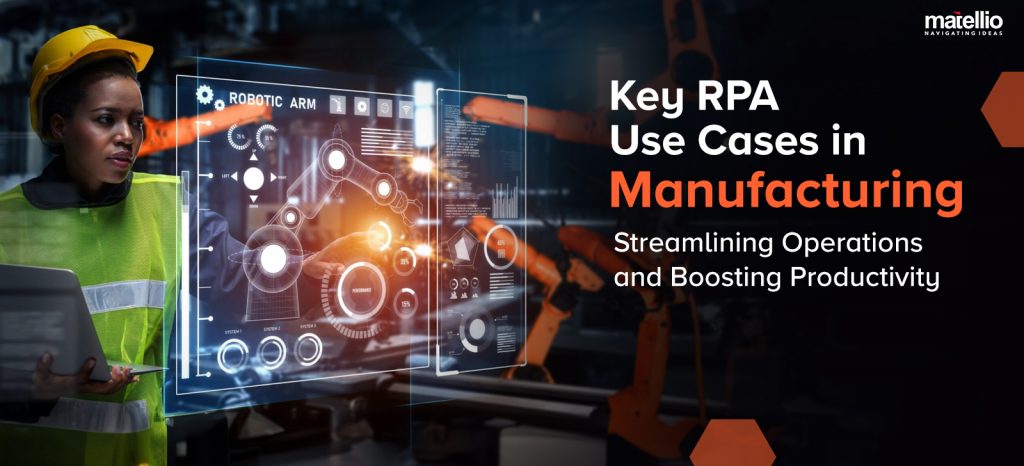
Do you ever feel like your manufacturing facility is overwhelmed with repetitive tasks, inefficient processes, and ever-changing regulations? Struggling to manage inventory, ensure quality control, and keep up with production schedules? That’s exactly where RPA use cases in manufacturing come into play!
According to a trusted source, the market for RPA in manufacturing is projected to surpass $74.38 billion in 2030! And that’s just the beginning!
Companies across the world are leveraging robust RPA development services to automate mundane tasks and facilitate process automation in manufacturing. Other than that, RPA use cases in manufacturing also streamline processes, reduce costs, and free up valuable time for production teams. Intrigued?
But what exactly is RPA in manufacturing, and how is it transforming the industry landscape? Moreover, how can you utilize RPA use cases in manufacturing to resolve your operational challenges and step into a more digital world? Let’s uncover answers to all such questions in our blog below!
What is RPA in Manufacturing?
In simpler terms, RPA uses software robots, or bots, to automate repetitive, rule-based tasks across various computer applications. RPA use cases in manufacturing are numerous and impactful, offering significant benefits for both production teams and manufacturing organizations.
In manufacturing, RPA can handle various administrative and operational functions, freeing up professionals to focus on strategic tasks.
Imagine a super-fast helper in your manufacturing facility who never gets tired and can follow instructions perfectly. That’s the main motto of RPA use cases in manufacturing. RPA uses software robots, basically computer programs running on machine learning algorithms, to automate repetitive tasks that staff usually do on computers.
Here’s how it works:
- Think of those boring, repetitive tasks like inventory management, order processing, or data entry. These are perfect for RPA.
- The RPA “helper” learns these tasks by watching how staff do them. It remembers the steps and can then repeat them super-fast and without mistakes.
- RPA can access different computer programs in your facility, just like a human staff member. This lets it move information around and complete tasks automatically.
- So, instead of an employee spending countless hours on repetitive tasks, the RPA “helper” can do it in seconds! This frees up the employees’ time to focus on more strategic initiatives.
And that’s just the start! Here are a few other benefits that you can achieve by leveraging RPA use cases in manufacturing:
Key RPA Use Cases in Manufacturing that You Can Use for Your Organization
RPA use cases in manufacturing are vast and impactful, offering significant benefits for both production teams and manufacturing organizations. Let’s delve into some key areas where RPA can revolutionize manufacturing operations.
