
Internet of Things (IoT) and Industrial Internet of Things (IIoT)
IoT and IIoT devices are the backbone of data collection in modern manufacturing. By partnering with IIoT services providers, you can:
- Implement comprehensive sensor networks for real-time data collection
- Enable machine-to-machine communication for automated processes
- Create digital twins of your manufacturing operations for simulation and optimization
- Enhance asset tracking and management across your facility
Cloud Computing
Cloud platforms provide the scalability and processing power needed for advanced analytics. By leveraging cloud computing in manufacturing, you can:
- Store and process vast amounts of data from across your operations
- Enable real-time analytics and reporting accessible from anywhere
- Facilitate collaboration and data sharing across different departments and locations
- Reduce IT infrastructure costs and enhance data security
Edge Computing
Edge computing brings processing power closer to the data source, which is crucial for time-sensitive analytics. In manufacturing, edge computing can:
- Enable real-time decision making on the production floor
- Reduce latency for critical control systems
- Enhance data privacy and security by processing sensitive data locally
- Optimize bandwidth usage by filtering and processing data before sending it to the cloud
By integrating these technologies with your analytics use cases in manufacturing, you can create a powerful ecosystem that drives efficiency, quality, and innovation. The synergy between analytics and these advanced technologies opens up new possibilities for optimization and automation across your entire manufacturing operation.
At Matellio, we specialize in helping manufacturers leverage these cutting-edge technologies alongside analytics. Our comprehensive technology consulting services are designed to help you seamlessly incorporate these technologies into your existing operations, maximizing the value of your analytics initiatives. Below is one of our projects that shows our expertise in custom manufacturing software development and analytics services.
Also Read:- Manufacturing Analytics Software Development – From Concept to Implementation
Case Study: Revolutionizing Safety Inspections with Advanced Analytics – A Success Story with HESCO
HESCO, a leading provider of full-service, professional third-party inspections for heavy machinery, faced significant challenges with their offline and manual safety inspection process. Ensuring compliance with industry regulations and maintaining optimal equipment performance, HESCO conducted inspections directly at their clients’ locations or job sites. However, their outdated system led to error-prone data, cumbersome processes, and inefficiencies that hindered their operations.
The Challenge
Before partnering with us, HESCO’s safety inspection process was entirely manual, leading to several critical issues:
- Error-Prone Data: Manual data entry resulted in frequent errors, compromising the accuracy and reliability of inspection reports.
- Cumbersome Process: Customers had to call in with inspection details, which were then manually allocated by the admin. Inspectors visited sites, submitted handwritten inspection sheets, and awaited manual review for certification or deficiency reports.
- Inefficiencies: The manual process hindered progress tracking, historical data analysis, and document management. Manual invoicing led to missed or overdue invoices due to a lack of reminders.
HESCO needed a solution to automate their safety inspection process, streamline operations, and enhance efficiency. This is where we came in.
Our Solution
We partnered with HESCO to develop a state-of-the-art web-based platform, leveraging the power of ReactJS, NodeJS, and Postgres DB. Our technology-driven solution transformed their entire safety inspection process, offering numerous benefits to both the inspection team and their customers.
Key Features and Benefits
- Online Inspection Requests: Customers can now easily request inspections online, eliminating the need for phone calls and manual data entry.
- Efficient Task Management: Admins can efficiently manage inquiries, schedule appointments, and track tasks with automated reminders, ensuring no task is overlooked.
- Google Calendar Integration: Seamless integration with Google Calendar ensures punctuality and reduces scheduling conflicts, enhancing the reliability of inspection appointments.
- Customizable Inspection Sheets: Inspectors use customizable digital inspection sheets, streamlining the data collection process and reducing errors.
- Automated Invoice Generation: The platform automatically generates invoices, ensuring timely billing and reducing the risk of missed or overdue invoices.
- User-Friendly Interface: Both HESCO and their clients benefit from a user-friendly interface that provides real-time access to inspection details, certificates, deficiency forms, and invoices.
- Integrated Analytics Dashboard: A powerful analytics dashboard offers comprehensive insights into current, future, and completed inspections, enabling informed decision-making and strategic planning.
