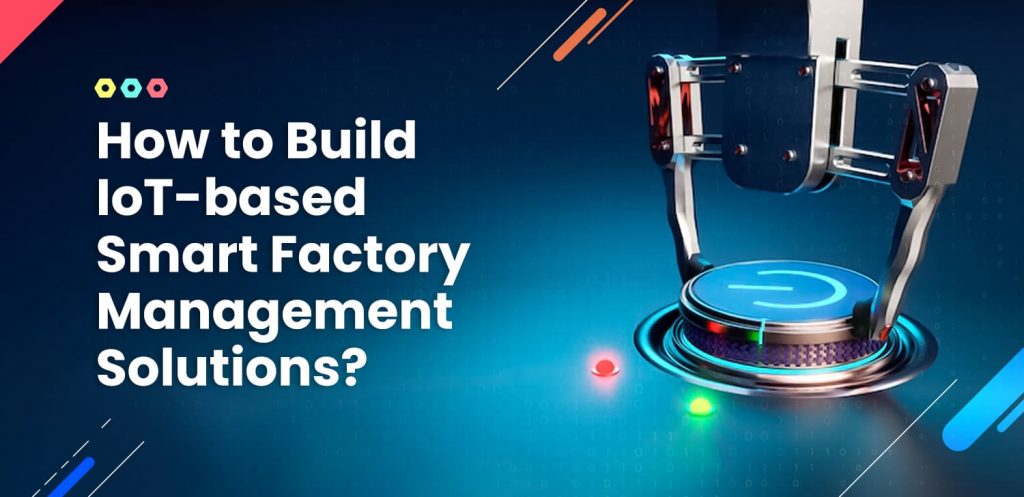
IoT-based smart factories are helping manufacturers around the globe improve their production lines, workforce efficiency, and productivity. In today’s day and age, when quality and quantity both matter to the end-users, factories must produce as many products as possible and meet a certain quality benchmark. To meet the staggeringly high demand in a short time window, companies must eliminate all types of wastage and inefficiencies from their production processes and turn their factories into well-oiled machines. In other words, they need digital transformation.
Manufacturing is one of the biggest industries in the world, and there are several components factories need to complete their digital transformation: IoT, AI, robot automation, big data, and industrial analytics. IoT and automation are the key elements in any company’s digital transformation efforts. With the help of IoT, companies can streamline their manufacturing processes and improve their staff management and back-end processes. It is clear that IoT sits in the middle of industrial digital transformation, and as a result, a new subset of IoT has emerged: Industrial Internet of Things (IIoT).
The global market for IIoT was valued at over $263 billion in 2028, according to stats posted by Statista, and is expected to reach $1.1 trillion by 2028. These numbers clearly show a growing corporate interest and faith in IIoT. Smart factories are the factories of the future that offer heightened overall efficiency and improved product quality. And in today’s article, we will learn what smart factories are, their benefits, and how you can make your factory smart too.
What is a Smart Factory?
Smart factory is a term used to describe an environment in which various machines and equipment are connected to each other. Different types of modern and next-gen technologies are clumped together to automate workflows and make the manufacturing and the surrounding processes more streamlined, flexible, and efficient. Smart factories use technologies such as AI, robotics, data analytics, etc., to create a hyperflexible and self-adapting environment. However, the benefits of smart factories are not just limited to production floors. From logistics to inventory and asset management, smart factories cover all their bases to ensure maximum efficiency.
To understand how smart factories work, consider the following example:
An international sneaker brand has finally decided to get with the times and go digital. They have turned one of their factories into a smart factory. Now, when we call it smart, we mean that all types of wastages and inefficiencies have been plucked out of the manufacturing and related process. This means that robot arms work on parts of the manufacturing processes that don’t require human beings on the production line. The asset management solutions ensure that all the machines and robots are in fine condition. Real-time data tracking lets these solutions have the most recent data about the health of machines and robots. And using AI, they can predict if a failure or a fault is imminent. If a machine is about to break down, then an alert can be issued to the mechanics, and they can go and service the devices in question before they cause any problem. This way, the production kept going.
Read More: Why Digital Asset Management System for Your Business?