1. Streamlining Inventory Management
Imagine a system that can automatically manage inventory levels, reorder supplies, and track shipments. This is exactly where RPA in manufacturing use cases shine. Here’s how RPA can transform inventory management:
Automated Inventory Replenishment
No more stockouts! This RPA manufacturing use case can automatically reorder supplies when inventory levels fall below a certain threshold, ensuring a consistent supply of materials.
Dynamic Inventory Tracking
RPA can continuously monitor inventory levels, track usage patterns, and predict future needs. This optimizes inventory management and minimizes production delays.
Efficient Warehouse Management
RPA can automate warehouse operations such as sorting, packing, and shipping, ensuring efficient use of space and resources.
By automating these tasks, RPA creates a more efficient and accurate inventory management process, reducing costs and improving productivity.
2. Simplifying Order Processing and Management
Order processing and management can be a lengthy and error-prone process. But that’s not the case with RPA in manufacturing. Here’s how RPA use cases in manufacturing can simplify it:
Automated Order Entry
RPA in manufacturing can extract order information from various sources and electronically transfer it to the order management system. With RPA as a Service, this process becomes even more scalable and efficient, eliminating manual data entry errors and saving valuable staff time.
Seamless Order Tracking
This particular RPA use case in manufacturing can seamlessly track orders from placement to delivery, ensuring accurate and timely fulfillment.
Automatic Order Updates
RPA can automatically update order statuses and notify customers of changes, improving transparency and customer satisfaction.
This not only streamlines the order processing but also enhances customer experience by providing accurate and timely information.
3. Automating Quality Control Processes
Quality control involves a high volume of data entry, inspection, and verification, and they are prone to errors and delays. Here’s how RPA use cases in manufacturing can significantly improve this process:
Automated Data Collection and Analysis
RPA bots can automatically collect and analyze data from production lines for quality control purposes. This ensures accurate and timely quality checks based on the latest standards.
Error Identification and Correction
RPA can identify potential defects before products reach the market, preventing recalls and ensuring high-quality products.
Automated Compliance Reporting
RPA in manufacturing can automate the generation of compliance reports, ensuring adherence to industry regulations.
By automating these tasks, RPA streamlines quality control processes, reduces errors, and ensures consistent product quality.
4. Enhancing Supplier and Vendor Management
RPA in manufacturing can ensure timely and efficient communication with suppliers and vendors by:
Automated Supplier Onboarding
RPA can streamline the onboarding process for new suppliers by automating data collection and verification.
Seamless Vendor Communication
RPA can automate routine communications with suppliers and vendors, ensuring timely responses and updates.
Efficient Contract Management
RPA can manage contracts, track renewals, and ensure compliance with terms and conditions.
This not only improves supplier and vendor relationships but also ensures smooth supply chain operations.
5. Optimizing Supply Chain Management
Managing the complex manufacturing supply chain involves numerous tasks, including inventory management, order processing, and restocking. RPA in supply chain use cases can automate these processes, leading to:
Optimized Inventory Levels
RPA can analyze historical data and predict future needs to maintain optimal inventory levels, preventing stockouts or overstocking of critical supplies.
Reduced Supply Chain Costs
Streamlined ordering processes and minimized stockouts can lead to significant cost savings in the manufacturing supply chain.
Improved Availability of Supplies
Automating inventory management ensures the timely availability of essential supplies for production.
6. Enhancing Production Line Automation
Production workflows can benefit significantly from RPA automation. RPA use cases in manufacturing can automate tasks like:
Automated Production Scheduling
Automating production scheduling ensures optimal use of resources and minimizes downtime.
Seamless Data Integration
RPA can integrate data from various production systems, ensuring real-time visibility into production processes.
Automated Equipment Maintenance
RPA can schedule and manage equipment maintenance tasks, ensuring timely upkeep and minimizing breakdowns.
In short, you can invest in RPA development services to move toward production line optimization and process automation in manufacturing.