Data Consultation and Analytics
Our partnership didn’t stop at just developing the platform. We provided extensive data consultation services to help HESCO leverage the power of analytics. Through our consultation, we identified key performance indicators (KPIs) and established a framework for continuous improvement.
- Data Collection and Analysis: We helped HESCO implement robust data collection methods, ensuring accurate and comprehensive data was available for analysis.
- Real-Time Monitoring: The analytics dashboard we integrated allows real-time monitoring of inspections, helping HESCO stay on top of their operations.
- Predictive Insights: Using advanced analytics, we provided predictive insights that enable HESCO to anticipate potential issues and take proactive measures.
- Performance Metrics: Our analytics tools track performance metrics, helping HESCO identify trends, measure efficiency, and make data-driven decisions.
Outcome
Our web solution, combined with our data consultation services, revolutionized HESCO’s business, replacing their manual processes entirely. Tasks that used to take nearly two days for inspection work now take just two hours, thanks to the automation features of our platform. Manual task assignment, progress tracking, and data management have been completely eliminated, saving time and minimizing human error.
The analytics dashboard provides a clear overview of tasks, offering comprehensive insights with just a few clicks. This allows HESCO to monitor performance, identify trends, and make data-driven decisions that drive efficiency and growth.
Clients now enjoy a transparent and user-friendly online platform, simplifying communication and enhancing their overall experience. The result is optimized operational efficiency, elevated customer satisfaction, and fostered business growth for HESCO.
Our partnership with HESCO showcases our expertise in developing cutting-edge solutions that address real-world challenges in the manufacturing sector. By leveraging advanced analytics and automation, we transformed HESCO’s safety inspection process, delivering significant improvements in efficiency, accuracy, and customer satisfaction.
Seeking a Similar Transformation for Your Company with Analytics in Manufacturing?
How You Can Implement Analytics in Manufacturing?
Implementing analytics in your manufacturing processes doesn’t have to be overwhelming. By taking a structured approach, you can seamlessly leverage analytics use cases in manufacturing, making your business streamlined, profitable, and data-driven.
However, as a trusted digital transformation services company, we understand the challenges involved with the implementation process. But don’t worry; we have got you covered! Here’s a step-by-step guide to get you started:
Assess Your Current State
First, you need to evaluate your existing processes. Look at every aspect of your manufacturing operations and identify areas where data-driven insights could make a difference. Are you experiencing frequent equipment failures? Is quality control a constant challenge? Understanding your current state will help you pinpoint where analytics can provide the most value.
Steps to Take:
- Conduct a thorough review of your production processes.
- Identify key pain points and inefficiencies.
- Gather feedback from your team to understand operational challenges.
Define Clear Objectives
Next, set specific goals for what you want to achieve with analytics in manufacturing. Do you want to reduce downtime, improve product quality, or streamline your supply chain? Having clear objectives will guide your analytics strategy and ensure you select the right analytics use cases in manufacturing.
Steps to Take:
- Set measurable goals, such as reducing downtime by 20% or increasing product quality by 15%.
- Prioritize objectives based on their potential impact on your business.
- Ensure your goals align with your overall business strategy.
Partner with a Trusted Digital Transformation Services Company
Choosing the right partner is critical to the success of your analytics initiatives. A trusted company can provide the expertise, tools, and support you need to implement and scale analytics in your manufacturing operations.
They can help you navigate the complexities of data integration, software selection, and process optimization via technology consulting services. Hence, always partner with a company to get assistance for choosing and implementing the best analytics use cases in manufacturing for your business.
Steps to Take:
- Research and identify reputable digital transformation services companies with experience in manufacturing.
- Evaluate their track record, client testimonials, and case studies to ensure they have the expertise you need.
- Partner with a company that offers comprehensive services, from initial assessment to ongoing support and optimization.
Read More: How to Hire a Digital Transformation Company?
Collect and Centralize Data
To make informed decisions, you need to collect data from various sources within your manufacturing operations. This includes data from machines, sensors, and ERP systems. Centralizing this data is crucial for comprehensive analysis. Once again, a trusted transformation partner will help you identify and collect relevant data from various touchpoints. You can leverage data consultation to streamline this step.
Steps to Take:
- Implement data collection systems across your production line.
- Integrate data from different sources into a centralized database.
- Ensure data quality and consistency for accurate analysis.