Similarly, logistics and inventory can be streamlined. In-coming and out-going deliveries can be tracked. For instance, if there is a component in the sneakers that a different company manufactures, our company can track their order and ensure timely delivery. Furthermore, for big factories, storage is always an issue. Knowing how much storage space they have, how many orders they have to fulfill, and other such problems can be solved with smart factories.
It’s not hard to see that by choosing to build a smart factory, our sneaker company dwindled the chances of a production halt due to machine failure and sped up the overall production process by automating and monitoring all the related processes.
Now that we understand what smart factories are, we can go back to a previous point and discuss what components they usually have. As we said, smart factories are a collection of different next-gen and latest technologies working together. But how are they connected? What is that one thing that links all these various technologies together and governs them? The answer is IIoT.
What is IIoT?
Industrial Internet of Things (IIoT) is just like any other IoT implementation like smart homes, smart hospitals, smart retail stores, etc. The difference is that since manufacturing is such a vast industry and has so many use-cases where IoT can help, it felt like we needed a whole new brand of IoT, something specific to the manufacturing industry.
IIoT is a network of internet-enabled factory-grade equipment and machines, sharing data with each other and streaming it back to the server in real-time. Various devices and machines should be connected for all of this to work. The idea is to minimize human intervention. So these connected devices must be smart enough to take smaller decisions on their own and adjust based on the data received. This self-adjusting nature of a smart factory is particularly beneficial for the owners as it makes sure that the production never grinds to a halt.
What are the Benefits of IIoT?
Aside from sensors and IIoT devices, a key component of a smart factory is the IIoT-management software. IoT-based management software is essential for managers to control their factories remotely. The real-time data sent by the factory machines can be accessed from a well-designed UI. Furthermore, with the help of AI, managers can get critical analytics such as asset efficiency, power consumption, waste management, inventory and logistics management, etc. Managers can quickly sift through a vast amount of data, retrieve trends, and study behaviors. With the help of this information, managers can improve their management policies, worker policies, etc. Asset management, human and otherwise, also becomes easier. Asset tracking is child’s play with IIoT; you can find out where any device or employee is with tracking devices. Automatic doors and the facial-recognition technologies can help you keep track of your employees.
Companies these days are very aware of their environmental impact. In fact, in many countries, factories must adhere to strict environmental laws or face legal action. IIoT helps companies in reducing their carbon footprint. With the help of smart HVAC and lighting systems, factories can ensure minimum power wastage. Taking it a step further, various types of sensors can help companies detect their wastage, solid, liquid, and gas. With IIoT implementation, factories can find out the harmful constituents of the smoke and treat them before releasing it into the atmosphere via their chimneys. The same can be done in the liquid and solid waste departments. Companies usually go to great lengths to ensure that they don’t release harmful or toxic wastage into rivers and other water sources. Solid waste must be marked properly, and whatever can be recycled must be. IIoT can help with all of that. Furthermore, if there is an unknown component in the waste that has not been detected before, then, thanks to AI-based analytics, it will be flagged on the manager’s IoT software. Managers can investigate the matter and fix the issue.
How to Build a Smart Factory Solution?
To build a smart factory, you need multiple components. Simply installing net-enabled devices and a mediocre software layer to control it is not enough and is a waste of money and time. If you want to generate better revenues and streamline your factories, you must consider all the use-cases and commit to your factory’s digital transformation.
Given below is everything you need to know to get started. However, keep in mind that the following points aren’t set in stone. At the end of the day, how you approach your IIoT implementation process will depend on the type of factories and your business. Also, the IoT partner you decide to team up with will have its own processes to achieve the final goal.
1. Define the Need
Every business is different and has unique requirements. So you need to analyze your business and factories and figure out your key pain points. For instance, not all the processes in a prediction line can be done by robot arms. There are some parts that require a more human touch. Additionally, some processes are prone to errors or require precision; those processes are better automated with robot arms. So you must know your factories inside and out before committing to something as big as IIoT implementation. It is a big undertaking and can turn into a disaster if you’re not careful. So, define your IoT goals.