7. Empowering Virtual Assistants for Production Support
RPA in manufacturing can power virtual assistants that provide support for production teams by:
Continuous Monitoring of Production Metrics
Virtual assistants can monitor production metrics and alert teams of any anomalies or deviations from set standards.
Immediate Response to Production Inquiries
Virtual assistants can answer routine production questions and concerns, reducing the burden on production managers.
Improved Production Efficiency
By investing in conversational AI services, along with RPA in manufacturing, you can create virtual assistants that can provide teams with real-time data and insights, promoting efficiency.
8. Enabling Remote Monitoring of Manufacturing Processes
Lastly, you can also leverage RPA manufacturing use cases to manage remote monitoring systems. This integration empowers you to:
Collect and Analyze Production Data
This RPA use case in manufacturing can automatically collect and analyze production data, such as machine performance and production output.
Proactive Maintenance Management
By identifying trends and potential issues in production data, RPA can facilitate proactive maintenance interventions.
Early detection of production issues through remote monitoring can lead to better production outcomes and reduced downtime.
By implementing these RPA manufacturing use cases, you can create a more efficient, cost-effective, and productive manufacturing environment.
Ready to Implement RPA in Manufacturing? Get a Free 30-Min Consultation!
How to Leverage RPA Use Cases in Manufacturing for Your Organization?
So, we have explored the top RPA use cases in manufacturing. But how can you leverage them for your organization? In other words, how can you implement RPA in your manufacturing facility?
Implementing RPA in your manufacturing organization can seem daunting, but partnering with a trusted technology consulting services company can make the process seamless and effective. Here’s a detailed guide on how to leverage RPA use cases in manufacturing and the steps you need to follow:
1. Assessing Business Needs
Before diving into RPA implementation, it’s essential to thoroughly assess your business needs. This involves understanding the specific pain points and inefficiencies in your current processes that RPA can address. Here’s how to conduct a comprehensive assessment:
- Identify which areas do you need to optimize by implementing RPA use cases in manufacturing. Is it inventory management, warehouse management, order processing and supplier management, or something else?
- Define what you aim to achieve with RPA. This could be reducing operational costs, improving production efficiency, increasing quality, or ensuring compliance.
- Know the basic challenges faced by your workers and IT managers and assess how those can be resolved via RPA development services.
- Evaluate the technical feasibility of implementing RPA for the identified processes.
2. Partnering with a Trusted Technology Consulting Services Company
Choosing the right partner is critical to the success of your RPA implementation. A trusted technology consulting services company brings expertise, experience, and a proven track record to the table.
However, selecting the right technology consulting services company is critical for your project’s success. Here’s what to look for:
- Proven Track Record: Look for a company with expertise in custom manufacturing software development. The company should also be well-versed in using next-gen technologies like AI, RPA, IoT, etc., for your manufacturing solution. Check case studies and client testimonials to gauge their expertise.
- Industry-Wide Knowledge: Ensure the company has skilled RPA developers and is well-versed with the manufacturing software development landscape. This ensures they can provide solutions tailored to your needs.
- Comprehensive Services: The company should offer end-to-end digital transformation services, from initial assessment and design to implementation, training, and ongoing support.
- Flexibility and Scalability: Choose a partner that can scale their services as your needs evolve. This ensures you can expand your RPA efforts without switching providers.
3. Analyzing the Latest Tech Trends
Staying updated with the latest RPA trends is crucial to making informed decisions. However, identifying the latest yet reliable technology trends can be a daunting task. But do not fear; we have got you covered! As a trusted technology partner, we have listed some trustworthy trends that you can adopt for your RPA solution:
- AI Integration: Combining RPA with AI development services can enhance automation capabilities, enabling bots to handle more complex tasks that require decision-making and pattern recognition.
- Digital Twin Testing: Refine your RPA before deployment by simulating production scenarios with a virtual replica of your factory floor.
- Predictive Maintenance with ML: Leverage RPA and Machine Learning development services to analyze real-time sensor data and trigger preventative actions before equipment failure disrupts production.