Start Small and Scale
Begin with a pilot project in one area of your manufacturing operations. This allows you to test the concept and demonstrate the value of analytics before scaling up. Choose an area where you can quickly see results, such as predictive maintenance or quality control.
Steps to Take:
- Identify a suitable area for your pilot project.
- Implement analytics tools and processes in this area.
- Monitor the results and make adjustments as needed.
Invest in Training
Your team needs the skills to interpret and act on the insights provided by your analytics tools. Invest in training to ensure everyone understands how to use the new systems and make data-driven decisions.
Steps to Take:
- Provide training sessions for your team on the new analytics tools.
- Offer ongoing support and resources to help them become proficient.
- Encourage a culture of continuous learning and improvement.
Ready to Transform Your Manufacturing Operations Using Analytics Services?
How Can Matellio Help?
At Matellio, we understand the unique challenges and opportunities in implementing analytics use cases in manufacturing. Our team of experts is dedicated to helping you harness the power of data to transform your operations. Here’s how we can support your journey:
Custom Solutions Development
We design and develop tailored manufacturing analytics software that addresses your specific needs and integrates seamlessly with your existing systems.
Data Analytics Services
Our team offers data analytics services to help you collect, process, and analyze your manufacturing data to extract actionable insights.
AI Integration Services
We leverage cutting-edge artificial intelligence and machine learning techniques to enhance your predictive capabilities and decision-making processes.
IoT Consulting Services
Our IoT consulting services experts can help you implement and optimize sensor networks to collect real-time data from your manufacturing floor.
Digital Transformation Services
We provide comprehensive support to guide your organization through the digital transformation process, ensuring you’re equipped to thrive in the data-driven manufacturing landscape.
Technology Consulting Services
Our consultants work closely with you to develop a strategic roadmap for implementing analytics in your manufacturing processes.
Support and Maintenance
We offer continuous support to ensure your analytics systems remain effective and up-to-date as your business evolves.
By partnering with Matellio, you gain access to a team of experienced professionals dedicated to your success. We’re committed to helping you leverage the full potential of analytics use cases in manufacturing to drive efficiency, quality, and innovation in your operations.
Conclusion
As we’ve explored throughout this article, analytics use cases in manufacturing are not just a trend – they’re a fundamental shift in how successful manufacturing operations are run. From predictive maintenance and quality control to supply chain optimization and sustainability efforts, analytics touches every aspect of modern manufacturing.
Moreover, when combined with cutting-edge technologies like AI, IoT, cloud computing, and edge computing, the potential of manufacturing analytics expands exponentially. These technologies work synergistically with analytics to create smarter, more responsive, and more efficient manufacturing ecosystems.
However, embarking on this analytics journey doesn’t mean you have to go it alone. As a leading provider of technology consulting services and custom enterprise solutions development, Matellio is here to guide you every step of the way.
Contact us to learn how our tailored analytics solutions can revolutionize your manufacturing operations and propel your business to new heights of success.
FAQs
Real-world examples include predictive maintenance, quality control and defect detection, supply chain optimization, demand forecasting, and energy management. These use cases help manufacturers improve efficiency, reduce costs, and enhance product quality. Analytics uses data from sensors and IoT devices to predict equipment failures before they happen. This allows manufacturers to perform maintenance proactively, reducing downtime, extending machinery lifespan, and cutting repair costs. The four main types of analytics used in manufacturing are descriptive analytics (what happened?), diagnostic analytics (why did it happen?), predictive analytics (what could happen?), and prescriptive analytics (what should we do?). Data collection involves gathering information from machines, sensors, and ERP systems. Centralizing this data in a single database allows for comprehensive analysis, ensuring data quality and consistency for accurate insights. A digital transformation services company provides expertise in data integration, software selection, and process optimization. They offer comprehensive support, from initial assessment to ongoing maintenance, ensuring successful implementation and scaling of analytics in your manufacturing operations. Q1. What are some real-world examples of analytics use cases in manufacturing?
Q2. How can analytics improve predictive maintenance in manufacturing?
Q3. What types of analytics are commonly used in manufacturing?
Q4. How does data collection and centralization work in manufacturing analytics?
Q5. Why should I partner with a digital transformation services company to implement manufacturing analytics?