Figure out what your pain points are and make a priority list. IIoT, like any traditional IoT, will create a lot of disruption in your factory. A factory-wide implementation will lead to a complete production shutdown. So it’s better to implement IIoT in phases to minimize productivity disruption.
Your goals, pain points, and priority list will form the basis of your entire journey. Sure, the goals can change throughout IoT development and implementation, but they hardly take one eighty-degree turn. So you must have clarity about your goals before moving forward.
2. Research and Plan
Once you know what goals you want to achieve, it’s time to look for solutions that can help you achieve them. The best way to do so is by conducting extensive market research. Read case studies about other manufacturers on how they completed their digital transformation. The idea is to learn from their experience and mistakes. Reading their case studies will give you information like what IoT development firms they partnered with, what were the things they learned from their digital journey, etc. This also allows you to avoid making the mistakes they made. You can learn from different companies and then figure out how you want to achieve your digital transformation.
Another reason to conduct market research is to find out what solutions are available to you. The digital transformation market is vast, and not every solution is meant for your company. As we said, different businesses have unique requirements. Market research will let you find out solutions that can help you with your pain points.
Next, it’s time to put your research to use and build a digital transformation plan. Depending on the priorities list, you must decide what type of solution you want to develop. For instance, if you simply want to achieve asset management and remote control initially, you will either need IoT-based devices that can not only locate your asset but give you the power to turn them on and off remotely. These devices are usually mounted inside the machines, where they have access to key parts of the internal machinery. Or you will have to buy smarter devices that are net-enabled. Based on your choice of devices, you will also need the data management and a UI for your managers.
While having a plan of your own is essential, it can greatly benefit from the experienced eyes of an IoT expert. Your IoT expert will help you mature your plan and improve upon it during the initial stages.
Read More: IoT-based Home Automation Development: What’s in it for Businesses?
3. Hire an IIoT Development Company
An experienced IIoT development company with the right talent and tools is essential for the success of your IIoT implementation project. IIoT is harder to implement than vanilla IoT because of the steep precision and efficiency requirements. So hiring the best IoT development company to help you achieve your digital transformation goals is a must.
There are many talented IIoT software solution developers and consultants on the market who provide great services. But you must find an IoT partner who can meet your requirements. A great way to find such an IoT developer is with the help of sites like Clutch. Also, take a look at their websites. Most good technology partners showcase the best work on their portfolios, and they can give you a great idea about the projects they have done in the past.
4. Develop, Test, Deploy, and Repeat
IIoT implementation is a long and complicated process and can take some time. To ensure maximum value for your investment, it’s best that you first ask your IoT developer to build your Proof of Concept (POC) or Minimum Viable Product (MVP). A POC will show you whether the proposed architecture and devices work and meet your goals or not. If the POC is not working up to the mark, then your developers can rework and improve. Similarly, MVP helps you get initial feedback on your products. In the case of IIoT, an MVP will mean a leaner version of your IIoT implementation will be made available to your employees. They will work with it for a while, and according to their feedback, you can change things for the final solution.
After development comes testing and then deployment. Testing is essential for any digital transformation project to ensure no bugs or cracks in the server have been left for the hackers to exploit.
The journey doesn’t end at deployment, though. You have probably only crossed off one or two points on your priority list at this stage. So, once everything about the previous release settles down and things start working as they should, you can get started on the next item. Of course, you won’t be starting from scratch this time, and you will also have your experience and which will prevent you from making the same mistakes.
Also Read- IoT Software Development: A Complete Guide
Conclusion
Smart factories can help manufacturers become more efficient and streamlined. IIoT helps increase the speed and quality of the production and helps with back-office and logistics workflows. And if you are looking to turn your factory into a smart factory, then Matellio is the right IIoT partner for you.
We have years of experience developing state-of-the-art IIoT digital solutions for factories big and small. We offer flexible digital transformation services and various hiring models to ensure we cater to businesses of all sizes. Our experienced and talented IoT developers excel at analyzing the requirements of a factory and coming up with the most efficient and elegant solution for your clients. We work on the Agile development methodology, which allows us to put our customers at the center of our development process.
If you want to learn more about our IIoT software solution development services, click here.