- Cobots for Seamless Collaboration: Free your human workforce for higher-value tasks by integrating cobots (collaborative robots) to handle repetitive tasks alongside RPA automation.
- Edge Computing Boosts Speed: Minimize latency issues by bringing processing power closer to the factory floor with edge computing, allowing RPA systems to make real-time decisions and optimize automation efficiency.
4. Following the Agile Methodology
Adopting an agile approach to RPA implementation allows for flexibility and continuous improvement. Here’s how to apply the Agile methodology:
- Iterative Development: Break the implementation process into smaller, manageable phases. This allows for incremental progress and makes it easier to address any issues that arise.
- Regular Feedback: Engage stakeholders regularly to gather feedback on each phase. This ensures the solution meets their needs and allows for adjustments based on real-world usage.
- Continuous Improvement: Use the feedback to continuously refine and improve the RPA solution. This iterative approach ensures the final product is robust and effective.
5. Testing and Maintenance
Thorough testing is crucial to ensure your RPA implementation works as intended. Here’s how to approach testing and maintenance:
- Comprehensive Testing: Conduct extensive testing of the RPA solution in a controlled environment. This includes functional testing, performance testing, and security testing to identify and resolve any issues.
- Pilot Programs: Launch a pilot program to test the solution in a real-world setting. This allows you to gather feedback and make necessary adjustments before full-scale deployment.
- Ongoing Maintenance: Regular maintenance is essential to keep the RPA solution running smoothly. This includes software updates, monitoring performance, and addressing any issues that arise.
A trusted consultancy always offers testing as an integral part of their RPA development services package. So, choose wisely!
Other Challenges to Resolve and How We Can Help?
So, you are all set to move ahead with RPA use cases in manufacturing. However, even after following this implementation process, there might be challenges you must address for a successful implementation.
That’s where we come in!
As a trusted RPA development services provider, we can help you tackle every major and minor challenge that you discover in your transformation journey. Here’s why to choose us for implementing RPA in manufacturing:
Expert Team
Certified RPA developers with deep manufacturing knowledge for tailored solutions.
Beyond Consulting
We design and craft RPA solutions, not just recommend them.
Comprehensive Services
From start to finish, we handle needs assessment, design, implementation, training, and ongoing support.
Seamless Integration
We integrate RPA smoothly with your existing manufacturing IT systems.
Flexible Engagement
Choose the model that fits you, from full-service projects to ongoing RPA bot support.
Get a Free 30-Minute Consultation and a Custom Quote for Your RPA Project!
Conclusion
Implementing RPA in manufacturing is a strategic move that can significantly improve operational efficiency and productivity. By partnering with a trusted technology consulting services company, assessing your business needs, analyzing the latest tech trends, following the agile methodology, and providing comprehensive training, you can successfully leverage RPA use cases in manufacturing.
Ready to transform your manufacturing operations with RPA? Contact us today for a free 30-minute consultation and discover how our RPA solutions can benefit your organization. Embrace the future of manufacturing with RPA and experience unparalleled efficiency and productivity.
FAQ’s
Q1. What is the use case of RPA in manufacturing?
RPA in manufacturing automates repetitive, rule-based tasks such as inventory management, order processing, and quality control, improving efficiency and reducing errors.
Q2. What are the common RPA examples in manufacturing?
Common RPA examples in manufacturing include automated inventory replenishment, order entry, quality control data analysis, supplier communication, and production scheduling.
Q3. How much does it cost to implement RPA in manufacturing?
The cost to implement RPA in manufacturing depends on various factors such as the complexity of processes and the number of bots required. Contact us to get a free quote.
Q4. What steps do you take to protect our business data?
We use robust security protocols, including data encryption, secure access controls, and regular audits, to protect your business data and ensure compliance with industry standards.
Q5. What other services do you offer?
In addition to RPA development, we offer AI integration, cloud-based solutions, process mining, digital transformation consulting, and comprehensive IT support services.